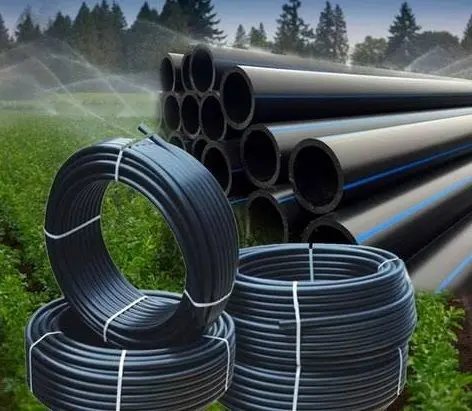
The production of PE pipes involves a highly specialized process that adheres to strict quality standards. In this article, we’ll explore the entire PE pipe production line, including the processes involved, the benefits of PE pipes, and the future of PE pipe manufacturing.
What is PE Pipe?
Overview of PE Pipe
PE pipe is made from polyethylene, a thermoplastic polymer that has become a material of choice for water supply, gas distribution, and sewage systems. PE pipes are available in different grades and sizes, making them suitable for various applications.
Key Properties of PE Pipe
- Corrosion Resistance: PE pipes do not corrode, which makes them ideal for transporting liquids without fear of rust or chemical degradation.
- Flexibility: The flexibility of PE pipes allows for easy installation and adaptability to various environments and terrains.
- Low Friction Loss: The smooth inner surface of PE pipes minimizes friction loss, enhancing flow efficiency.
The PE Pipe Production Process
The production of PE pipes involves several key steps, from raw material preparation to quality control. Below, we’ll detail each stage of the production line.
1. Raw Material Selection
The first step in the production of PE pipes is selecting high-quality polyethylene resin.
2. Extrusion Process
The extrusion process is the core of the PE pipe production line. Here’s a breakdown of how this process works:
Feeding the Material
Polyethylene pellets are fed into an extruder, where they are heated to a specific temperature to melt the material.
Forming the Pipe
The molten polyethylene is forced through a specially designed die that shapes it into a continuous pipe. This die determines the final diameter and wall thickness of the pipe.
Cooling the Pipe
After extrusion, the newly formed PE pipe is cooled using water or air cooling methods. Cooling is essential to solidify the pipe and maintain its shape.
3. Calibration and Sizing
This step ensures that the pipe meets the specified dimensions:
- Vacuum Tanks: Sometimes used to ensure that the pipe maintains the correct size and shape.
4. Cutting and Packaging
After calibration, the continuous length of PE pipe is cut into specified lengths. This step often includes:
- Automated Cutting Machines: For precision and efficiency.
Hydrostatic Testing
Pipes are tested under pressure to ensure they can withstand operational conditions without leaks.
Impact Testing
This testing assesses the pipe’s resistance to impact and ensures that it can endure physical stress.
Benefits of Using PE Pipes
1. Durability and Longevity
PE pipes are known for their long service life, often exceeding 50 years. Their resistance to corrosion and chemical degradation means they require less frequent replacement.
2. Low Maintenance Costs
They do not need protective coatings or treatments like metal pipes, which reduces long-term costs.
4. Versatility in Applications
- Water Supply: For municipal and residential water distribution.
- Gas Distribution: For transporting natural gas safely and efficiently.
- Irrigation: Widely used in agricultural applications for efficient water delivery.
Challenges in PE Pipe Production
1. Material Quality Control
Ensuring consistent quality in raw materials is critical. Variations in the quality of polyethylene can affect the final product’s performance.
3. Technological Advances
Keeping up with technological advancements is essential for maintaining competitiveness. Manufacturers need to invest in the latest equipment and processes to enhance efficiency and quality.
Future Trends in PE Pipe Production
2. Sustainable Practices
As the focus on sustainability increases, manufacturers will likely adopt more eco-friendly materials and production methods to reduce their environmental impact.
3. Increased Demand for PE Pipes
This trend will drive innovation and improvements in manufacturing processes.
Conclusion
The PE pipe production line is a complex yet efficient process that ensures the production of high-quality polyethylene pipes for various applications. By understanding the production steps, benefits, and future trends associated with PE pipes, stakeholders can make informed decisions that enhance the reliability and efficiency of their piping systems. As the industry evolves, continued investment in technology and sustainability will be key to meeting the increasing demands for PE pipe solutions.
FAQs
1. What are the main advantages of PE pipes?
PE pipes offer corrosion resistance, flexibility, lightweight construction, and low maintenance costs.
5. Are PE pipes environmentally friendly?
Yes, PE pipes are recyclable, and many manufacturers implement eco-friendly practices to minimize their environmental impact.