Oerlikon HRS Flow, a leading global provider of hot runner systems for injection molding, has recently introduced a revolutionary innovation in their product lineup: the new Valve Gate End Rings for Nozzle Series. This advanced solution aims to improve the efficiency, quality, and overall performance of injection molding processes. This article will explore the significance of this innovation, focusing on the role of valve gates in hot runner systems, the technical benefits of the new end rings, and how they can optimize manufacturing operations.
Understanding Valve Gate Technology in Injection Molding
What is a Valve Gate?
A valve gate is an essential component in modern injection molding processes. It is used to control the flow of molten plastic into the mold cavity by acting as a gate that opens and closes during the injection cycle. Valve gate systems are crucial for achieving high-quality parts with precise control over the injection process. By allowing for better control of the material flow, valve gates help to reduce cycle times, improve part consistency, and minimize defects like weld lines, air traps, and flow marks.
Role of Valve Gates in Hot Runner Systems
In hot runner systems, valve gates are particularly beneficial. Hot runner systems are designed to keep the plastic material in a molten state as it travels from the injection molding machine to the mold cavity, preventing material waste and improving cycle efficiency. Valve gates control when and how the plastic flows into the mold cavities, making them integral to the overall hot runner system’s performance.
Valve gates are activated by an external mechanism, such as a pneumatic or hydraulic actuator, and they close and open based on the molding requirements. This precise control ensures that each cavity is filled evenly and with minimal residual pressure, leading to better product quality and reduced material consumption.
The Role of End Rings in Hot Runner Systems
What Are End Rings?
End rings are a key part of the nozzle assembly in hot runner systems. They serve as a connection point between the hot runner manifold and the nozzle itself. End rings play a critical role in the thermal regulation of the system, ensuring that the molten plastic maintains a consistent temperature throughout the flow path. In addition to thermal management, end rings also contribute to the mechanical integrity of the system, allowing for better alignment and support of the nozzle and valve gate.
How Do End Rings Impact Performance?
The performance of hot runner systems is highly dependent on the design and functionality of the end rings. Properly designed end rings help to ensure that the molten plastic flows smoothly, with minimal pressure loss, while maintaining a uniform temperature. The introduction of new valve gate end rings represents a significant advancement in this area, providing enhanced performance and greater reliability for injection molding systems.
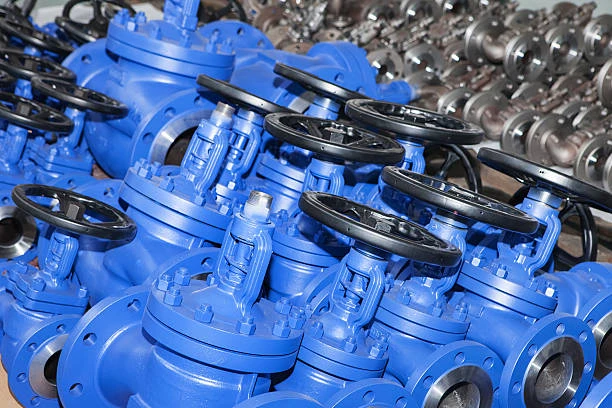
Oerlikon HRS Flow’s New Valve Gate End Rings for Nozzle Series
Key Features of the New Valve Gate End Rings
Oerlikon HRS Flow’s new valve gate end rings for nozzle series are designed to address the increasing demands of high-performance injection molding. These end rings feature several innovative upgrades that enhance both functionality and reliability:
- Optimized Flow Path:
The new valve gate end rings are engineered to improve the flow of molten plastic through the nozzle. Which reducing pressure drops and ensuring more uniform material distribution. This results in better quality molded parts and improved cycle times. - Improved Thermal Performance:
One of the standout features of the new end rings is their ability to maintain consistent temperatures across the nozzle and runner system. This is crucial for preventing material degradation and ensuring that the plastic remains in an optimal state throughout the injection process. - Durability and Long-Term Performance:
Oerlikon HRS Flow has used advanced materials and manufacturing processes to ensure that the valve gate end rings have enhanced durability. Which making them resistant to wear and tear. This longevity helps to reduce maintenance costs and downtime in production environments. - Precision Control:
The new valve gate end rings are designed to provide precise control over the flow of plastic. Which can reduce issues like short shots, overpacking, or misalignment of cavities. This control helps to improve part quality and reduce material waste. - Ease of Maintenance:
The new end rings are designed to be easy to maintain and service. Which minimizing downtime and improving the overall operational efficiency of injection molding systems.
Benefits of the New Valve Gate End Rings
The introduction of these new valve gate end rings offers a range of benefits for manufacturers in various industries, including automotive, consumer goods, packaging, and medical devices. Some of the key advantages include:
- Enhanced Process Stability: The precise control provided by the valve gate end rings leads to a more stable and predictable molding process. Which in turn reduces the risk of defects and increases the overall yield.
- Improved Part Quality: With better control over the flow of material, the quality of molded parts is significantly improved. This is especially important for industries that require high-precision parts with minimal defects.
- Reduced Material Consumption: By optimizing the flow and reducing the risk of overpacking. These end rings help to minimize material waste, leading to cost savings for manufacturers.
- Lower Maintenance Costs: The durability of the new end rings reduces the frequency of repairs and replacements. Which making them a more cost-effective solution in the long run.
- Faster Cycle Times: With the improved flow and thermal regulation, manufacturers can expect shorter cycle times. Which enhances overall productivity and throughput.
How Oerlikon HRS Flow’s Valve Gate End Rings Improve Manufacturing Efficiency
Impact on Injection Molding Process
Oerlikon HRS Flow’s new valve gate end rings can significantly impact the efficiency of the injection molding process. The precise control offered by these end rings helps manufacturers streamline their operations by reducing scrap rates, improving cycle times, and ensuring that each part is produced to specification. This improved efficiency leads to reduced operational costs and greater profitability.
Customization for Specific Applications
Oerlikon HRS Flow’s valve gate end rings can be customized to meet the specific requirements of different injection molding applications. Whether for high-precision parts in medical devices or complex automotive components, the flexibility of the new end rings ensures that manufacturers can optimize their hot runner systems for their unique needs.
Environmental Impact and Sustainability
The new valve gate end rings also contribute to sustainability goals by reducing material waste and energy consumption. By improving the flow of molten plastic and reducing the need for regrinding scrap material. Which manufacturers can reduce their environmental footprint while improving overall production efficiency.
Conclusion
Oerlikon HRS Flow’s new valve gate end rings for nozzle series represent a significant leap forward in the evolution of hot runner systems for injection molding. By enhancing material flow, improving thermal performance, and increasing durability. These end rings provide manufacturers with the tools they need to optimize their injection molding processes. With benefits ranging from improved part quality and reduced material consumption to faster cycle times and lower maintenance costs. These innovations promise to drive operational efficiency and profitability across a range of industries.
As injection molding continues to evolve and demand for high-quality, high-precision parts increases. And the role of advanced technologies like valve gate systems will only continue to grow. Oerlikon HRS Flow’s new valve gate end rings are at the forefront of this transformation. Which offering manufacturers a solution that balances performance, reliability, and sustainability.
FAQs
1. What is a valve gates in injection molding?
A valve gate is a type of gate used in injection molding that controls the flow of molten plastic into the mold cavity. It opens and closes to regulate the amount of material injected, ensuring precise control over the molding process.
2. What are the benefits of using valve gates end rings in hot runner systems?
Valve gate end rings improve the flow of molten plastic, maintain consistent temperatures, reduce material waste, and improve part quality. They also offer greater durability and easier maintenance.
3. How do Oerlikon HRS Flow’s new valve gate end rings improve injection molding performance?
The new valve gate end rings optimize the flow path, enhance thermal performance, increase durability, and provide precise control over material injection, all of which lead to better part quality, faster cycle times, and lower maintenance costs.
4. Can these valve gate end rings be customized for specific applications?
Yes, Oerlikon HRS Flow offers customization options for their valve gate end rings to meet the specific requirements of different industries, such as automotive, medical devices, and consumer goods.
5. Are Oerlikon HRS Flow’s valve gate end rings environmentally friendly?
Yes, by improving the efficiency of the injection molding process, reducing material waste, and lowering energy consumption, the new valve gate end rings contribute to more sustainable manufacturing practices.