Introduction
The U.S. Navy continually seeks innovative solutions to enhance the efficiency, reliability, and performance of its submarines. In a significant step forward, Hunt Valve has announced its plans to 3D print valve assemblies specifically designed for Navy submarines. This cutting-edge approach promises to revolutionize the way valves are manufactured, maintained, and integrated into complex submarine systems. This article will delve into the implications of this development, the technology behind 3D printing valve assemblies, and the benefits it brings to naval operations.
Understanding Valve Assemblies
What is a Valve Assembly?
A valve assembly is a critical component in various mechanical systems, controlling the flow of fluids and gases within a system. In submarines, valve assemblies are essential for managing water, fuel, and air systems, ensuring optimal operation under extreme conditions.
Key Functions of Valve Assemblies in Submarines
- Flow Control: Regulating the flow of water and other fluids to maintain buoyancy and stability.
- Safety Mechanisms: Ensuring that critical systems can be shut down or diverted in emergencies.
- Pressure Management: Maintaining necessary pressure levels for various systems, such as ballast tanks and engine cooling.
The Importance of 3D Printing in Valve Assembly Production
Advantages of 3D Printing Technology
- Customization: 3D printing allows for the production of customized valve assemblies tailored to specific operational requirements of submarines.
- Reduced Lead Times: Traditional manufacturing methods can be time-consuming. 3D printing significantly reduces lead times, enabling faster prototyping and production.
- Complex Geometries: The technology can produce intricate designs that may be impossible to achieve with conventional machining.
- Material Efficiency: 3D printing generates less waste, as material is added layer by layer, minimizing excess.
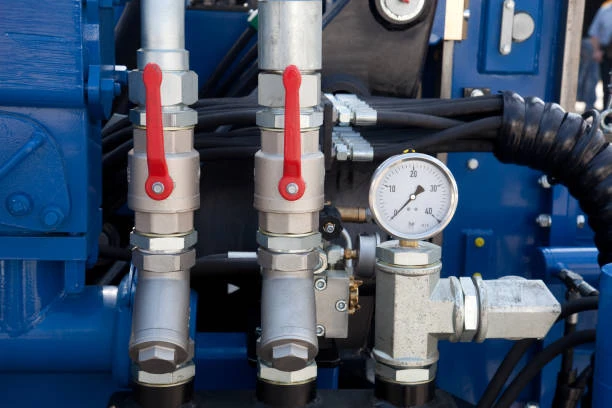
Applications in Submarine Operations
The integration of 3D printed valve assemblies into submarine systems can enhance performance and operational readiness in several ways:
- Rapid Repairs: The ability to quickly produce replacement parts means submarines can spend less time in dry dock and more time operational.
- On-Demand Manufacturing: Submarines could potentially manufacture parts on-site, reducing the need for extensive supply chains and inventories.
- Weight Reduction: 3D printing allows for the design of lighter components without sacrificing strength, which is crucial in submarine design where weight is a critical factor.
Hunt Valve’s Approach to 3D Printing Valve Assemblies
Company Background
Hunt Valve has a long history of providing advanced valve solutions for the defense and aerospace sectors. Their commitment to innovation and quality has positioned them as a key player in the industry, particularly in the development of systems for military applications.
The 3D Printing Process
- Design and Modeling: Engineers create detailed digital models of valve assemblies using CAD (Computer-Aided Design) software.
- Material Selection: Choosing suitable materials is critical. Hunt Valve utilizes advanced alloys and polymers that can withstand the rigorous conditions experienced by submarines.
- Printing: Using state-of-the-art 3D printers, the valve assemblies are produced layer by layer, ensuring high precision and consistency.
- Post-Processing: After printing, components may undergo additional finishing processes to meet stringent quality standards.
Benefits of 3D Printed Valve Assemblies for the Navy
The introduction of 3D printed valve assemblies offers several strategic advantages for the U.S. Navy:
1. Enhanced Reliability
3D printed components can be engineered for superior performance, ensuring that the valves function reliably even in extreme underwater conditions.
2. Cost-Effectiveness
Reducing lead times and waste not only lowers production costs but also decreases overall lifecycle expenses for submarine maintenance and repairs.
3. Increased Operational Readiness
The ability to quickly produce and replace valve assemblies means submarines can maintain high levels of operational readiness, crucial for national defense.
4. Innovation in Maintenance Practices
3D printing can facilitate new maintenance practices, allowing submarines to produce components on-demand, thus streamlining repair processes and improving efficiency.
Challenges and Considerations
While the benefits are substantial, there are challenges to consider when implementing 3D printing for valve assemblies in submarines:
1. Regulatory Compliance
Any components used in military applications must meet rigorous safety and performance standards. Ensuring compliance with these regulations is critical.
2. Material Limitations
The selection of materials for 3D printing must consider factors such as corrosion resistance, temperature tolerance, and pressure capabilities specific to submarine environments.
3. Integration with Existing Systems
The transition to 3D printed components requires careful planning to ensure compatibility with existing submarine systems and components.
Future of 3D Printing in Naval Applications
The Navy’s adoption of 3D printing technology is poised to transform how it approaches manufacturing and maintenance. As Hunt Valve and other companies continue to innovate, we can expect to see even more applications of 3D printing in naval operations.
Potential Expansions
- Broader Component Range: Beyond valve assemblies, 3D printing could be useful to various submarine components, from structural elements to intricate electronic housings.
- Enhanced R&D: Investment in research and development for new materials and printing technologies could unlock further potential in military applications.
Conclusion
Hunt Valve’s initiative to 3D print valve assemblies for U.S. Navy submarines marks a significant advancement in military manufacturing and maintenance practices. By leveraging the benefits of 3D printing, the Navy can enhance operational readiness, reduce costs, and improve the reliability of critical submarine systems. As this technology continues to evolve, it holds the potential to redefine manufacturing processes across the defense sector.
FAQs
- What is a valve assembly?
- A valve assembly is a critical component in mechanical systems that controls the flow of fluids and gases, essential for maintaining operational efficiency.
- How does 3D printing benefit valve assembly production?
- 3D printing allows for customization, reduced lead times, complex geometries, and material efficiency, making it ideal for valve assembly production.
- What are the applications of 3D printed valve assemblies in submarines?
- They can be useful for flow control, safety mechanisms, and pressure management in various submarine systems.
- What challenges are associated with 3D printing for military applications?
- Challenges include ensuring regulatory compliance, selecting appropriate materials, and integrating new components with existing systems.
- How can 3D printing improve naval operational readiness?
- By enabling rapid production of replacement parts, 3D printing minimizes downtime and ensures submarines remain mission-ready.