In an era of rapid technological advancement, industries worldwide are continuously seeking ways to innovate and improve manufacturing processes. For valve makers, precision, reliability, and cost-efficiency are essential to meet the demands of modern industries such as oil and gas, power generation, and water treatment. One of the most significant innovations in manufacturing today is the use of Additive Manufacturing (AM), particularly metal 3D printing, which has revolutionized the way components are designed and produced.
In this article, we will explore how Renishaw, a global leader in metal additive manufacturing, has partnered with valve maker Domin, supplying them with an advanced metal laser AM system. We’ll discuss how this technology is changing the valve manufacturing landscape, the benefits it brings to Domin and the broader valve industry, and what this means for the future of manufacturing in the valve sector.
What is Additive Manufacturing (AM) of Valve?
Additive manufacturing, commonly known as 3D printing, is a process in which a material is deposited layer by layer to create a three-dimensional object. Unlike traditional manufacturing methods that rely on subtracting material from a solid block (such as machining or casting). AM builds up the product by adding material, often using a laser or another energy source to fuse the material.
Metal additive manufacturing, or metal 3D printing, uses metal powders that are selectively melted and fused together to create parts with complex geometries and highly detailed designs. This technology has gained significant traction in industries that require precision-engineered components. Such as aerospace, automotive, and, of course, valve manufacturing.
Renishaw: A Leader in Metal Laser Valve AM Technology
Renishaw is an established name in the world of advanced manufacturing, known for its expertise in metrology, additive manufacturing, and engineering solutions. With a track record of producing high-quality metal additive manufacturing systems. Renishaw has been at the forefront of pushing the boundaries of what is possible with 3D printing technologies. Their systems enable manufacturers to create highly complex parts with exceptional precision and strength. Which using a variety of materials such as stainless steel, titanium, aluminum, and more.
The Benefits of Renishaw’s Metal AM Systems
Renishaw’s metal laser AM systems are equipped with the latest laser technology and precision control systems that allow manufacturers to produce parts with intricate designs and specifications. These systems offer several key benefits over traditional manufacturing methods, particularly for valve makers:
- Complex Geometries: Traditional manufacturing techniques can be limited by the complexity of the design. Additive manufacturing, however, allows valve makers to produce components with complex internal geometries. Such as channels, lattice structures, and internal cooling features that would be impossible or cost-prohibitive with conventional methods.
- Material Efficiency: Metal 3D printing reduces waste by using only the material required for the component. Which is particularly beneficial when working with expensive metals like titanium or stainless steel. Additionally, any unused material can often be reused for future prints, contributing to a more sustainable manufacturing process.
- Customization and Flexibility: With metal AM, valve makers like Domin can easily customize designs without the need for expensive tooling or molds. This is particularly valuable for producing low-volume, high-complexity components, or parts designed for specific customer requirements.
- Faster Prototyping and Production: Metal AM speeds up the design iteration process, allowing valve makers to rapidly prototype parts and test their designs before full-scale production. This not only reduces time to market but also lowers the risk of costly mistakes in mass production.
- Improved Performance: The ability to produce lightweight, high-strength parts with intricate geometries means that valves made through additive manufacturing can offer enhanced performance. For instance, valves used in extreme environments, such as high-pressure systems or chemical processing, can be designed to handle specific stresses and strains more efficiently.
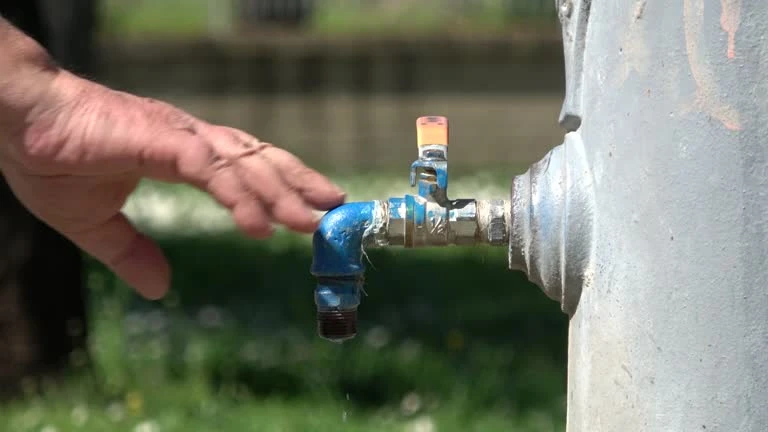
Domin: A Valve Maker Leading the Way in Innovation
Domin, a well-established valve maker, has a reputation for producing high-quality, precision-engineered valves for a variety of industries, including oil and gas, water treatment, and power generation. As industries continue to demand higher performance and more complex designs, Domin has sought to stay at the cutting edge of manufacturing technology.
By partnering with Renishaw and integrating metal laser additive manufacturing into their production processes, Domin has taken a significant step forward in enhancing its product offerings and increasing production efficiency. The collaboration is expected to help Domin streamline its manufacturing capabilities, reduce lead times, and enhance the customization of valve components for its clients.
How Metal Laser AM Benefits Domin
For Domin, Renishaw’s metal laser AM system provides several advantages, particularly when it comes to producing highly specialized valve components. Here are some of the key benefits Domin expects to see:
- Faster Design and Prototyping: With the ability to rapidly prototype valve components, Domin can test and refine new designs more efficiently. This not only reduces the time it takes to bring new products to market but also enables quicker responses to customer-specific demands.
- Cost-Effective Production: By reducing material waste and eliminating the need for expensive tooling and molds, Domin can lower the cost of production for small and medium-sized batches of valves. This is especially useful for custom-made or one-off valve components that would otherwise be too costly to produce using traditional methods.
- Increased Design Flexibility: Metal laser AM allows Domin to experiment with more complex valve designs that include intricate internal geometries, such as cooling channels or lightweight structures. This design flexibility enhances the functionality and performance of the final valve product, especially in high-performance applications.
- Enhanced Supply Chain Efficiency: With additive manufacturing, Domin can produce valve components on demand. Which reducing the need for large inventories and long lead times. This helps streamline the supply chain and ensures that valve parts are readily available when needed, without unnecessary delays.
- Improved Product Quality: The precision and control offered by Renishaw’s metal AM systems enable Domin to produce valve components with exceptional consistency and quality. The result is more reliable products with fewer defects, which is critical for industries where safety and performance are paramount.
Metal Additive Manufacturing’s Impact on the Valve Industry
The collaboration between Renishaw and Domin highlights the growing role of metal additive manufacturing in the valve industry. As industries become more demanding in terms of performance, customization, and cost-efficiency. Valve makers are increasingly turning to 3D printing to meet these needs. Here’s how metal AM is transforming the valve industry:
1. Customization for Specific Applications
Valves are used in a wide range of industries, each with unique requirements. Metal AM allows valve makers to produce components that are tailored to the specific needs of each application. Whether it’s creating valves with specialized materials for extreme temperatures, complex geometries for efficient flow, or custom designs for unique system requirements, metal additive manufacturing provides the flexibility needed to meet these challenges.
2. Smaller Batch Production
Many industries require valves in small quantities, particularly when dealing with specialized or custom-built systems. Traditional manufacturing methods can be inefficient for small runs, requiring expensive molds and tooling. Metal AM allows valve makers to produce smaller batches more cost-effectively, reducing waste and lead time.
3. Lightweight and Stronger Components
Additive manufacturing enables the creation of lightweight yet strong valve components that are essential for reducing energy consumption and enhancing performance, especially in aerospace, automotive, and oil and gas applications. The ability to create complex geometries. Such as lattice structures or integrated cooling channels, can help improve the efficiency and strength of valve components.
4. Faster Time to Valve Market
In industries where time is of the essence, additive manufacturing speeds up the design, prototyping, and production processes. Valve makers can quickly develop and test new valve designs, ensuring that they meet the stringent requirements of their clients and reducing the overall time to market for new products.
Conclusion
The partnership between Renishaw and Domin represents a major leap forward for the valve manufacturing industry. By integrating Renishaw’s metal laser additive manufacturing systems into their production lines. Domin is setting a new standard for innovation, efficiency, and customization in the valve sector. This technology is helping Domin enhance the quality and performance of its products while reducing production costs and lead times. As more valve makers adopt additive manufacturing. We can expect to see continued advancements in valve design, customization, and overall industry performance.
Frequently Asked Questions (FAQ)
1. What is metal laser additive manufacturing?
Metal laser additive manufacturing (AM) is a 3D printing process that uses a laser to melt metal powder layer by layer. Which building up complex components with high precision. This method is ideal for producing parts with intricate geometries and high-performance requirements.
2. How does additive manufacturing benefit valve makers?
Additive manufacturing enables valve makers to produce highly customized and complex valve components that are difficult or impossible to create using traditional methods. It reduces material waste, speeds up prototyping, and enhances the performance of valve products.
3. What industries benefit most from metal AM for valve production?
Industries that require high-performance valves, such as oil and gas, power generation, aerospace, and water treatment, benefit the most from metal AM. The technology allows valve makers to produce valves with custom designs and specifications tailored to specific industry needs.
4. How does metal AM reduce production costs?
Metal AM reduces production costs by eliminating the need for expensive tooling and molds. Which reducing material waste, and allowing for on-demand production. This makes it particularly cost-effective for small or custom production runs.
5. Will Renishaw’s metal AM system replace traditional valve manufacturing methods?
While metal AM offers significant advantages, it is not expected to fully replace traditional methods. Instead, it complements traditional manufacturing, enabling valve makers to create complex, customized components more efficiently and cost-effectively.