In industrial facilities, particularly those handling hazardous materials or operating in potentially explosive environments, valves play a crucial role in controlling the flow of fluids or gases. However, over time, valves can develop leaks, posing significant risks to both safety and operational efficiency. Detecting these leaks early is critical, and an effective inspection system for leak detection in valves can help mitigate these risks by ensuring the proper functioning of valves in hazardous areas.
In this article, we will explore the importance of leak detection in valves, the challenges associated with inspecting valves in hazardous areas, and the role of advanced technologies and inspection systems in ensuring safety and compliance.
The Importance of Valves in Hazardous Areas
Valves are essential components in fluid and gas handling systems. They control the flow of liquids, gases, and slurries in pipes, tanks, and equipment across various industries, including oil and gas, chemical manufacturing, pharmaceuticals, and power generation. In hazardous areas, valves serve an even more critical function, as they ensure that hazardous materials are properly contain and transported, preventing leaks that could lead to accidents, fires, or explosions.
These valves are typically locate in areas where dangerous chemicals, flammable gases, or volatile liquids are being transported or process. Therefore, even the smallest leak can result in catastrophic consequences, including environmental damage, equipment failure, and loss of life. As such, regular inspections and proactive leak detection systems are essential for maintaining the integrity and safety of these systems.
The Risks of Valve Leaks in Hazardous Areas
Leaks in valves in hazardous areas pose several risks, including:
- Safety Hazards: Leaking valves can release harmful chemicals, gases, or liquids into the environment, posing a direct threat to personnel working in or near the area. Exposure to toxic or flammable substances can lead to injuries, illnesses, or even fatalities.
- Environmental Impact: A significant leak could result in harmful substances being discharge into the surrounding environment, leading to soil, water, or air contamination. This can have long-lasting ecological consequences and could result in fines or legal actions.
- Operational Disruption: Leaking valves can interfere with the normal operation of industrial systems, leading to reduced efficiency, equipment damage, and unscheduled downtime. This disruption can cause financial losses, especially in industries where production uptime is critical.
- Regulatory Compliance Issues: Industrial plants must comply with stringent safety regulations to ensure that systems in hazardous areas are properly maintain and free from leaks. Failure to identify and address leaks can result in penalties, fines, and potential shutdowns.
Traditional Leak Detection Methods for Valves
Traditionally, leak detection in valves was performed through manual inspections, which involved visually checking valves for signs of leakage, as well as using basic tools like pressure gauges or hand-held detectors. However, this approach is not only labor-intensive but also prone to human error. In hazardous areas, where the risks of exposure to dangerous substances are high, manual inspections are often inadequate.
Traditional leak detection methods include:
- Visual Inspections: Checking for obvious signs of leakage such as damp spots, corrosion, or pooling of liquids around the valve. This method is useful but cannot detect leaks that are small, slow, or hidden behind equipment.
- Pressure Monitoring: Using pressure gauges to monitor the pressure drop across valves, which could indicate a leak. While this method is effective for detecting significant leaks, it may not identify small, gradual leaks that pose a long-term risk.
- Sound Detection: Listening for unusual sounds like hissing or dripping that may indicate a leak. This method can be effective for identifying certain types of leaks but is limited by environmental factors, such as noise interference or access restrictions.
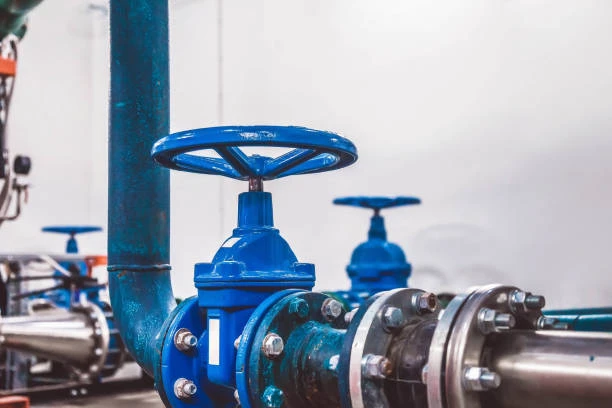
Advanced Inspection Systems for Leak Detection in Valves
As industries increasingly rely on automation and advanced technologies, traditional leak detection methods are being supplemented or replaced by more sophisticated systems. Modern inspection technologies can detect even the smallest leaks in valves with higher accuracy, improving safety and minimizing downtime in hazardous areas.
Here are some of the most advanced inspection systems for leak detection in valves in hazardous areas:
1. Acoustic Emission Monitoring
Acoustic emission monitoring is an advanced technique that detects high-frequency sounds produced by the leakage of fluids or gases from valves. When a valve develops a leak, it can produce high-frequency acoustic signals that can be picked up by sensors placed near the valve. These sensors can be installed in hazardous areas to continuously monitor for leaks.
Key benefits of acoustic emission monitoring include:
- Continuous Monitoring: It allows for real-time monitoring of valve health, providing early detection of leaks before they become a serious issue.
- Non-invasive: Acoustic sensors can be installed without interrupting valve operation, making it suitable for use in live systems.
- Sensitive Detection: This system can detect very small leaks that may be difficult to identify through visual inspection or pressure monitoring.
2. Infrared Thermography
Infrared thermography uses infrared cameras to detect temperature differences around valves and pipelines. Leaks in valves often lead to temperature changes due to the loss of fluid or gas under pressure. An infrared camera can capture these temperature variations, alerting maintenance teams to potential leaks.
Benefits of infrared thermography include:
- Non-destructive: It does not require any physical contact with the valve, making it ideal for hazardous environments.
- Wide Area Coverage: Infrared thermography can be useful to inspect large sections of pipelines and valves quickly.
- Visual Alerts: Operators can quickly identify potential leaks on the thermal images, speeding up the troubleshooting process.
3. Gas Detectors and Sensors
For facilities that handle hazardous gases, gas detectors are crucial for identifying leaks from valves. These detectors measure the concentration of specific gases in the air, triggering alarms when the levels exceed predefined thresholds. Many modern gas detectors are portable and can be useful to inspect valves on-site or remotely.
Advantages of gas detectors include:
- Real-Time Leak Detection: Gas detectors provide immediate feedback, allowing operators to respond quickly to potential hazards.
- Targeted Detection: Gas sensors can be customize to detect a wide range of gases, including toxic, flammable, or corrosive substances.
- Automation: In some systems, gas detectors are integrate into the facility’s automated control systems, enabling automatic shut-off or re-routing of gas flow in the event of a leak.
4. Smart Valves with Integrated Leak Detection
Some valves now come equipped with built-in sensors and monitoring systems that allow for real-time leak detection. These smart valves can monitor pressure, temperature, and other parameters to detect irregularities that could indicate a leak. If an issue is identify, the valve can send an alert to the control system, enabling immediate action to prevent further damage.
Benefits of smart valves with integrated leak detection:
- Integrated Monitoring: The system continuously checks the valve’s performance, providing a comprehensive picture of valve health.
- Automated Alerts: Immediate notifications can be sent to maintenance teams when a leak is detected, minimizing delays in response time.
- Predictive Maintenance: Smart valves often use predictive analytics to forecast potential issues, allowing for proactive maintenance and reducing the likelihood of unexpected failures.
5. Dye Penetrant Testing (for Static Valves)
For valves that are in a static position and not subjected to constant flow or pressure changes, dye penetrant testing is an effective inspection method. This involves applying a dye to the valve surface, which seeps into any cracks or defects. The excess dye is wipe away, and a developer is apply to highlight the presence of any leaks.
Advantages of dye penetrant testing:
- Visual Confirmation: This method provides clear, visual evidence of leaks, making it easy to identify and address issues.
- Cost-Effective: Dye penetrant testing is relatively inexpensive compare to other leak detection methods.
- Applicable to Static Valves: This method is best useful for valves that do not undergo constant operation but are still critical in hazardous environments.
Conclusion
Leak detection in valves is a vital part of maintaining safety and operational efficiency in hazardous areas. Traditional inspection methods are no longer sufficient to address the growing complexity and risks associated with modern industrial operations. Advanced inspection systems such as acoustic emission monitoring, infrared thermography, gas detectors, smart valves, and dye penetrant testing offer reliable, real-time solutions for detecting even the smallest leaks before they result in significant damage.
By adopting these advanced technologies, industrial facilities can minimize risks, ensure regulatory compliance, and improve overall system reliability. In hazardous environments where every second counts, investing in an effective leak detection system for valves is essential for safeguarding both people and the environment.
Frequently Asked Questions (FAQ)
- Why is leak detection important in valves in hazardous areas?
- Leak detection is crucial in hazardous areas to prevent the release of dangerous chemicals, gases, or liquids that could cause safety hazards, environmental damage, or operational disruptions.
- What are the common methods for detecting leaks in valves?
- Common methods include acoustic emission monitoring, infrared thermography, gas detectors, smart valves with integrated leak detection, and dye penetrant testing.
- How does acoustic emission monitoring work for valve leak detection?
- Acoustic emission monitoring detects high-frequency sounds produced by leaks in valves, allowing for real-time, non-invasive leak detection without interrupting system operation.
- Can gas detectors be useul for leak detection in hazardous areas?
- Yes, gas detectors are ideal for identifying leaks in hazardous areas. They measure the concentration of specific gases in the air and trigger alarms when thresholds are excellent.
- What is the role of smart valves in leak detection?
- Smart valves come with integrated sensors that continuously monitor pressure, temperature, and other parameters, allowing for real-time leak detection and automated alerts for maintenance teams.