The demand for High-Density Polyethylene HDPE pipes continues to soar due to their durability, flexibility, and cost-effectiveness. As the industry evolves, more manufacturers are considering establishing HDPE pipe manufacturing plants. This report delves into the setup and costs associated with launching such a facility in 2024, with a focus on the importance of pipe press fittings.
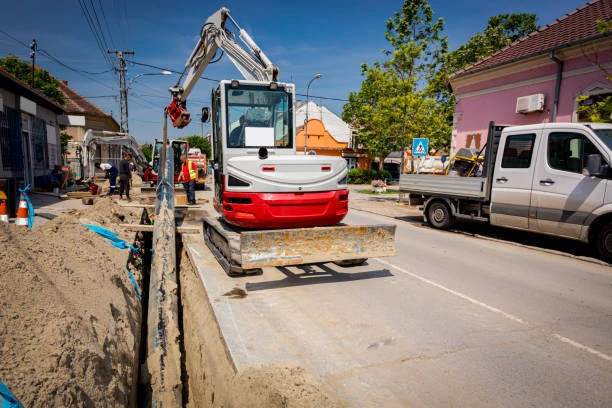
Understanding HDPE Pipes
HDPE pipes are widely used in various sectors, including construction, water supply, and drainage systems. Their ability to withstand harsh environmental conditions makes them a preferred choice for many applications.
Benefits of HDPE Pipes
- Durability: HDPE pipes can last for over 50 years, reducing the need for frequent replacements.
- Corrosion Resistance: Unlike traditional piping materials, HDPE is resistant to corrosion, ensuring the integrity of transported fluids.
- Flexibility: This flexibility allows for easy installation, even in complex layouts.
- Cost Efficiency: While initial costs may be higher, the long-term savings in maintenance and durability make HDPE pipes an economical choice.
- Environmental Sustainability: HDPE is 100% recyclable, aligning with growing global environmental initiatives.
The Role of Pipe Press Fittings
Pipe press fittings are essential components in any HDPE piping system. They provide reliable connections between pipes, ensuring that the entire system operates efficiently and leak-free.
Types of Pipe Press Fittings
- Elbows: These fittings change the direction of the pipe, facilitating fluid movement through various angles.
- Tees: Tees allow branching in the pipeline, enabling multiple flow paths from a single source.
- Reducers: These fittings connect pipes of differing diameters, maintaining optimal flow rates.
- Couplings: Couplings join two pipe sections together securely.
- Caps: Used to seal the ends of pipes, caps prevent leakage and contamination.
Advantages of Using Pipe Press Fittings
- Ease of Installation: Press fittings can be installed quickly without welding, reducing labor costs and installation time.
- Reliability: High-quality fittings provide a tight seal, minimizing the risk of leaks.
- Versatility: Compatible with various pipe materials, these fittings offer flexibility in design and installation.
- Maintenance-Free: The combination of HDPE pipes and press fittings leads to lower maintenance requirements.
Setting Up an HDPE Pipe Manufacturing Plant
1. Location Selection
Choosing the right location is crucial for a successful manufacturing plant. Factors to consider include proximity to raw material suppliers, transportation access, and the availability of skilled labor. Areas with established industrial zones are often ideal.
2. Equipment and Machinery
The equipment required for an HDPE pipe manufacturing plant includes:
- Extruders: For shaping the HDPE material into pipe form.
- Molding Machines: For creating fittings and other components.
- Quality Control Equipment: To ensure that all products meet industry standards.
3. Facility Layout
A well-planned facility layout enhances operational efficiency. Key areas include:
- Production Area: Where the manufacturing process takes place.
- Storage: For raw materials and finished products.
- Quality Control: A dedicated area for testing and inspection.
4. Staffing Requirements
Hiring skilled personnel is essential for smooth operations. Key roles include:
- Production Operators: Responsible for machine operation and maintenance.
- Quality Control Inspectors: Ensure product quality.
- Administrative Staff: Handle logistics, finance, and management.
5. Regulatory Compliance
Understanding and complying with local regulations and industry standards is vital. This includes environmental regulations, safety standards, and quality certifications.
Cost Analysis
Setting up an HDPE pipe manufacturing plant involves several cost components:
1. Initial Investment
The initial investment can vary significantly based on location, scale, and equipment choices. Estimated costs include:
- Land and Facility: Purchasing or leasing land and constructing the facility can range from $500,000 to $2 million.
- Machinery: Equipment costs may range from $300,000 to $1.5 million, depending on production capacity.
- Raw Materials: Initial inventory of HDPE resin can cost around $100,000 to $300,000.
2. Operational Costs
Monthly operational costs include:
- Labor: Salaries for staff can range from $20,000 to $50,000, depending on the workforce size.
- Utilities: Electricity, water, and other utilities may cost approximately $5,000 to $15,000.
- Maintenance: Regular maintenance of machinery may account for 5-10% of total operational costs.
3. Marketing and Distribution
Allocating a budget for marketing and distribution is essential to penetrate the market effectively. This could range from $10,000 to $50,000 annually, depending on the marketing strategy.
4. Profitability Projections
With a growing demand for HDPE pipes, businesses can anticipate strong returns on investment. By producing high-quality pipes and fittings, manufacturers can capitalize on both local and regional markets, projecting profitability within 2-3 years.
Conclusion
Establishing an HDPE pipe manufacturing plant in 2024 presents a lucrative opportunity for investors and entrepreneurs. By focusing on high-quality production, including reliable pipe press fittings, businesses can meet the increasing demand while ensuring sustainability and efficiency. With careful planning and strategic investments, this venture can lead to significant economic benefits and growth in the manufacturing sector.
FAQs
- What are HDPE pipes primarily used for? HDPE pipes are used in water supply, sewage systems, gas distribution, and various industrial applications.
- What are pipe press fittings? Pipe press fittings are connectors that join different pipe sections, ensuring a secure and leak-proof connection.
- How long can HDPE pipes last? HDPE pipes typically have a lifespan exceeding 50 years with proper installation and maintenance.
- Are HDPE pipes environmentally friendly? Yes, HDPE pipes are 100% recyclable and contribute to reduced environmental impact compared to traditional materials.
- What factors influence the cost of setting up a manufacturing plant? Key factors include location, equipment choices, facility size, and operational expenses.