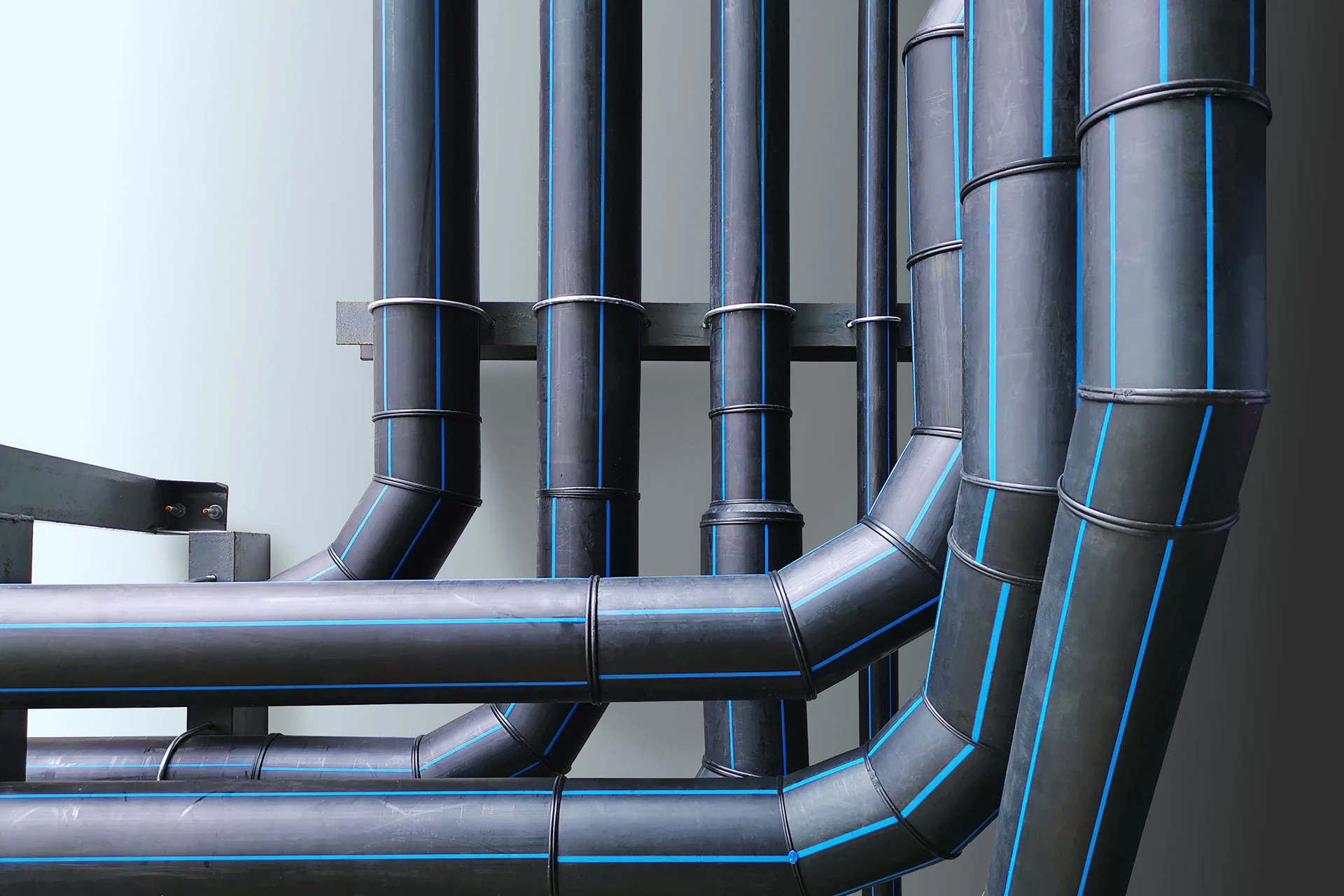
Introduction
PE pipes have become a popular choice in various applications, including water supply, gas distribution, and industrial processes. Their flexibility, durability, and resistance to corrosion make them an ideal solution for modern piping systems. This article provides a comprehensive guide on PE pipe installation, covering essential preparation steps, installation techniques, and best practices to ensure a reliable and efficient piping system.
Understanding PE Pipes
What Are PE Pipes?
Polyethylene pipes are made from high-density polyethylene (HDPE) or medium-density polyethylene (MDPE). They are known for their:
- Flexibility: Ability to bend and adapt to various conditions.
- Durability: Resistance to corrosion, chemicals, and environmental factors.
- Ease of Installation: Lightweight and easy to handle.
Applications of PE Pipes
PE pipes are used in:
- Water Distribution: For transporting potable water.
- Gas Distribution: For natural gas and other gaseous fuels.
- Industrial Processes: In various industrial applications due to their chemical resistance.
Preparation for PE Pipe Installation
1. Site Assessment
Survey and Planning
- Site Survey: Conduct a thorough survey of the installation area to identify any potential obstacles or issues.
- Planning: Develop a detailed installation plan, including pipe routing, depth, and required fittings.
Soil and Environmental Conditions
- Soil Analysis: Assess soil conditions to determine if special bedding or protection is needed.
- Environmental Factors: Consider factors such as temperature and UV exposure that could impact the pipe.
2. Pipe Handling and Storage
Handling
- Careful Handling: Avoid dropping or rough handling of pipes to prevent damage.
- Pipe Orientation: Store pipes horizontally to prevent deformation.
Storage
- Protection: Protect pipes from direct sunlight and extreme temperatures.
- Support: Use appropriate supports to prevent sagging or bending.
3. Trenching and Bedding
Trenching
- Depth and Width: Excavate trenches to the required depth and width based on the pipe diameter and application.
- Trench Support: Provide support to trench walls to prevent collapse.
Installation Techniques
1. Pipe Laying
Alignment and Positioning
- Straight Layout: Lay pipes in a straight alignment to prevent unnecessary stress.
- Proper Positioning: Ensure pipes are positioned correctly within the trench.
Support and Protection
- Pipe Supports: Provide adequate supports to prevent sagging or displacement.
- Protection: Use protective measures to shield the pipe from external forces and potential damage.
2. Jointing Methods
Fusion Joining
- Butt Fusion: Heat the ends of two pipes and press them together to form a strong, seamless joint.
- Electrofusion: Use an electrofusion coupling to join the pipes by applying an electric current to melt and fuse the pipe ends.
Mechanical Joining
- Couplings and Fittings: Use mechanical couplings and fittings to connect pipes without heat. Ensure they are compatible with PE pipes and properly tightened.
Socket Fusion
- Procedure: Heat the inside of a fitting and the outside of the pipe end, then join them together. This method is typically used for smaller diameter pipes.
3. Testing and Inspection
Pressure Testing
- Procedure: Perform pressure tests to verify the integrity of the installed piping system. Follow standard procedures for testing and safety.
Final Inspection
- Check Alignment: Ensure pipes are correctly aligned and properly supported.
- Inspect Joints: Verify the quality of joints and fittings for any signs of defects or damage.
Post-Installation Practices
1. Backfilling
Backfill Material
- Selection: Use appropriate backfill material that does not cause damage to the pipe.
- Compaction: Compact the backfill material in layers to ensure stability and prevent settling.
2. Documentation and Record-Keeping
- Installation Records: Document the installation process, including pipe types, sizes, and locations.
- Maintenance Schedule: Establish a maintenance schedule for regular inspections and upkeep of the piping system.
Conclusion
Proper installation of PE pipes is crucial for ensuring the reliability and efficiency of your piping system.
FAQs
Key factors include site assessment, soil and environmental conditions, and proper handling and storage of the pipes.
2. What are the common methods for joining PE pipes?
Common methods include butt fusion, electrofusion, and mechanical joining. The choice of method depends on the application and pipe size.
3. How do I perform a pressure test on a PE pipe system?
Follow standard procedures for pressure testing, which typically involve filling the system with water, pressurizing it to the required level, and checking for leaks.