High-Density Polyethylene HDPE pipe are becoming increasingly important in various industries, from water supply to gas distribution and beyond. The extrusion process plays a pivotal role in manufacturing these pipes, ensuring their quality and performance. In recent months, several noteworthy developments have emerged in the field of HDPE pipe extrusion and profiles. This article will explore these recent news highlights, advancements in extrusion technology, the benefits of HDPE pipes, and future trends in the industry.
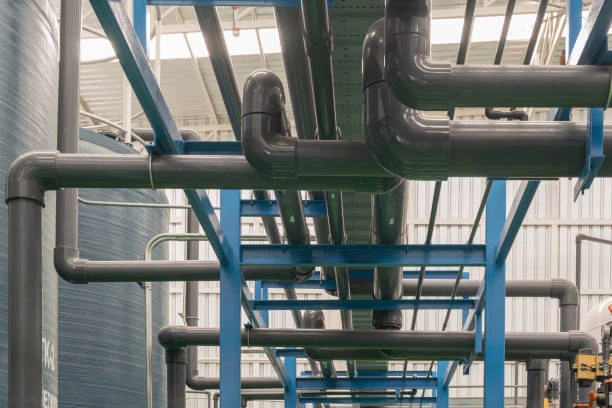
Understanding HDPE Pipe and Their Applications
Before delving into the latest news, it is crucial to understand what HDPE pipes are and why they are favored in various applications.
What Are HDPE Pipe?
HDPE pipes are made from high-density polyethylene, a thermoplastic polymer known for its high strength-to-density ratio. This material is used to create pipes that are flexible, durable, and resistant to corrosion, making them ideal for various applications, including:
- Water Supply: HDPE pipes are widely used in municipal water supply systems due to their resistance to chemicals and ability to handle high pressure.
- Sewage and Drainage: They are effective for transporting sewage and stormwater, providing a reliable solution for drainage systems.
- Gas Distribution: HDPE pipes are employed in the gas industry for transporting natural gas and other gases safely and efficiently.
- Industrial Applications: Various industries utilize HDPE pipes for transporting chemicals, slurries, and other materials.
Key Benefits of HDPE Pipe
- Durability: HDPE pipes can last over 50 years with proper installation and maintenance, reducing the need for frequent replacements.
- Flexibility: Their flexibility allows for easy installation, even in challenging terrains.
- Corrosion Resistance: HDPE is resistant to corrosion and chemicals, ensuring the integrity of the transported materials.
- Cost-Effectiveness: Although initial costs may be higher than traditional materials, the long-term savings in maintenance and replacements make HDPE pipes a wise investment.
- Environmental Impact: HDPE pipes are recyclable, contributing to sustainable practices in infrastructure development.
Recent News in HDPE Pipe Extrusion
1. Advances in Extrusion Technology
Recent advancements in extrusion technology have led to the production of higher-quality HDPE pipes. Companies are investing in state-of-the-art machinery and techniques to improve efficiency and output quality. Innovations such as multi-layer extrusion processes allow manufacturers to create pipes with enhanced properties, such as increased pressure ratings and better chemical resistance.
2. Increased Demand in Infrastructure Projects
With governments worldwide increasing their investments in infrastructure development, the demand for HDPE pipes is on the rise. This surge is particularly evident in urban areas where aging water and sewage systems require urgent upgrades. As cities expand, the need for durable and reliable piping solutions becomes critical, driving the market for HDPE pipes and profiles.
3. Sustainability Initiatives
The industry is seeing a growing emphasis on sustainability. Manufacturers are focusing on reducing the environmental impact of HDPE pipe production through more efficient extrusion processes and utilizing recycled materials. Some companies have started to incorporate bio-based HDPE, which reduces reliance on fossil fuels and lowers carbon footprints.
4. Regulatory Changes
Recent regulatory changes in various regions are also influencing the HDPE pipe market. Stricter standards for water quality and environmental protection are pushing manufacturers to adopt better practices and technologies. Compliance with these regulations is driving innovation in HDPE extrusion processes and material formulations.
5. Market Expansion
Companies are exploring new markets for HDPE pipes, particularly in developing countries where infrastructure development is a priority. The globalization of the HDPE pipe market is leading to increased collaboration between manufacturers and local suppliers, facilitating knowledge transfer and technology sharing.
The Extrusion Process: A Closer Look
Understanding the extrusion process is essential for appreciating how HDPE pipes are manufactured. Here’s a breakdown of the key stages involved:
1. Material Preparation
The process begins with the preparation of raw HDPE pellets. These pellets are selecte based on the required specifications for the final product, including density, melt flow index, and other performance characteristics.
2. Feeding
The prepared HDPE pellets are fed into the extruder, where they are heate and melted. This is typically do using a series of heating zones that gradually increase the temperature, allowing the material to reach a molten state.
3. Extrusion
Once melted, the HDPE is force through a die, which shapes the material into the desired profile. For pipes, this typically involves a round die that creates a continuous pipe shape.
4. Cooling
After exiting the die, the newly formed HDPE pipe is coole using water or air. This step solidifies the material and retains the shape.
5. Cutting and Finishing
Finally, the coole pipe is cut to the desired lengths and may undergo additional finishing processes, such as surface treatment or adding markings.
The Future of HDPE Pipe Extrusion
As we look ahead, several trends are expecte to shape the future of HDPE pipe extrusion:
1. Smart Technology Integration
The integration of smart technologies into the extrusion process is anticipate to enhance efficiency and quality control. Sensors and data analytics can provide real-time feedback on the extrusion process, allowing for immediate adjustments and improvements.
2. HDPE pipe Customization and Tailored Solutions
With the increasing demand for specialized piping solutions, manufacturers will likely focus on customization. This may involve developing HDPE pipes with specific properties tailored to unique applications or environmental conditions.
3. HDPE pipe Growth in Recycling Initiatives
As sustainability becomes a more pressing concern, the recycling of HDPE pipes will gain traction. Closed-loop systems, where old HDPE pipes are collecte, recycled, and reprocessed into new products, will become more common.
4. HDPE pipe Expansion into New Applications
As the versatility of HDPE pipes is recognize, manufacturers may explore new applications beyond traditional uses. Industries such as telecommunications and electrical utilities may increasingly adopt HDPE piping solutions for various infrastructure needs.
5. HDPE pipe Regulatory Compliance and Innovation
Continued pressure from regulatory bodies will push manufacturers to innovate and comply with stricter environmental and safety standards. This will drive research and development in new materials and extrusion techniques.
Conclusion
The recent news surrounding HDPE pipe extrusion highlights the dynamic nature of the industry and the ongoing innovations that are shaping its future. With advancements in technology, a growing focus on sustainability, and increased demand for reliable piping solutions, HDPE pipes are well-positione to meet the challenges of modern infrastructure needs. As manufacturers continue to evolve and adapt, the potential for HDPE pipes and profiles remains significant, offering a promising outlook for the industry.
Frequently Asked Questions (FAQs)
- What are HDPE pipes used for? HDPE pipes are use for various applications, including water supply, sewage and drainage systems, gas distribution, and industrial transport.
- What are the benefits of using HDPE pipe? Benefits include durability, flexibility, chemical resistance, cost-effectiveness, and environmental sustainability.
- How is the extrusion process performe for HDPE pipe? The extrusion process involves feeding HDPE pellets into an extruder, melting them, shaping them through a die, cooling, and cutting them to length.
- What recent trends are influencing the HDPE pipe market? Recent trends include advances in extrusion technology, increased demand for infrastructure projects, sustainability initiatives, regulatory changes, and market expansion.
- How does HDPE pipe recycling work? HDPE pipe recycling involves collecting used pipes, processing them into pellets, and using those pellets to produce new HDPE products, supporting a circular economy.