Polypropylene Random Copolymer (PPR) pipes have gained immense popularity in plumbing due to their durability, resistance to corrosion, and ease of installation. However, proper installation is crucial to ensure their longevity and efficiency. In this article, we will explore the key considerations for PPR Pipe installation, helping you avoid common pitfalls and maximize the benefits of this versatile material.
Understanding PPR Pipes
PPR pipes are a type of plastic piping commonly used for transporting hot and cold water in residential and industrial settings. They are lightweight, resistant to scaling and corrosion, and have a low thermal conductivity, making them a preferred choice for many plumbing applications. However, their performance largely depends on correct installation practices.
Key Considerations for PPR Pipe Installation
1. Material Quality
The quality of the PPR pipes and fittings is the foundation of a successful installation. Always source your materials from reputable suppliers who provide certified products. Look for pipes that meet relevant standards, such as ISO 15874, to ensure durability and performance.
2. Pipe Size and Flow Rate
Choosing the right pipe size is crucial for ensuring optimal flow rates and preventing issues like water hammer. Calculate the required diameter based on the intended use, flow rate, and pressure requirements of your system. Using pipes that are too small can restrict flow, while oversized pipes can lead to pressure drops.
3. Temperature Considerations
PPR pipes are designed to withstand specific temperature ranges. For hot water applications, ensure that the pipes can handle the maximum operating temperature without deforming. Installation in areas exposed to extreme temperatures should also be carefully planned to avoid thermal expansion issues.
4. Pressure Ratings
Understanding the pressure ratings of PPR pipes is essential for preventing failures. Check the pressure class of the pipes you’re using and ensure it aligns with the system’s requirements. Always account for potential pressure fluctuations that may occur during operation.
5. Installation Techniques
Proper installation techniques are critical to the integrity of the piping system. Some key practices include:
- Heat Fusion Welding: PPR pipes are typically joined using heat fusion, which involves melting the ends of the pipes and fittings to create a secure bond. Ensure that the equipment is calibrated correctly and that the proper temperature is maintained during the process.
- Proper Alignment: Misaligned pipes can lead to stress and eventual failure. Take the time to ensure that all pipes and fittings are correctly aligned before securing them.
- Support and Hanging: Adequate support is essential to prevent sagging or movement. Use appropriate hangers or brackets spaced according to manufacturer recommendations, typically every 2-3 feet.
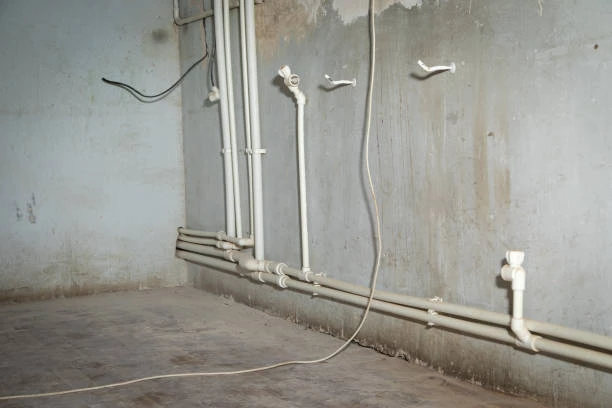
6. Expansion and Contraction
PPR pipes can expand and contract with temperature changes. It’s important to account for this movement during installation. Incorporate expansion loops or fittings where necessary to accommodate thermal expansion without putting stress on the joints.
7. Insulation
Insulating PPR pipes can help maintain the temperature of the fluids within and prevent heat loss in hot water systems. It can also reduce condensation in cold water systems, minimizing the risk of corrosion and water damage.
8. Environmental Considerations
Consider the environmental conditions where the pipes will be installed. Exposure to UV rays can degrade PPR pipes over time, so when installing outdoors, use UV-resistant coatings or protective measures.
9. Testing the System
After installation, it’s vital to conduct pressure tests to ensure that there are no leaks. Testing can help identify weak points or improper joints before the system goes live. Always follow the manufacturer’s recommendations for pressure testing procedures.
Common Mistakes to Avoid
- Ignoring Manufacturer Guidelines: Always follow the installation instructions provided by the manufacturer. Deviating from these guidelines can compromise the integrity of the system.
- Over-tightening Connections: Excessive force when tightening fittings can lead to cracks or other failures. Follow recommended torque specifications.
- Using Incompatible Materials: Mixing different types of materials can lead to failure at the joints. Ensure compatibility between PPR pipes and fittings or other piping materials.
- Neglecting Regular Maintenance: After installation, regular maintenance checks can help identify issues early and prolong the lifespan of your PPR piping system.
Conclusion
Proper installation of PPR Pipe is crucial for ensuring a reliable and efficient plumbing system. By considering factors such as material quality, pipe size, temperature, and pressure ratings, you can avoid common pitfalls and enhance the longevity of your installation. Regular maintenance and adherence to best practices will ensure that your PPR pipes serve you well for many years.
FAQs
1. What are the advantages of using PPR pipes?
PPR pipes are lightweight, resistant to corrosion, have low thermal conductivity, and are easy to install, making them ideal for various plumbing applications.
2. How do I determine the right size of PPR pipe for my project?
Calculate the required diameter based on the flow rate and pressure needs of your system, consulting manufacturer guidelines for specific applications.
3. Can PPR pipes be used for hot water supply?
Yes, PPR pipes are suitable for hot water applications, but it’s essential to ensure they are rated for the specific temperature you plan to use.
4. How often should I inspect my PPR piping system?
Regular inspections should be conducted at least once a year, or more frequently in high-use systems, to check for leaks or signs of wear.
5. What should I do if I notice a leak in my PPR pipes?
Immediately shut off the water supply and assess the leak. Depending on the severity, you may need to repair it yourself or call a professional plumber.