PPR (Polypropylene Random Copolymer) pipes are gaining popularity in various industries due to their outstanding characteristics and versatility. This article will explore the reasons behind the preference for PPR Pipe in industrial pipe fittings, examining their benefits, applications, and why they have become a preferred choice in modern plumbing and piping systems.
Understanding PPR Pipe
PPR pipes are made from a type of polypropylene that combines flexibility, strength, and chemical resistance, making them suitable for a wide range of applications. They are often used for transporting hot and cold water and various industrial fluids.
Key Characteristics of PPR Pipe
- Corrosion Resistance: Unlike metal pipes, PPR pipes do not rust or corrode, providing a long-lasting solution for fluid transport.
- High Thermal Resistance: PPR pipes can withstand temperatures up to 95°C (203°F), making them ideal for both hot and cold water systems.
- Chemical Resistance: PPR is resistant to a wide range of chemicals, making it suitable for transporting various industrial fluids.
- Lightweight: Their low weight makes PPR pipes easier to handle and install, reducing labor costs and improving efficiency.
- Low Thermal Conductivity: PPR pipes minimize heat loss, making them energy-efficient for hot water applications.
Applications of PPR Pipe in Industry
PPR pipes are utilized in various industrial applications, including:
- Water Supply Systems: Suitable for transporting potable and non-potable water in municipal and industrial settings.
- Chemical Processing: Ideal for transporting chemicals and other aggressive fluids due to their chemical resistance.
- Heating Systems: Frequently used in radiant heating and hot water systems.
- Food and Beverage Industry: Safe for transporting potable water and certain food products, as PPR is free from toxic chemicals.
Advantages of Using PPR Pipe in Industrial Applications
The preference for PPR pipes in industrial settings can be attributed to several significant advantages:
1. Durability and Longevity
PPR pipes are known for their long lifespan, often exceeding 50 years with proper installation and maintenance. Their resistance to corrosion and scaling ensures that they remain functional without frequent replacements, making them a cost-effective solution for industrial applications.
2. Cost-Effectiveness
Although the initial cost of PPR pipes might be higher than traditional metal pipes, their long-term benefits outweigh the initial investment. PPR pipes require minimal maintenance and have a lower risk of leaks, leading to reduced repair costs and downtime in industrial operations.
3. Energy Efficiency
The low thermal conductivity of PPR pipes helps maintain the temperature of the fluids transported, reducing energy consumption in heating systems. This characteristic is particularly beneficial for industries that rely on hot water or steam.
4. Ease of Installation
PPR pipes are lightweight and easy to handle, simplifying the installation process. The hot melt welding technique used for joining PPR pipes allows for quick and secure connections, further speeding up the installation time and reducing labor costs.
5. Versatile Applications
PPR pipes can be adapted for various applications, from water supply to chemical transport. Their versatility makes them an attractive option for industries that require flexibility in their piping systems.
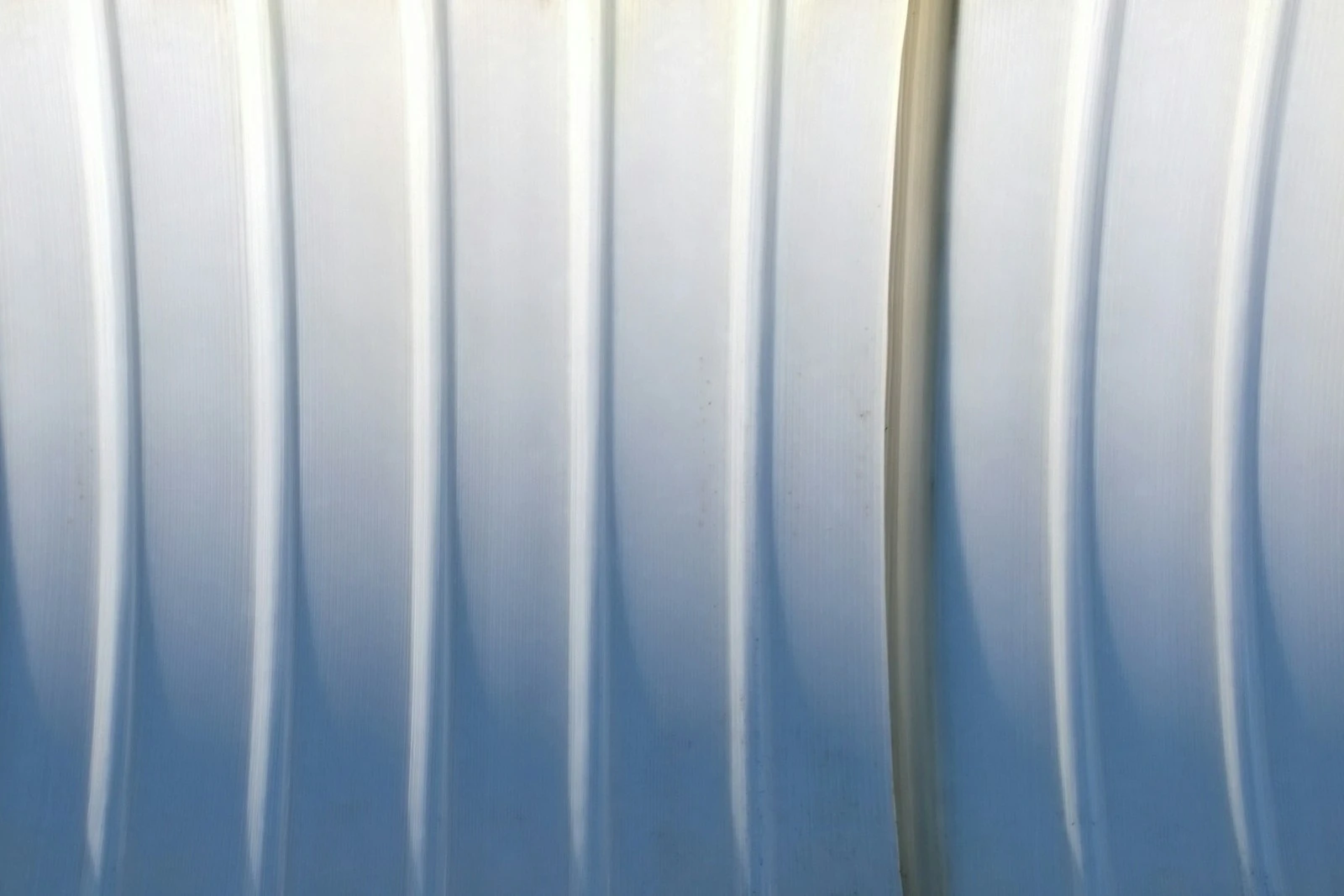
The Hot Melt Welding Process
Hot melt welding is the primary method for joining PPR pipes. This technique involves heating the ends of the pipes and fittings until they become molten, allowing them to fuse together upon cooling. Here’s a detailed overview of the hot melt welding process.
Step-by-Step Guide to Hot Melt Welding
Gather Necessary Tools
Before starting, ensure you have the following tools and equipment:
- PPR pipes and fittings
- Hot melt welding machine
- Pipe cutter
- Deburring tool
- Measuring tape
- Safety gear (gloves, goggles)
Prepare the Pipe
- Measure and Cut: Use a measuring tape to determine the required length of the PPR pipe and cut it using a pipe cutter.
- Deburr the Edges: Smooth the cut edges with a deburring tool to prevent leaks and ensure a tight fit.
Heating the Pipe and Fitting
- Set Temperature: Adjust the hot melt welding machine to the recommended temperature, typically around 260°C (500°F).
- Insert into Heater: Place the ends of the pipe and fitting into the heating element of the machine. Allow them to heat for approximately 30-45 seconds.
Joining the Components
- Remove from Heat: Carefully take the heated components out of the machine.
- Join Quickly: Insert the heated pipe end into the fitting with a twisting motion to ensure even distribution of the molten material.
- Hold Together: Maintain pressure for a few seconds to allow the joint to cool and solidify.
Inspection
After cooling, inspect the joint for any defects. A successful joint will be smooth and uniform. If you notice any issues, consider redoing the joint to ensure integrity.
PPR Pipe Challenges and Solutions
While PPR pipes have many advantages, there are also challenges that industries may face when using them. Here are some common challenges and potential solutions:
1. Temperature Sensitivity
PPR pipes can be sensitive to extreme temperatures, which can cause deformation. It’s essential to avoid exposing the pipes to direct sunlight or high-temperature environments.
Solution: Use insulation for pipes exposed to high temperatures or direct sunlight to maintain their integrity.
2. Proper Installation Techniques
Incorrect installation can lead to leaks or system failures. Ensuring that all technicians are adequately traine in hot melt welding and installation techniques is vital.
Solution: Provide comprehensive training for staff on installation practices and the importance of following manufacturer guidelines.
3. Compatibility with Other Materials
In some cases, PPR pipes may need to be connected to other types of piping materials, which can lead to compatibility issues.
Solution: Use appropriate fittings and transition pieces designed for compatibility between different materials.
Conclusion PPR Pipe
The preference for PPR pipes in industrial pipe fittings is driven by their numerous advantages, including durability, cost-effectiveness, energy efficiency, and ease of installation. As industries continue to seek reliable and efficient solutions for fluid transport, PPR pipes will remain a popular choice for various applications. Understanding the hot melt welding process and addressing potential challenges will further enhance the effectiveness of PPR pipes in industrial settings.
Frequently Asked Questions (FAQs)
- What are the main benefits of PPR pipes over traditional metal pipes?
- PPR pipes are corrosion-resistant, lightweight, energy-efficient, and have a longer lifespan compared to metal pipes.
- Can PPR pipes be use for both hot and cold water applications?
- Yes, PPR pipes are suitable for both hot and cold water systems, with a temperature tolerance up to 95°C (203°F).
- How long do PPR pipes typically last?
- PPR pipes can last over 50 years with proper installation and maintenance.
- Is the hot melt welding process difficult to learn?
- With proper training and practice, the hot melt welding process can be mastered relatively quickly, allowing for efficient installations.
- Are PPR pipes environmentally friendly?
- Yes, PPR pipes are recyclable and do not contain harmful chemicals, making them an eco-friendly choice for piping systems.