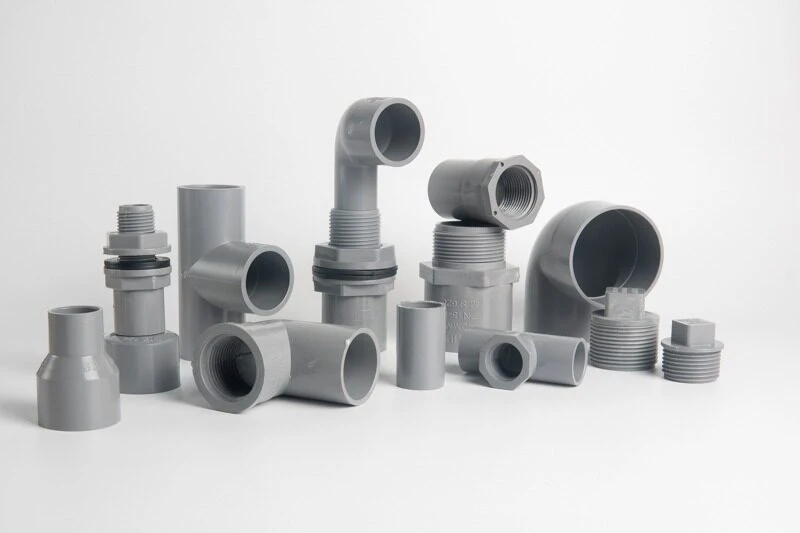
Introduction
PPR pipes and fittings are increasingly recognized for their utility in various industrial applications, including scientific refractories. Known for their durability and resistance to harsh environments, these materials play a critical role in enhancing the efficiency and safety of refractory systems. Let’s explore their significance in this field.
What are PPR Pipes?
PPR stands for Polypropylene Random Copolymer. Unlike traditional materials, PPR does not corrode, providing a longer lifespan and lower maintenance costs.
Advantages of Using PPR Pipes and Fittings
- Corrosion Resistance: PPR is impervious to many chemicals and will not rust, making it ideal for aggressive environments.
- Thermal Stability: PPR can handle temperature fluctuations without compromising its structural integrity.
- Lightweight and Durable: The lightweight nature of PPR facilitates easier handling and installation, while its durability ensures a long service life.
Installation Guidelines for PPR in Refractory Systems
Preparation Steps
Before installation, ensure that the site is clean and all necessary tools and materials are on hand. Proper planning will streamline the process and minimize errors.
Maintenance of PPR Systems in Refractory Applications
Regular inspections are vital to maintaining the integrity of PPR systems. Look for signs of wear or leaks and address them promptly to avoid operational disruptions.
Environmental Considerations
PPR materials are recyclable, making them a sustainable choice for industrial applications. Their longevity reduces waste, aligning with eco-friendly practices.
Future Trends in PPR Technology
Innovations in PPR technology continue to enhance its performance and applicability in various industries, including refractories.
Conclusion
PPR pipes and fittings offer numerous advantages for scientific refractory applications, including durability, resistance to corrosion, and thermal stability. Their adoption can significantly enhance the efficiency and safety of refractory systems, making them an excellent choice for modern industrial needs.
FAQs
- What makes PPR suitable for high-temperature applications?
- PPR has excellent thermal stability and can withstand temperature fluctuations without damage.
- How do I install PPR pipes in a refractory setting?
- Use socket fusion or electrofusion methods, ensuring proper alignment and heating.
- Are PPR pipes resistant to chemicals?
- Yes, PPR pipes are highly resistant to many chemicals, making them suitable for harsh environments.
- Regular inspections for wear or leaks are essential for maintaining system integrity.
- Yes, PPR is recyclable, contributing to its sustainability as a material choice.