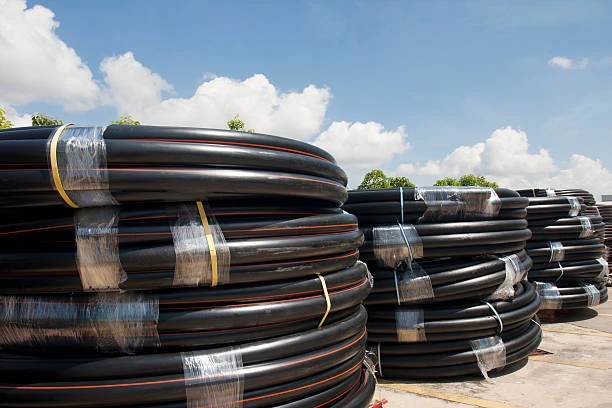
Introduction
In the world of PE pipe installation and maintenance, proper preparation of pipe surfaces is essential for ensuring secure connections and system reliability. PE pipe peelers are specialized tools used to remove the outer layer of PE pipes to prepare them for jointing and fusion processes. This article explores the various types of PE pipe peeler blades and common parts, highlighting their importance, functions, and maintenance.
What is a PE Pipe Peeler?
Definition and Purpose
A PE pipe peeler is a tool designed to remove the outer layer of polyethylene pipes. This process is crucial for:
- Preparing the Pipe Surface: Ensuring a clean surface for effective welding or jointing.
- Enhancing Bonding: Improving the quality of the bond between the pipe and fittings.
Types of PE Pipe Peelers
1. Manual Pipe Peelers
- Design: Hand-operated tools with adjustable blades.
- Use: Ideal for small-scale or field operations where portability and ease of use are essential.
2. Powered Pipe Peelers
- Design: Motorized tools with automatic or semi-automatic blade operation.
- Use: Suitable for high-volume operations or where consistent, precise peeling is required.
PE Pipe Peeler Blades
1. Types of Blades
Circular Blades
- Description: Round blades used in some manual and powered peelers.
- Function: Ideal for making clean, even cuts around the pipe circumference.
Straight Blades
- Description: Straight-edged blades found in various peeler models.
- Function: Useful for removing the outer layer in a linear motion, often used in manual peelers.
Cartridge Blades
- Description: Replaceable blade cartridges used in some advanced peelers.
- Function: Allow for quick blade changes and maintenance.
2. Blade Material and Construction
- Material: Typically made from high-quality stainless steel or carbide for durability and sharpness.
- Construction: Designed to withstand the wear and tear of peeling PE pipes and maintain consistent performance.
Common Parts of PE Pipe Peelers
1. Blade Assembly
- Components: Includes the blade holder, adjustment mechanism, and the blade itself.
- Function: Allows for precise control over the peeling process and blade replacement.
2. Pipe Holder
- Components: Clamp or grip mechanism to hold the pipe securely in place.
- Function: Ensures stability and alignment during peeling, preventing movement that could affect the quality of the surface preparation.
3. Adjustment Mechanism
- Components: Knobs or levers for adjusting blade depth and alignment.
- Function: Provides control over the thickness of the material being peeled and ensures uniformity.
4. Handle and Housing
- Components: Ergonomic handle and protective housing.
- Function: Enhances user comfort and safety while operating the peeler. The housing also protects internal components from damage.
5. Motor and Drive Mechanism (for powered peelers)
- Components: Electric motor and drive gears.
- Function: Powers the blade for automatic peeling, offering efficiency and consistency in high-volume applications.
Maintenance and Care
1. Regular Cleaning
- Procedure: Clean the peeler and blades regularly to remove debris and residues.
- Importance: Prevents clogging and ensures optimal performance.
2. Blade Sharpening and Replacement
- Procedure: Sharpen or replace blades as needed to maintain cutting efficiency.
- Importance: Ensures clean, precise peeling and prolongs the life of the tool.
3. Lubrication
- Procedure: Lubricate moving parts and adjustment mechanisms.
- Importance: Reduces friction and wear, ensuring smooth operation.
4. Inspection
- Procedure: Regularly inspect the tool for any signs of damage or wear.
- Importance: Identifies potential issues before they affect performance or safety.
Choosing the Right PE Pipe Peeler
1. Consider the Application
- Type of Operation: Determine whether a manual or powered peeler is more suitable based on the volume and complexity of the work.
- Pipe Size: Ensure the peeler is compatible with the diameter of the PE pipes being used.
2. Evaluate Blade Quality
- Material: Choose blades made from high-quality materials for durability.
- Design: Select a blade design that suits your specific peeling needs.
3. Check for Ease of Maintenance
- Blade Replacement: Look for tools with easy blade replacement options.
- Cleaning: Choose a peeler that is easy to clean and maintain.
Conclusion
PE pipe peelers are essential tools for ensuring proper surface preparation in polyethylene pipe systems. Understanding the different types of blades and common parts, as well as adhering to best practices for maintenance, will help ensure the longevity and performance of these tools. Whether you are working with manual or powered peelers, selecting the right tool and keeping it in good condition are key to achieving reliable and efficient results in your piping projects.
FAQs
1. What is the purpose of using a PE pipe peeler?
A PE pipe peeler removes the outer layer of polyethylene pipes to prepare them for welding or jointing, ensuring a clean and effective bond.
2. How do I know which blade type is suitable for my PE pipe peeler?
Choose a blade type based on the pipe size, the peeling method (manual or powered), and the specific requirements of your application. Circular blades are common for uniform cuts, while straight blades are useful for linear peeling.
3. How often should I replace the blades on my PE pipe peeler?
Blades should be replaced when they become dull or damaged. Regularly inspect the blades for signs of wear and replace them as needed to maintain cutting efficiency.
4. Can I use a PE pipe peeler on other types of pipes?
PE pipe peelers are specifically designed for polyethylene pipes. For other pipe materials, different tools and techniques may be required.
5. What are the signs that my PE pipe peeler needs maintenance?
Signs that maintenance is needed include difficulty in cutting, uneven peeling, visible damage to the tool or blades, and unusual noise during operation. Regular inspections and upkeep will help address these issues promptly.