Introduce PPR Pipe
PPR (Polypropylene Random Copolymer) pipes are revolutionizing the plumbing industry with their robust characteristics and practical applications. One of the most effective techniques for joining PPR pipes is hot melt welding, which ensures strong, leak-proof connections. This article will explore PPR Pipe, the hot melt welding process, essential skills needed for installation, and the benefits of this innovative plumbing solution. We will also provide answers to frequently asked questions at the end.
Understanding PPR Pipe
PPR pipes are composed of a type of polypropylene that offers enhanced performance, making them ideal for various plumbing applications. They are often used in residential, commercial, and industrial settings for both hot and cold water systems.
Characteristics of PPR Pipe
- Durability: PPR pipes are highly resistant to corrosion, chemicals, and scaling, which extends their lifespan significantly compared to traditional metal pipes.
- Temperature Resistance: These pipes can handle temperatures up to 95°C (203°F), making them suitable for hot water applications.
- Lightweight: Their lightweight nature simplifies transportation and installation, reducing labor costs.
- Flexibility: PPR pipes can be bent and shaped, allowing for versatile installation configurations.
- Low Thermal Conductivity: This property minimizes heat loss in hot water systems, contributing to energy efficiency.
Applications of PPR Pipe
PPR pipes are used in various applications, including:
- Hot and Cold Water Supply: Ideal for residential and commercial plumbing.
- Heating Systems: Commonly used in underfloor heating and radiator systems.
- Industrial Applications: Suitable for chemical and industrial fluid transport.
- Potable Water Systems: Safe for drinking water applications due to their non-toxic properties.
The Hot Melt Welding Process
Hot melt welding is a widely accepted method for joining PPR pipes. This process involves heating the ends of the pipes and fittings until they reach a molten state, allowing them to bond securely upon cooling. Here’s a detailed overview of the hot melt welding process.
Equipment Needed
Before beginning, gather the following tools and equipment:
- PPR Pipes and Fittings: Ensure you have the correct sizes and types for your application.
- Hot Melt Welding Machine: This device heats the pipe ends and fittings.
- Pipe Cutter: For cleanly cutting the pipes.
- Deburring Tool: To smooth out cut edges and prevent leaks.
- Measuring Tape: For accurate measurements.
- Safety Gear: Safety goggles and gloves are essential to protect against burns.
Step-by-Step Guide to Hot Melt Welding
Preparation
- Measure and Cut: Use a measuring tape to determine the required length of the PPR pipe. Cut the pipe using a pipe cutter to ensure a clean, straight edge.
- Deburr the Edges: After cutting, use a deburring tool to remove any rough edges from the cut ends. This step is crucial for achieving a tight seal.
Heating the Pipe and Fitting
- Set Up the Welding Machine: Adjust the hot melt welding machine to the appropriate temperature, typically around 260°C (500°F).
- Heat the Pipe and Fitting: Insert the cut ends of the pipe and fitting into the welding machine. Allow them to heat for approximately 30 to 45 seconds, depending on the pipe diameter.
Joining the Components
- Remove from Heat: Carefully take the heated pipe and fitting out of the machine, ensuring not to touch the hot ends.
- Join the Pipe and Fitting: Quickly insert the heated end of the pipe into the fitting with a twisting motion. This action helps to distribute the molten material evenly and create a secure bond.
- Hold in Place: Maintain pressure for a few seconds to allow the connection to cool and solidify.
Inspection
After the joint has cooled, visually inspect it for any gaps or inconsistencies. A well-executed joint will appear smooth and uniform. If any defects are detected, it may be necessary to redo the joint to prevent leaks.
Key Skills for Hot Melt Welding
Mastering hot melt welding requires practice and attention to detail. Here are some essential skills and tips for successful PPR pipe installation:
- Precision Cutting: Accurate measurements and straight cuts are vital for creating tight joints. Invest time in perfecting your cutting technique.
- Temperature Control: Understanding the appropriate heating times and temperatures for different pipe sizes is critical. Overheating can damage the material, while insufficient heating can lead to weak joints.
- Quick Assembly: After heating, you must work quickly to join the components before the material cools. Practicing the timing will improve your efficiency.
- Visual Inspection: Developing a keen eye for detail will help you identify imperfections in joints, ensuring long-lasting connections.
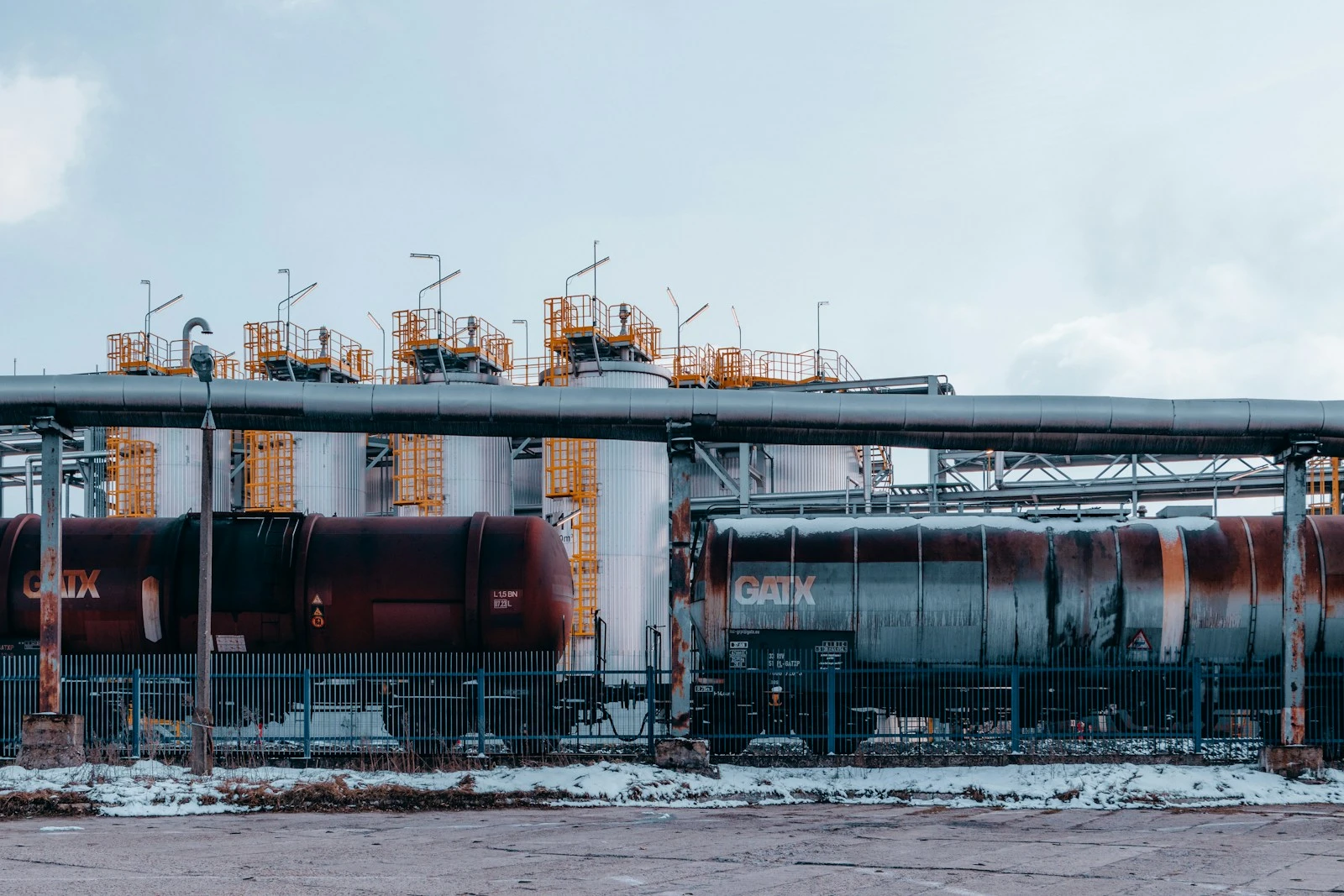
Advantages of PPR Pipe and Hot Melt Welding
Combining PPR pipes with the hot melt welding technique offers several benefits:
- Cost-Effective: The durability and low maintenance needs of PPR pipes reduce long-term costs associated with repairs and replacements.
- Environmentally Friendly: PPR pipes are recyclable, and the hot melt welding process does not produce harmful emissions.
- High Strength: The hot melt welding method creates strong joints that can withstand high pressure and temperature variations.
- Versatility: PPR pipes can be used in various applications, making them suitable for diverse plumbing needs.
- Ease of Installation: With proper training and skills, PPR pipe installation can be quicker and simpler than traditional methods.
Maintenance and Care for PPR Pipe Systems
Maintaining PPR pipe systems is relatively easy, but regular checks can prevent future issues:
- Visual Inspections: Periodically inspect joints and pipes for signs of wear or leaks.
- Cleaning: Clean the exterior of the pipes to prevent buildup of debris or sediment, which can affect water flow.
- Temperature Monitoring: Ensure that the pipes are not exposed to extreme temperature changes that could cause damage.
Conclusion
PPR pipes, combined with the hot melt welding technique, provide a reliable and efficient solution for modern plumbing systems. Understanding the properties of PPR pipes and mastering hot melt welding skills can lead to successful installations that stand the test of time. Whether for residential, commercial, or industrial applications, PPR pipes represent a versatile and durable choice.
Frequently Asked Questions (FAQs)
- What are the main benefits of using PPR pipes?
- PPR pipes are lightweight, corrosion-resistant, and durable, making them ideal for various plumbing applications.
- How do I determine the right size of PPR pipe for my project?
- The size depends on the specific application, flow requirements, and local plumbing codes. Consulting with a plumbing professional can help ensure you choose the correct size.
- Can PPR pipes be used for outdoor applications?
- Yes, PPR pipes can be use outdoors, but they should be protecte from direct sunlight to prevent degradation over time.
- How long does the hot melt welding process take?
- The entire process usually takes about 1 to 2 minutes per joint, depending on the size of the pipe and fittings.
- Is it necessary to have professional training to weld PPR pipes?
- While basic training can help, anyone can learn the technique with practice. However, for large projects or critical installations, hiring a trained professional is advisable.