The world of injection molding is constantly evolving, driven by the need for efficiency, precision, and innovation. One of the latest advancements in this field is the introduction of new valve-gate end rings and hot runner controls. These technologies are transforming the way manufacturers approach the injection molding process, enhancing quality and reducing waste. This article explores the significance of valve-gate systems, the benefits of the new end rings, and how hot runner controls play a crucial role in optimizing production.
Understanding Valve-Gate Systems
Valve-gate technology is a method used in injection molding that allows for precise control over the flow of molten plastic into the mold cavity. Unlike traditional methods that rely on open gates, valve-gate systems utilize mechanical or pneumatic actuators to open and close the gate, ensuring a controlled flow of material. This approach offers several advantages, including improved surface finish, reduced material wastage, and enhanced cycle times.
Key Components of Valve-Gate Systems
- Valve-Gate Actuator: This component controls the opening and closing of the gate, ensuring that the flow of plastic is precisely managed.
- End Rings: These are critical components that interface with the mold. They play a vital role in sealing the gate and preventing leaks during the injection process.
- Hot Runner System: This system keeps the plastic in a molten state, allowing for quicker cycle times and better material flow control.
The Importance of End Rings in Valve-Gate Systems
End rings are essential in ensuring the effective operation of valve-gate systems. They help maintain pressure within the mold cavity during the injection process and facilitate the seamless opening and closing of the gates.
Benefits of New Valve-Gate End Rings
- Improved Sealing: The new designs of valve-gate end rings offer enhanced sealing capabilities, reducing the risk of material leakage and ensuring that the injected plastic fills the mold cavity uniformly.
- Durability: Advanced materials used in the new end rings provide greater resistance to wear and tear, extending the lifespan of the components and reducing maintenance costs.
- Ease of Installation: The new end rings are designed for easier installation, allowing manufacturers to reduce downtime during setup and maintenance.
- Precision Engineering: Improved manufacturing techniques have resulted in end rings with tighter tolerances, leading to better fit and function in valve-gate systems.
- Cost Efficiency: By minimizing waste and enhancing the overall efficiency of the injection molding process, the new valve-gate end rings contribute to lower operational costs.
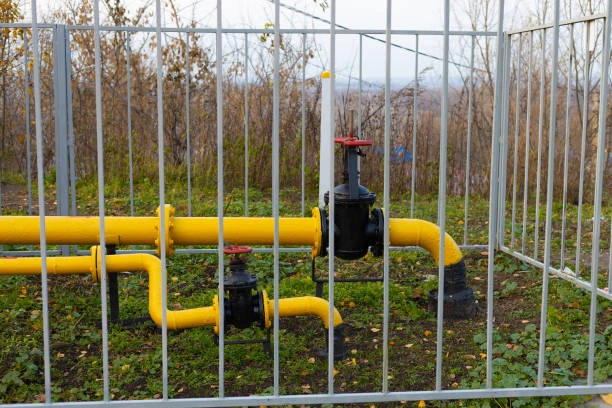
Hot Runner Controls: Enhancing Injection Molding Efficiency
Hot runner systems are integral to modern injection molding processes. They maintain the molten state of the plastic from the injection unit to the mold. Which ensuring consistent flow and minimizing cycle times. Hot runner controls are the technological backbone that optimizes this system.
Features of Advanced Hot Runner Controls
- Temperature Regulation:
Advanced hot runner controls provide precise temperature management throughout the system. Which ensuring that the plastic remains at the optimal processing temperature. - Flow Control:
These controls allow for dynamic adjustment of flow rates. Which providing manufacturers with the flexibility to adapt to different materials and product designs. - Real-Time Monitoring:
Modern hot runner controls are equipped with sensors and monitoring systems that provide real-time data on system performance. Which enabling quick adjustments and preventive maintenance. - Energy Efficiency:
By maintaining consistent temperatures and reducing material waste, advanced hot runner controls contribute to lower energy consumption, making the injection molding process more sustainable. - Integration with Automation:
Hot runner controls can be integrated with automated systems. Which allowing for seamless operation and enhanced productivity in the injection molding process.
The Synergy Between Valve-Gate End Rings and Hot Runner Controls
The combination of new valve-gate end rings and advanced hot runner controls represents a significant leap forward in injection molding technology. Together, they enhance the overall performance of the molding process, offering manufacturers numerous advantages.
Improved Quality and Consistency
The precise control offered by valve-gate systems, coupled with the efficiency of hot runner controls, results in high-quality molded products with consistent surface finishes and dimensional accuracy. This level of quality is essential for industries that demand precision, such as automotive, medical devices, and consumer electronics.
Reduced Cycle Times
The integration of these technologies allows for faster cycle times. As the hot runner systems enable quicker transitions between injection cycles. This efficiency not only increases productivity but also reduces the time required to bring products to market.
Minimized Material Waste
With improved sealing capabilities from the new valve-gate end rings and optimized flow control from the hot runner systems. Which manufacturers can significantly reduce material waste. This is particularly important in today’s manufacturing environment, where sustainability is a growing concern.
Future Trends in Valve-Gate Technology
As the injection molding industry continues to evolve, several trends are emerging in valve-gate technology:
- Increased Automation:
The integration of automation in injection molding processes will continue to grow, enhancing efficiency and reducing labor costs. - Smart Manufacturing:
The adoption of IoT (Internet of Things) technologies will allow for smarter manufacturing processes. Where data analytics play a crucial role in optimizing production. - Sustainable Materials:
As the industry shifts toward sustainability, the use of biodegradable and recyclable materials in conjunction with advanced valves-gate and hot runner technologies will become more prevalent. - Customization and Flexibility:
Manufacturers will increasingly seek flexible solutions that can adapt to varying production needs. Which requiring valve-gate systems and hot runner controls that offer configurability and ease of adjustment.
Conclusion
The introduction of new valves-gate end rings and advanced hot runner controls marks a significant milestone in the evolution of injection molding technology. These innovations enhance the efficiency, quality, and sustainability of the molding process, addressing the demands of modern manufacturing. As industries continue to seek ways to optimize production while minimizing environmental impact. And the role of valve-gate systems will only become more crucial.
By investing in these technologies, manufacturers can improve their operational efficiency, reduce waste, and deliver high-quality products that meet the ever-increasing standards of the market. The future of injection molding looks promising, driven by continuous innovation and the commitment to excellence.
Frequently Asked Questions (FAQs)
- What are valves-gate systems?
Valves-gate systems are injection molding technologies that control the flow of molten plastic using mechanical or pneumatic actuators. Which ensuring precise material injection. - What are the benefits of new valves-gate end rings?
New valves-gate end rings offer improved sealing, durability, ease of installation, precision engineering, and cost efficiency. - How do hot runner controls enhance injection molding?
Hot runner controls provide precise temperature regulation, flow control, real-time monitoring, energy efficiency, and integration with automation systems. - Why is reducing material waste important in injection molding?
Minimizing material waste is essential for sustainability, reducing operational costs, and improving overall efficiency in the manufacturing process. - What future trends are expected in valve-gate technology?
Future trends include increased automation, smart manufacturing, sustainable materials, and customizable solutions to meet diverse production needs.