In the food and pharmaceutical industries, ensuring product safety and quality is paramount. One of the critical processes in these sectors is spray drying, where liquids are transformed into powders while retaining their essential properties. GEA, a global leader in process technology, has recently introduced innovative valve technology designed to significantly reduce microbial risks during this process. This article will explore how GEA’s new valve technology enhances spray drying, its benefits, and its impact on the industry.
Understanding Spray Drying
Spray drying is a widely used method for converting liquid feed into dry powder. This process involves atomizing the liquid into fine droplets and then passing these droplets through a hot gas stream, resulting in rapid evaporation of moisture. The final product is a fine powder, often used in various applications, from food ingredients to pharmaceutical formulations.
Importance of Microbial Control in Spray Drying
Microbial contamination can have serious implications in spray drying. The presence of bacteria, yeasts, and molds can compromise product safety, lead to spoilage, and reduce shelf life. Consequently, maintaining strict hygiene and sanitation standards during the spray drying process is critical. This is where GEA’s new valve technology plays a vital role.
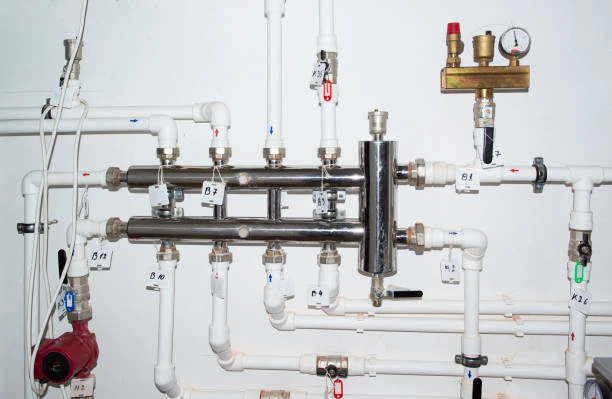
GEA’s New Valve Technology
GEA’s latest innovation focuses on improving the design and functionality of valves used in spray drying systems. These valves are essential components that control the flow of materials and air, impacting both efficiency and hygiene. The new valve technology incorporates several key features aimed at reducing microbial risks.
Key Features of the New Valve Technology
- Enhanced Sealing Mechanisms: The new valves are design with advanced sealing technologies that minimize leakage and prevent microbial ingress. This is crucial in maintaining a sterile environment throughout the spray drying process.
- Easy Cleanability: The design of the valves allows for easy disassembly and thorough cleaning. This feature is vital for preventing contamination between production batches and ensuring compliance with hygiene standards.
- Material Selection: GEA has utilized materials that are resistant to corrosion and microbial growth. These materials not only enhance the durability of the valves but also contribute to maintaining product integrity.
- Automated Control: The new valve technology can be integrate with automation systems, enabling precise control over the flow and pressure. This level of control helps to optimize the drying process and reduce the risk of product degradation.
- Real-Time Monitoring: The valves are important with sensors that monitor performance in real-time, allowing for immediate adjustments to be made if any anomalies are detected. This feature further enhances the safety and efficiency of the spray drying process.
Benefits of GEA’s New Valve Technology
Improved Product Safety
By significantly reducing microbial risks, GEA’s new valve technology enhances product safety. Manufacturers can confidently produce high-quality powders that meet stringent safety standards, thus protecting consumers and reducing the risk of recalls.
Increased Efficiency
The advanced design of the new valves leads to improved flow control and reduced energy consumption during the spray drying process. This increased efficiency not only lowers operational costs but also minimizes environmental impact.
Enhanced Product Quality
With better control over the drying process, manufacturers can achieve consistent product quality. This consistency is crucial for applications where the properties of the powder—such as solubility, flavor, and nutritional content—are essential.
Compliance with Regulatory Standards
The food and pharmaceutical industries are subject to rigorous regulatory standards. GEA’s new valve technology helps manufacturers meet these requirements by ensuring that the spray drying process is safe and hygienic.
Flexibility in Applications
The versatility of GEA’s new valve technology allows it to be useful across various applications, from dairy and food products to pharmaceuticals and chemicals. This adaptability makes it a valuable addition to any manufacturing setup.
Implementation of GEA’s New Valve Technology
Installation Process
Implementing GEA’s new valve technology into existing spray drying systems is straightforward. The valves can be easily integrate without significant modifications to the current setup. Here’s a brief overview of the installation process:
- Assessment: Evaluate the existing spray drying system to determine the best integration point for the new valves.
- Installation: Follow GEA’s installation guidelines to ensure proper placement and function. This step typically requires minimal downtime.
- Calibration: Once installed, the valves need to be calibrate to match the specific requirements of the spray drying process.
- Training: Operators should receive training on the new system to maximize its benefits and ensure smooth operation.
Maintenance and Support
GEA provides comprehensive support and maintenance services to ensure that the new valve technology operates at peak efficiency. Regular maintenance checks can prevent potential issues and prolong the life of the valves.
Conclusion
GEA’s new valve technology represents a significant advancement in the field of spray drying. By effectively reducing microbial risks, this innovative solution enhances product safety, efficiency, and quality. As industries continue to prioritize hygiene and safety, GEA’s technology positions itself as a vital component in the evolution of spray drying processes. Manufacturers can embrace this technology with confidence, knowing it will help them meet the growing demands for safe and high-quality products.
FAQs About GEA’s New Valve Technology
- How does the new valve technology reduce microbial risks?
- The enhanced sealing mechanisms and easy cleanability of the valves minimize the risk of microbial ingress and contamination.
- Can the new valves be integrated into existing spray drying systems?
- Yes, the valves can be easily install in current systems without significant modifications.
- What materials are used in the new valve technology?
- GEA utilizes corrosion-resistant materials that inhibit microbial growth, ensuring durability and hygiene.
- Is training required for operators using the new valve technology?
- Yes, GEA recommends training for operators to ensure they understand the features and maintenance of the new system.
- What industries can benefit from GEA’s new valve technology?
- The technology is versatile and can be useful in food, dairy, pharmaceutical, and chemical industries, among others.