In the world of chemical processing, achieving purity and precision is paramount. One of the critical components in this process is the control valve. Particularly in the production of vanadium oxides, which are essential for various industrial applications, the choice and operation of control valves can significantly impact the quality of the final product. This article delves into the role of control valves in the manufacturing of the world’s purest vanadium oxides, exploring their types, functions, benefits, and best practices for their application.
Understanding Control Valves
Control valves are devices used to regulate the flow of fluids by varying the size of the flow passage. They play a vital role in controlling process variables such as temperature, pressure, and flow rate, ensuring that operations run smoothly and efficiently. In the production of vanadium oxides, precise control is necessary to maintain the integrity and purity of the product.
Types of Control Valves
Several types of control valves are commonly used in industrial applications, including:
- Globe Valves:
Known for their excellent throttling capabilities, globe valves are often used in applications where precise flow control is required. - Ball Valves:
These provide a quick on-off control but can also be used for throttling in some designs, making them versatile for various applications. - Butterfly Valves:
Lightweight and space-efficient, butterfly valves are suitable for larger volumes and are often used in the vanadium oxide production process due to their quick operation. - Diaphragm Valves:
Ideal for handling corrosive fluids, diaphragm valves provide tight sealing, making them suitable for applications requiring high purity.
The Importance of Control Valves in Vanadium Oxide Production
Vanadium oxides are used in a range of applications, from catalysts in chemical processes to components in batteries and alloys. The production process often involves multiple steps, including the extraction of vanadium from ores, purification, and conversion to various oxide forms. Each of these steps requires careful monitoring and control of various parameters, which is where control valves come into play.
Ensuring Product Purity
In the production of vanadium oxides, the purity of the final product is crucial. Contaminants can significantly affect the properties of the oxides, leading to inferior performance in their applications. Control valve ensure that the right amounts of raw materials are used, and that the process conditions are kept within specified limits. This helps in minimizing the introduction of impurities, thus enhancing the purity of the vanadium oxides produced.
Enhancing Process Efficiency
Efficient production processes are not only cost-effective but also environmentally friendly. By employing control valves effectively, manufacturers can optimize their operations. For instance, proper flow control can reduce waste and energy consumption. Which leading to lower operational costs and a smaller environmental footprint.
Facilitating Automation
Modern industrial processes are increasingly automated. Control valves are integral to these systems, enabling real-time adjustments based on data from sensors and monitoring systems. This automation ensures that production processes remain stable and consistent, further contributing to the quality of the vanadium oxides produced.
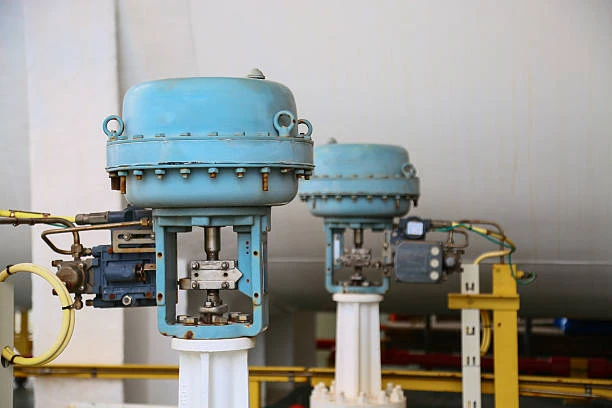
Best Practices for Control Valve Selection
When selecting control valves for vanadium oxide production, several factors should be considered to ensure optimal performance:
1. Material Compatibility
Given the corrosive nature of some chemicals involved in vanadium oxide production, it is essential to select control valves made from materials that can withstand these conditions. Common materials include stainless steel, bronze, and various plastics, depending on the specific application.
2. Size and Flow Characteristics
The size of the control valve must match the flow requirements of the system. An incorrectly sized valve can lead to issues such as cavitation or excessive pressure drops. Which both of which can affect product quality. Consulting with a flow expert can help determine the correct sizing.
3. Control Type
Different applications may require different types of control. For instance, some processes may benefit from continuous flow control, while others may require on/off control. Understanding the specific needs of the vanadium oxide production process is essential in selecting the right control valve.
4. Maintenance Requirements
Regular maintenance is crucial for ensuring the longevity and reliability of control valves. Selecting valves that are easy to maintain can help minimize downtime and improve overall operational efficiency.
Conclusion
Control valve play a pivotal role in the production of the world’s purest vanadium oxides. By ensuring precise control of process variables, they contribute to the purity, efficiency, and automation of production processes. By following best practices in selection and maintenance, manufacturers can enhance their operations. Which leading to higher quality products that meet the demands of various industries.
Frequently Asked Questions (FAQs)
1. What is the role of control valve in vanadium oxide production?
Control valves regulate the flow of materials and maintain process conditions, ensuring the purity and quality of vanadium oxides.
2. How do I choose the right control valve for my application?
Consider factors such as material compatibility, size, flow characteristics, and maintenance requirements when selecting a control valve.
3. What types of control valves are commonly used in industrial applications?
Common types include globe valves, ball valves, butterfly valves, and diaphragm valves, each with specific advantages for different applications.
4. How can control valve improve process efficiency?
By optimizing flow rates and reducing waste, control valves help minimize operational costs and enhance the overall efficiency of production processes.
5. Why is automation important in the production of vanadium oxides?
Automation allows for real-time monitoring and adjustments, ensuring stable production conditions and consistent quality in the final product.