Introduction
Electrofusion welding is a sophisticated technique used for joining polyethylene (PE) and polypropylene random copolymer PPR pipes ISO 15874. This method ensures a strong, leak-proof connection, which is essential for maintaining the integrity and performance of piping systems in various applications, including water supply, industrial processes, and gas distribution. Electrofusion welding machines are designed to make this process efficient and reliable, offering high-quality joints with minimal manual intervention.
What is PPR pipes Electrofusion Welding?
Electrofusion welding involves the use of an electric current to heat and melt the surfaces of PPR pipes and fittings to create a homogeneous joint. The process involves the following key components:
- Electrofusion Fittings: These fittings have embedded heating coils that, when energized, produce heat to melt the PE or PPR material at the joint interface.
- Electrofusion Welding Machine: This machine controls the fusion process by regulating the electrical current supplied to the heating coils. It ensures that the correct amount of heat is applied for a proper weld.
Components of Electrofusion Welding Machines
- Control Unit:
- The control unit manages the welding parameters such as temperature, voltage, and time. Advanced models may include programmable settings and data logging features to track welding conditions and ensure consistent quality.
- Electrofusion Clamps:
- These clamps hold the pipe and fitting in place during the welding process. They are crucial for maintaining alignment and preventing movement that could affect the weld quality.
- Heating Elements:
- These are the coils embedded in the fittings that generate the necessary heat to melt the pipe and fitting surfaces for fusion.
- Power Supply:
- Provides the electrical current needed for the heating elements. It must be stable and reliable to ensure proper welding conditions.
- Temperature Sensors:
- Monitor the temperature of the welding process to ensure that it remains within the specified range for optimal fusion.
Advantages of Electrofusion PPR pipes Welding
- Strong and Reliable Joints:
- Electrofusion welding creates a seamless, homogeneous joint that is as strong as the pipe material itself, ensuring durability and leak-proof performance.
- Versatility:
- Suitable for a wide range of PPR pipes sizes and materials, including PE and PPR. This makes it a versatile choice for various piping applications.
- Minimal Preparation:
- The process requires minimal pipe preparation compared to other joining methods, such as butt welding. This reduces installation time and labor costs.
- Consistency:
- Automated control of welding parameters ensures consistent joint quality, reducing the risk of human error and improving overall system reliability.
- Reduced Environmental Impact:
- Electrofusion welding produces minimal waste and does not require additional materials such as adhesives or welding rods, contributing to a cleaner and more sustainable process.
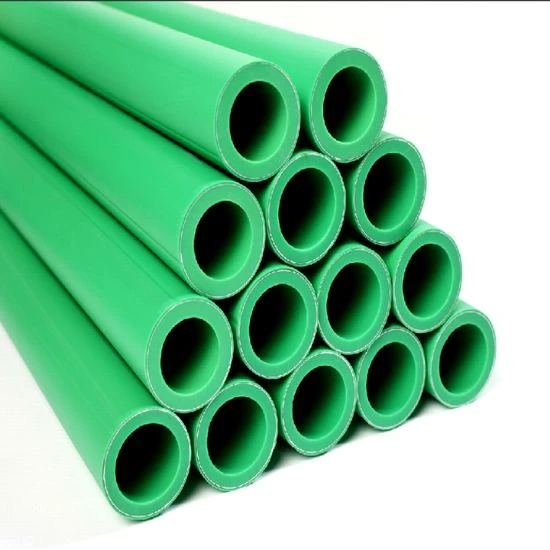
Applications
- Water Supply Systems:
- Used for joining PE and PPR pipes in municipal water supply networks, ensuring reliable and leak-free connections.
- Gas Distribution:
- Electrofusion welding is commonly used for joining PE pipes in natural gas distribution systems, where safety and integrity are critical.
- Industrial Piping:
- Suitable for various industrial applications, including chemical and pharmaceutical processes, where precise and durable joints are essential.
- HVAC Systems:
- Employed in heating, ventilation, and air conditioning systems to create strong and efficient connections between pipes.
Choosing an Electrofusion PPR pipes Welding Machine
- Machine Capacity:
- Ensure the machine can handle the pipe sizes and types you will be working with. Machines come in different capacities to suit various pipe dimensions.
- Control Features:
- Look for machines with advanced control features, such as programmable settings and data logging, to enhance accuracy and quality.
- Ease of Use:
- Consider machines that are user-friendly with intuitive interfaces and clear instructions, reducing the learning curve for operators.
- Durability and Maintenance:
- Select machines built with high-quality materials and components for durability and ease of maintenance.
- Support and Service:
- Choose a machine from a reputable manufacturer that offers good customer support and service, including training, repairs, and spare parts.
Conclusion
Electrofusion welding machines are essential tools for creating reliable and durable joints in PE and PPR piping systems. With their ability to produce strong, leak-proof connections efficiently, these machines play a crucial role in various applications, from water supply and gas distribution to industrial processes. When selecting an electrofusion welding machine, consider factors such as capacity, control features, and support to ensure optimal performance and quality.