Introduction
In the ever-evolving world of industrial automation, safety and reliability are paramount. Emerson’s latest innovation, the motorized actuator paired with an advanced shutoff valve, addresses these critical needs. This article will delve into how these technologies enhance operational safety and reliability in various applications.
Understanding Shutoff Valves
Shutoff valves are essential components in fluid control systems. They regulate the flow of liquids and gases, preventing leaks and maintaining system integrity. The ability to quickly shut off flow in emergencies is crucial for safety in industries like oil and gas, water treatment, and manufacturing.
Types of Shutoff Valves
Shutoff valves come in several types, including:
- Gate Valves: Used for on/off control without throttling.
- Ball Valves: Offer quick shutoff with a simple quarter-turn operation.
- Butterfly Valves: Ideal for large flow volumes with a compact design.
- Globe Valves: Used for throttling and flow regulation.
Among these, the ball valve is particularly popular due to its excellent sealing properties and ease of operation.
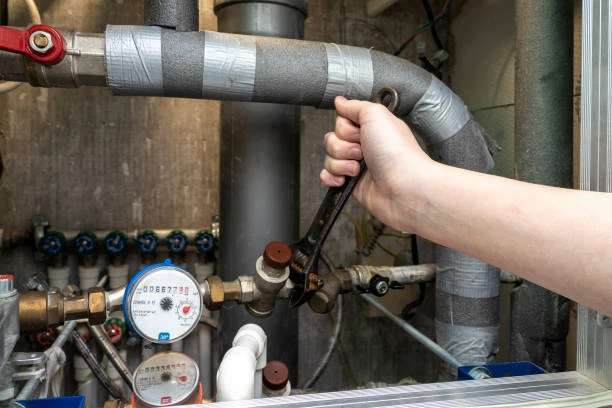
The Role of Motorized Actuators
Motorized actuators provide precise control over shutoff valves. By converting electrical energy into mechanical motion, these devices enable accurate positioning of the valve. This precision is vital for ensuring that the shutoff valves function correctly and promptly in response to system demands.
Benefits of Emerson’s Motorized Actuator and Shutoff Valve
The combination of Emerson’s motorized actuator and shutoff valve offers numerous benefits:
1. Improved Safety
Safety is the foremost concern in any industrial operation. By providing reliable shutoff capabilities, Emerson’s valve minimizes the risk of leaks and spills. The automated actuation ensures that the valve operates correctly and promptly, reducing the likelihood of human error.
2. Increased Reliability
With advanced materials and engineering, Emerson’s shutoff valve delivers exceptional reliability. Industries that rely on continuous operation can benefit from reduced downtime and maintenance costs associated with valve failures.
3. Enhanced Efficiency
Automating the valve operation improves overall system efficiency. Processes that require immediate adjustments to flow can be managed with precision, leading to optimized production and resource utilization.
4. Lower Operational Costs
While the initial investment in Emerson’s motorized actuator and shutoff valve may be higher than traditional systems, the long-term savings associated with reduced maintenance, fewer replacements, and enhanced efficiency make it a cost-effective solution.
Key Features of Emerson’s Shutoff Valve
Emerson’s shutoff valve is designed with several key features that enhance its performance:
- Durability: Made from high-quality materials, these valves withstand harsh environmental conditions.
- Quick Response: The motorized actuator allows for rapid opening and closing, improving response times during emergencies.
- Automation Compatibility: These valves integrate seamlessly with existing automation systems, making them easy to implement in various setups.
Safety Enhancements
Safety is a top priority in any industrial setting. Emerson’s motorized actuator and shutoff valve enhance safety through:
- Fail-Safe Design: In the event of a power failure, the actuator defaults to a closed position, preventing accidental leaks.
- Real-Time Monitoring: Integrated sensors provide real-time data on valve status, allowing operators to respond swiftly to any irregularities.
- Remote Control Capability: Operators can monitor and control valves from a distance, reducing the need for personnel in hazardous areas.
Reliability in Operations
Reliability is equally important. Emerson’s solution ensures consistent performance through:
- Reduced Wear and Tear: The actuator’s design minimizes mechanical stress, extending the valve’s lifespan.
- Consistent Flow Control: The precise positioning of the shutoff valve guarantees stable flow rates, which is essential for maintaining product quality.
- Minimal Downtime: Quick maintenance procedures and robust construction reduce the likelihood of failures, ensuring uninterrupted operations.
Applications in Various Industries
Emerson’s motorized actuator and shutoff valve find applications across several industries:
- Oil and Gas: Managing the flow of hydrocarbons safely is critical, and these valves play a vital role in preventing leaks.
- Water Treatment: Shutoff valves regulate water flow in treatment plants, ensuring clean water supply and compliance with safety regulations.
- Manufacturing: In manufacturing processes, precise control over fluid flows can significantly affect product quality and operational efficiency.
The Future of Fluid Control
As industries continue to innovate, the demand for advanced fluid control solutions will only increase. Emerson’s commitment to developing cutting-edge technology ensures that its motorized actuators and shutoff valves will remain at the forefront of safety and reliability in fluid management.
Conclusion
Emerson’s motorized actuator and shutoff valve represent a significant leap forward in enhancing safety and reliability across various industries. By integrating advanced technologies with user-friendly features, these products not only protect assets but also ensure compliance with stringent safety standards.
FAQs
- What is a shutoff valve? A shutoff valve controls the flow of liquids or gases in a system, allowing for immediate stoppage in emergencies.
- How does a motorized actuator work? A motorized actuator converts electrical energy into mechanical motion, enabling precise control of valve positioning.
- Why is safety important in fluid control systems? Safety is crucial to prevent leaks and accidents that can lead to environmental hazards and financial losses.
- What industries benefit from Emerson’s shutoff valve? Industries such as oil and gas, water treatment, and manufacturing benefit significantly from these valves.
- How do Emerson’s products enhance reliability? Their design minimizes wear and tear, ensures consistent flow control, and reduces maintenance needs, resulting in less downtime.