In the heart of Texas, where the summer sun blazes and temperatures soar, maintaining safety and operational integrity at nuclear power plants is paramount. One crucial component in this endeavor is high-density polyethylene HDPE pipe, which plays a significant role in fire prevention and cooling systems. This article explores the importance of HDPE pipes in fire prevention strategies at nuclear facilities, their advantages, and their impact on safety and efficiency.
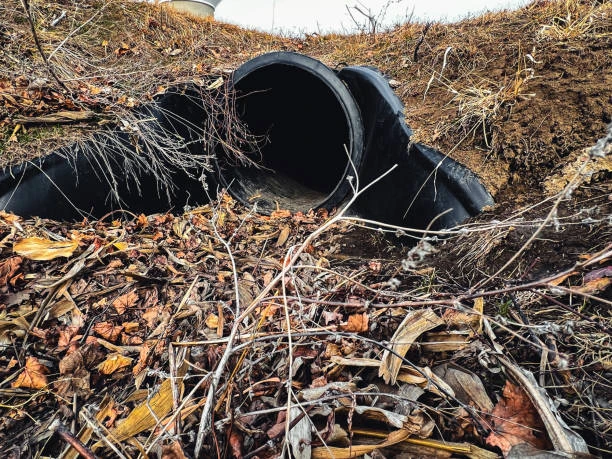
Understanding the Role of HDPE Pipe
High-density polyethylene (HDPE) pipes are a type of plastic piping made from high-density polyethylene. Known for their durability, flexibility, and resistance to various environmental factors, HDPE pipes are widely used in various applications, including water supply, sewage, and industrial processes.
Advantages of HDPE Pipe
- Durability: HDPE pipes are resistant to corrosion, chemicals, and environmental stress, making them suitable for long-term applications in harsh conditions.
- Flexibility: The flexibility of HDPE allows it to adapt to shifting ground conditions, reducing the risk of fractures or leaks.
- Low Maintenance: Unlike traditional metal pipes, HDPE pipes require minimal maintenance, leading to reduced operational costs.
- Lightweight: HDPE pipes are significantly lighter than metal alternatives, simplifying transportation and installation.
- Thermal Insulation: HDPE pipes have inherent insulating properties, which can be crucial in maintaining temperature control for fire prevention systems.
Fire Prevention at HDPE pipe Nuclear Power Plants
Nuclear power plants require comprehensive fire prevention systems to ensure safety and operational integrity. These facilities must manage a variety of potential fire hazards, from equipment malfunctions to external threats. Effective cooling systems are vital in mitigating these risks, and HDPE pipes are central to these efforts.
Cooling Systems and HDPE pipe Their Importance
Cooling systems at nuclear power plants are designed to remove excess heat from reactors and associated equipment. In the event of a fire, these systems are crucial for maintaining temperature control and preventing catastrophic failures. HDPE pipes facilitate the movement of cooling water, helping to dissipate heat quickly and efficiently.
How HDPE Pipe Contribute to Fire Prevention
- Efficient Heat Transfer: HDPE pipes are excellent for transporting water, enabling efficient heat transfer from critical systems to cooling towers or other heat exchange mechanisms.
- Reduced Risk of Corrosion: Unlike metal pipes, HDPE pipes do not corrode, ensuring a reliable flow of cooling water. This reliability is essential in preventing heat buildup that could lead to fires.
- Leak Resistance: The seamless construction of HDPE pipes minimizes the risk of leaks, which can be detrimental to cooling systems. Maintaining a consistent flow of water is vital for fire prevention.
- Temperature Resistance: HDPE pipes can withstand a range of temperatures, making them suitable for environments where temperature fluctuations are common. Their thermal insulation properties help maintain cooler temperatures in critical systems.
Case Study: HDPE Pipe in Texas Nuclear Facilities
In Texas, several nuclear power plants have adopted HDPE pipes in their cooling systems and fire prevention measures. These facilities have witnessed significant improvements in operational efficiency and safety.
Example: HDPE pipe The South Texas Project
The South Texas Project (STP) is a notable example where HDPE pipes play a critical role in fire prevention and cooling. This facility uses HDPE pipes in its cooling water system to ensure effective heat dissipation. The advantages of HDPE in this setting include:
- Improved Reliability: By utilizing HDPE pipes, the STP has enhanced the reliability of its cooling systems, reducing the risk of overheating and potential fires.
- Cost-Effectiveness: The long lifespan and low maintenance requirements of HDPE pipes contribute to reduced operational costs, allowing the facility to allocate resources more effectively.
- Environmental Benefits: The use of HDPE pipes aligns with sustainability goals, as they are recyclable and contribute to lower environmental impact compared to traditional materials.
The Future of in Nuclear Safety
As nuclear power plants continue to evolve, the role of HDPE pipes in fire prevention and cooling systems is expected to expand. Several trends and advancements are shaping the future of HDPE pipes in this critical sector.
1. Technological Innovations
Advancements in manufacturing technologies are leading to even higher quality HDPE pipes. Enhanced performance characteristics will improve their suitability for demanding applications in nuclear facilities.
2. Increased Focus on HDPE pipe Sustainability
With growing concerns about environmental impacts, the nuclear industry is prioritizing sustainable materials. The recyclability of HDPE pipes makes them an attractive option for future projects.
3. HDPE pipe Regulatory Support
As safety regulations continue to evolve, nuclear power plants will increasingly seek reliable materials that meet stringent standards. HDPE pipes are well-positioned to fulfill these requirements.
4. Integration of HDPE pipe Smart Technologies
The integration of smart technologies, such as sensors and monitoring systems, will enhance the performance of HDPE pipe systems. Real-time monitoring can help detect potential issues before they escalate, further enhancing safety.
Conclusion
The proposal to utilize HDPE pipes in fire prevention and cooling systems at nuclear power plants in Texas underscores the importance of innovative materials in ensuring safety and efficiency. With their numerous advantages, including durability, flexibility, and low maintenance, HDPE pipes are becoming essential components in modern nuclear facilities.
As the industry moves toward a more sustainable and technologically advanced future, HDPE pipes will play a crucial role in enhancing safety measures, improving operational efficiency, and contributing to the overall integrity of nuclear power plants. The focus on effective fire prevention strategies is vital in safeguarding both the facilities and the surrounding communities.
FAQs
- What are HDPE pipe used for in nuclear power plants? HDPE pipes are primarily used for cooling systems and fire prevention measures, facilitating the movement of cooling water and maintaining temperature control.
- How long do HDPE pipe last? HDPE pipes can last over 50 years with proper installation and maintenance, making them a durable choice for critical applications.
- Are HDPE pipe resistant to fire? While HDPE pipes are not fireproof, their ability to resist heat and maintain structural integrity under high temperatures makes them suitable for fire prevention systems.
- What are the advantages of using HDPE pipe over metal pipes? HDPE pipes are lighter, corrosion-resistant, require less maintenance, and provide better thermal insulation compared to traditional metal pipes.
- How do HDPE pipe contribute to environmental sustainability? HDPE pipes are recyclable and have a lower environmental impact than many traditional materials, supporting sustainability initiatives in construction and infrastructure projects.