Introduction: The Essence of Butt Welding in HDPE Applications
Butt welding machines for HDPE pipes and fittings have emerged as a cornerstone in the field of plastic piping systems, offering unparalleled joint integrity and operational efficiency.
Key Features: Precision and Versatility in One Machine
These machines utilize electric, hydraulic, or pneumatic power sources to generate the heat necessary for fusion welding. Key features include adjustable clamping systems that accommodate various pipe diameters, precise temperature control mechanisms, and automated or semi-automated welding processes that reduce human error and enhance productivity.
Benefits: Ensuring Joint Integrity and Operational Efficiency
The benefits of using butt welding machines for HDPE pipes and fittings are numerous. This, in turn, leads to operational efficiency, cost savings, and environmental sustainability.
Types and Applications: Tailoring Solutions to Fit Specific Needs
From manual, semi-automatic, to fully automatic machines, the choice depends on factors such as the size and complexity of the project, the skill level of the operators, and the desired level of automation. Applications range from large-scale water distribution networks and sewage treatment plants to smaller-scale irrigation systems and industrial fluid handling.
The Future: Advancements and Innovations in Butt Welding Technology
The future of butt welding machines for HDPE pipe and fittings is bright, with ongoing advancements and innovations driving the industry forward. Manufacturers are continuously refining their designs to improve welding accuracy, increase automation levels, and reduce operational costs.
Their key features, benefits, types, and applications make them an indispensable tool in the HDPE piping industry.
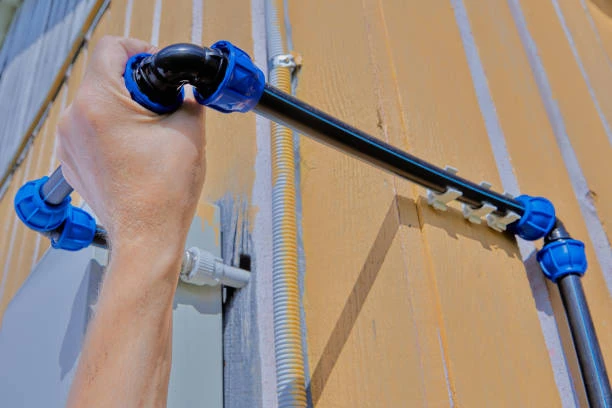
BS 6572: Setting the Standard
The British Standard BS 6572 provides comprehensive guidelines for the design, manufacture, and performance of butt welding machines for HDPE pipes and fittings. This standard ensures that welding equipment meets the highest quality standards, capable of producing joints with strength and reliability comparable to the pipe material itself. Key aspects covered by BS 6572 include:
- Machine Design and Construction: Specifications for the materials used in the construction of the welding machine, ensuring durability and precision.
- Operational Parameters: Detailed guidelines on the temperature control, pressure application, and welding cycle times to achieve optimal fusion.
- Testing and Verification: Procedures for testing the machines to validate their performance against predefined criteria, including tensile strength, burst pressure, and environmental stress crack resistance.
- Safety Requirements: Measures to safeguard operators from potential hazards during machine operation and maintenance.
Advantages of Using BS 6572-Compliant Machines
- Consistency in Joint Quality: Compliance with BS 6572 ensures that each weld meets stringent quality standards, minimizing the risk of leaks and failures.
- Operational Efficiency: Standardized machines reduce the learning curve for operators, enhancing productivity and reducing downtime.
- Cost Savings: High-quality welds lead to longer service life for piping systems, minimizing the need for frequent repairs and replacements.
- Environmental Benefits: Efficient welding processes reduce waste and energy consumption, contributing to sustainable practices.
Types and Applications
Butt welding machines for HDPE pipe and fittings come in various types and configurations, tailored to meet the specific needs of different applications. Semi-automatic machines automate some aspects of the welding process, reducing human error and increasing productivity. Applications range from water distribution networks and sewage treatment plants to irrigation systems and industrial fluid handling. Each type of machine is designed to optimize welding performance and joint integrity for its intended use.
Conclusion
Butt welding machines for HDPE pipes and fittings, adhering to the British Standard BS 6572, are indispensable tools in ensuring the reliability and efficiency of industrial piping systems.As HDPE piping systems continue to gain traction across various industries, investing in high-quality, compliant welding equipment will be crucial in maintaining the integrity and performance of these critical infrastructure components
FAQs
- What is the difference between manual and automatic butt welding machines for HDPE pipes?
Manual machines require the operator to manually control the welding process, including clamping, heating, and pressing the pipe ends together. Automatic machines, on the other hand, automate these steps, reducing human error and enhancing precision. - How do I know if my butt welding machine complies with BS 6572?
Manufacturers typically provide certification and documentation证明 that their machines meet the requirements of BS 6572. Additionally, you can verify this by checking the machine’s specifications against the standard’s guidelines. - Can I use butt welding machines for other types of plastic pipes besides HDPE?
While butt welding machines are primarily designed for HDPE pipes, some models can be adapted for other thermoplastic materials like polypropylene (PP) and polyvinyl chloride (PVC). However, it’s essential to check the machine’s compatibility and adjust welding parameters accordingly. - What safety precautions should I take when operating a butt welding machine?
Always wear appropriate protective gear, such as gloves, safety glasses, and hearing protection. Ensure the work area is well-ventilated and free of flammable materials. Follow the manufacturer’s instructions for machine operation and maintenance to prevent accidents.