Introduction
PPR (Polypropylene Random Copolymer) and HDPE (High-Density Polyethylene) pipes EN 15874 are both popular choices in various piping applications due to their distinct properties. While they share some similarities, they have different characteristics that make them suitable for different uses. Here’s a comparison of PPR and HDPE pipes based on various factors.
1. Material Composition
a. PPR Pipes
- Material: Made from Polypropylene Random Copolymer, which is a type of polypropylene with a specific molecular structure.
- Properties: PPR pipes are known for their resistance to high temperatures and chemical reactions, making them suitable for hot water and industrial applications.
b. HDPE Pipes
- Material: Made from High-Density Polyethylene, a type of polyethylene with high density and crystalline structure.
- Properties: HDPE pipes are known for their flexibility, impact resistance, and low-temperature performance, making them suitable for a wide range of applications including water supply and drainage.
2. Temperature and Pressure Resistance
a. PPR Pipes
- Temperature: PPR pipes can handle temperatures up to 95°C (203°F), making them suitable for hot water distribution and heating systems.
- Pressure: They are designed to withstand high pressures and are often used in applications requiring high pressure and temperature control.
b. HDPE Pipes
- Temperature: HDPE pipes are generally used in applications with temperatures up to 60°C (140°F). They are not suitable for high-temperature applications and may deform or soften if exposed to temperatures above this range.
- Pressure: HDPE pipes have varying pressure ratings depending on their SDR (Standard Dimension Ratio), and they are used in a range of pressure applications including water supply and gas distribution.
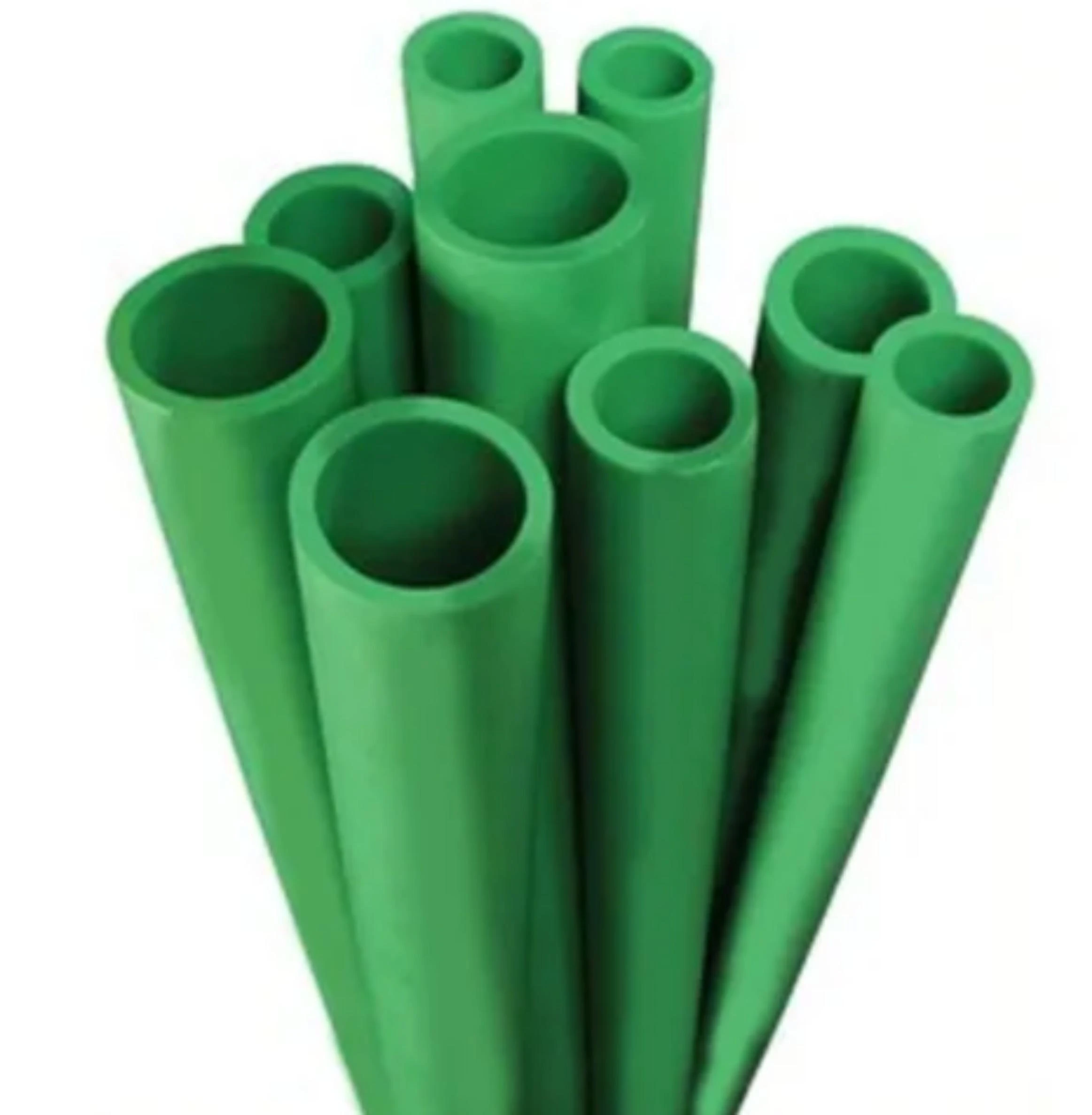
3. Flexibility and Durability
a. PPR Pipes
- Flexibility: PPR pipes are relatively rigid and are not as flexible as HDPE pipes. They are more suitable for applications where rigidity and structural integrity are important.
- Durability: They offer high durability and resistance to corrosion, scaling, and chemical reactions. PPR pipes are long-lasting with minimal maintenance.
b. HDPE Pipes
- This flexibility makes them suitable for applications with complex routing.
- Durability: They are highly durable and resistant to impact, corrosion, and environmental stress cracking.
4. Installation Methods
a. PPR Pipes
- Joining Method: PPR pipes are joined using fusion methods such as socket fusion and electrofusion. These methods create strong, leak-proof joints but require specific equipment and trained personnel.
- Installation: Installation involves heating the pipe and fitting ends and then joining them, which can be time-consuming but results in durable connections.
b. HDPE Pipes
- These methods provide flexibility in installation.
- Installation: Installation is relatively straightforward, with the flexibility of the pipes allowing for easy routing and fewer fittings.
5. Chemical and Environmental Resistance
a. PPR Pipes
- Chemical Resistance: PPR pipes have excellent resistance to a wide range of chemicals, including acids, bases, and salts. They are suitable for industrial applications involving aggressive chemicals.
b. HDPE Pipes
- Chemical Resistance: HDPE pipes are also resistant to many chemicals, including acids and bases.
6. Cost and Longevity
a. PPR Pipes
- Cost: Generally more expensive than HDPE pipes, especially due to the specialized fusion equipment required for installation.
- Longevity: PPR pipes have a long service life with minimal maintenance needs, making them a cost-effective choice in the long run despite the higher initial cost.
b. HDPE Pipes
- Cost: Often less expensive than PPR pipes, with lower installation costs due to easier joining methods and greater flexibility.
7. Applications
a. PPR Pipes
- Common Uses: Hot and cold water supply, heating systems, chemical processing, and industrial applications.
b. HDPE Pipes
- Common Uses: Water supply, gas distribution, drainage systems, irrigation, and environmental protection projects.
Conclusion
Both PPR and HDPE pipes offer valuable properties for specific applications. PPR pipes excel in high-temperature and high-pressure environments with excellent chemical resistance, making them suitable for plumbing and industrial applications. HDPE pipes, on the other hand, are flexible, impact-resistant, and cost-effective, making them ideal for water and gas distribution, drainage, and outdoor applications. The choice between PPR and HDPE pipes depends on the specific requirements of the project, including temperature, pressure, flexibility, and environmental conditions.