Introduction
The demand for high-density polyethylene HDPE pipe has been rising steadily due to their versatility and sustainability. As industries increasingly adopt eco-friendly practices, establishing a new HDPE pipe manufacturing plant in 2024 is both timely and strategic. This article explores the setup of an HDPE pipe manufacturing unit, the key considerations involved, and the prevailing trends shaping the industry.
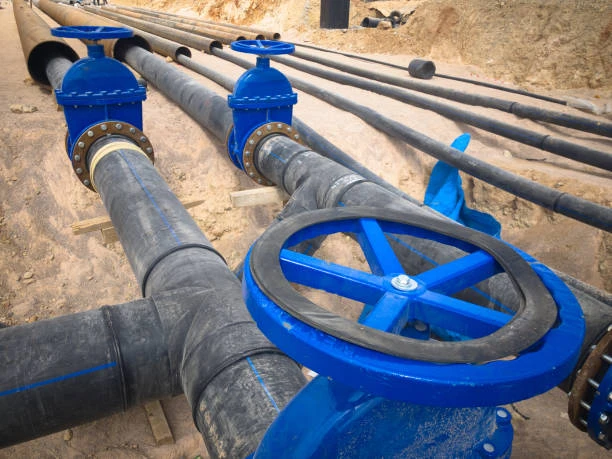
Understanding HDPE Pipe
High-density polyethylene (HDPE) pipes are widely used in various sectors, including water supply, wastewater management, and industrial applications. Made from high-density polyethylene resin, these pipes are known for their strength, durability, and resistance to corrosion, making them suitable for a broad range of applications.
Key Properties of HDPE Pipe
- Durability: HDPE pipes have a lifespan of over 50 years, significantly reducing maintenance costs.
- Flexibility: Their flexibility allows for easier installation in various terrains, accommodating ground movement.
- Chemical Resistance: HDPE pipes resist a wide range of chemicals, making them ideal for industrial applications.
- Sustainability: HDPE is recyclable, contributing to a circular economy and reducing plastic waste.
Setting Up an HDPE Pipe Manufacturing Plant
Establishing an HDPE pipe manufacturing plant involves several key steps. Each step requires careful planning and execution to ensure a successful operation.
1. HDPE pipe Market Research
Before setting up a plant, conducting thorough market research is essential. This research should include:
- Demand Analysis: Assess the demand for HDPE pipes in various sectors, including municipal, agricultural, and industrial markets.
- Competitive Landscape: Identify existing manufacturers and analyze their strengths and weaknesses.
- Pricing Strategy: Understand the pricing structure in the market to position your product competitively.
2. HDPE pipe Business Plan Development
A comprehensive business plan should outline the plant’s objectives, strategies, and financial projections. Key components include:
- Executive Summary: A brief overview of the business and its goals.
- Market Analysis: Insights gathered from the market research phase.
- Operational Plan: Details on manufacturing processes, equipment needed, and production capacity.
- Financial Projections: Expected costs, revenue forecasts, and break-even analysis.
3. HDPE pipe Location Selection
Choosing the right location for the manufacturing plant is crucial. Factors to consider include:
- Proximity to Raw Materials: Ensure access to HDPE resin and other materials to minimize transportation costs.
- Access to Markets: Select a location with easy access to major markets for efficient distribution.
- Labor Availability: Consider the availability of skilled labor in the region.
4. HDPE pipe Obtaining Permits and Licenses
Before construction begins, it is necessary to obtain the required permits and licenses. This process may involve:
- Environmental Clearances: Ensuring compliance with environmental regulations to mitigate the plant’s ecological impact.
- Construction Permits: Securing the necessary approvals for building and operating the facility.
5. Plant Design and HDPE pipe Layout
Designing an efficient plant layout can optimize production processes. Key considerations include:
- Flow of Materials: Ensure a logical flow from raw material input to finished product output.
- Safety Measures: Incorporate safety features to protect workers and equipment.
- Space Allocation: Allocate adequate space for storage, manufacturing, quality control, and administrative functions.
6. Equipment Procurement
Selecting the right equipment is vital for efficient manufacturing. Key machinery includes:
- Extruders: For shaping HDPE resin into pipes.
- Cooling Systems: To cool and solidify the extruded pipes.
- Cutting Machines: For cutting pipes to the desired lengths.
- Quality Control Equipment: For testing the quality of finished products.
7. Workforce Hiring and HDPE pipe Training
Recruiting a skilled workforce is essential for the plant’s success. Training programs should cover:
- Operational Training: Ensuring employees are proficient in operating machinery and adhering to safety protocols.
- Quality Control Training: Educating staff on quality assurance processes to maintain product standards.
8. Marketing and HDPE pipe Distribution Strategy
Once the plant is operational, developing a robust marketing and distribution strategy is essential. Key components include:
- Brand Development: Creating a strong brand identity to differentiate your products.
- Sales Channels: Identifying direct sales, distributors, and online platforms for reaching customers.
- Customer Relationships: Building relationships with key customers and stakeholders for repeat business.
Industry Trends Influencing HDPE Pipe Manufacturing
The HDPE pipe manufacturing industry is evolving, driven by several key trends that are shaping its future.
1. Increased Demand for HDPE pipe Sustainable Solutions
With growing environmental concerns, industries are seeking sustainable solutions. HDPE pipes offer eco-friendly alternatives to traditional materials, supporting the trend toward sustainability. This shift is prompting more manufacturers to adopt HDPE pipes in their projects.
2. HDPE pipe Technological Advancements
Innovations in manufacturing technology are improving the efficiency and quality of HDPE pipes. Advancements such as:
- Automation: Implementing automated systems in manufacturing processes reduces labor costs and increases production speed.
- Smart Manufacturing: Utilizing IoT (Internet of Things) technologies for real-time monitoring and data analysis enhances operational efficiency.
3. Regulatory Compliance and HDPE pipe Standards
Governments worldwide are implementing stricter regulations regarding materials used in construction and infrastructure projects. Compliance with these regulations is essential for manufacturers to maintain market access. Staying updated with industry standards will be crucial for HDPE pipes manufacturers.
4. Expansion in Emerging Markets
Emerging markets, particularly in Asia and Africa, are witnessing rapid urbanization and infrastructure development. This presents significant opportunities for HDPE pipes manufacturers to expand their operations and meet the growing demand.
5. Focus on Recycling and HDPE pipes Circular Economy
As part of the global push toward sustainability, there is an increasing focus on recycling HDPE pipes. Manufacturers are encouraged to implement recycling processes to reduce waste and contribute to a circular economy.
Challenges in HDPE Pipe Manufacturing
While the outlook for HDPE pipes manufacturing is positive, several challenges need to be addressed:
1.HDPE pipe Competition
The growing popularity of HDPE pipes has led to increased competition in the market. New entrants must differentiate themselves through quality, innovation, and customer service.
2. HDPE pipes Raw Material Price Fluctuations
The cost of HDPE resin can fluctuate due to market dynamics, impacting production costs. Manufacturers need to develop strategies for managing raw material costs effectively.
3. HDPE pipe Workforce Development
Finding skilled labor in manufacturing can be challenging. Companies must invest in training programs to ensure employees are well-equipped to handle advanced manufacturing processes.
4. HDPE pipe Environmental Regulations
Compliance with environmental regulations can be complex and costly. Manufacturers must remain proactive in ensuring their operations align with these regulations.
The Future of HDPE Pipe Manufacturing
The future of HDPE pipes manufacturing is bright, with opportunities for growth and innovation. As sustainability continues to drive industry trends, manufacturers that prioritize eco-friendly practices will likely thrive.
Investment in Research and HDPE pipe Development
Investing in R&D will enable manufacturers to innovate and improve product quality. Developing new HDPE formulations can enhance performance and expand applications.
Strategic Partnerships
Forming strategic partnerships with suppliers, distributors, and industry stakeholders can enhance market reach and operational efficiency. Collaborations can lead to shared resources and knowledge, fostering growth.
HDPE pipe Embracing Digital Transformation
Adopting digital technologies will play a critical role in the future of HDPE pipes manufacturing. From smart manufacturing processes to data analytics, digital transformation can improve operational efficiency and customer engagement.
Conclusion
Establishing an HDPE pipes manufacturing plant in 2024 presents a significant opportunity for growth in a burgeoning industry. By understanding the setup process and the current trends influencing the market, manufacturers can position themselves for success. With a focus on sustainability, technological advancements, and strategic partnerships, the future of HDPE pipes looks promising.
FAQs
1. What are HDPE pipes commonly used for?
HDPE pipes are used for water supply, wastewater management, irrigation, and various industrial applications due to their durability and flexibility.
2. What factors should be considered when setting up an HDPE pipes manufacturing plant?
Key factors include market research, location selection, obtaining permits, equipment procurement, and workforce training.
3. How do HDPE pipes contribute to sustainability?
HDPE pipes are recyclable and have a long lifespan, reducing waste and supporting a circular economy.
4. What challenges do HDPE pipes manufacturers face?
Challenges include competition, raw material price fluctuations, workforce development, and compliance with environmental regulations.
5. What trends are shaping the HDPE pipes manufacturing industry?
Current trends include increased demand for sustainable solutions, technological advancements, regulatory compliance, and a focus on recycling and circular economy practices.