The Vogtle Electric Generating Plant, one of the most significant nuclear facilities in the United States, has successfully brought Unit 3 back online following a recent valve issue. The incident temporarily halted operations, but swift action by the team ensured a quick and efficient resolution.
In this article, we’ll delve into what caused the valve issue, how the team resolved it, and the broader implications for nuclear energy operations.
Overview of Vogtle Unit 3
Vogtle Unit 3 is part of the Vogtle Electric Generating Plant in Georgia, the first newly constructed nuclear reactor in the U.S. in decades. This advanced nuclear unit represents a key component of America’s clean energy strategy, with the potential to power over 500,000 homes with zero-emission electricity.
Key Features of Vogtle Unit 3:
- Type: AP1000 Pressurized Water Reactor
- Capacity: Approximately 1,117 MW
- Technology: Passive safety features for enhanced reliability
Understanding the Valve Issue
Valve-related problems are not uncommon in industrial and power-generation settings, including nuclear plants. In this instance, the valve issue involved a critical component that regulates the flow of coolant within the reactor system.
Potential Causes of Valve Issues:
- Wear and Tear: Over time, mechanical components can degrade.
- Material Fatigue: High-pressure environments can weaken certain materials.
- Operational Errors: Miscalibrations or improper settings may lead to malfunctions.
- Debris or Blockages: Foreign particles can obstruct valve operations.
For Vogtle Unit 3, the issue necessitated an immediate halt to operations to prevent any compromise in safety or performance.
Duet Tool Box: Compact and Practical
Alongside the valve caps, Granite Design’s Duet Tool Box offers a versatile solution for cyclists who value preparedness.
Features of the Duet Tool Box:
- All-in-One Compact Storage: Fits multiple essential tools in a compact casing.
- Secure Mounting System: Attaches neatly under the saddle or to the frame for easy access.
- Tool Variety: Includes hex wrenches, tire levers, and other essentials for quick repairs.
- Durability: Built with robust materials to withstand outdoor conditions.
The Duet Tool Box complements the Juicy Nipple Valve Caps, ensuring cyclists are equip for any situation.
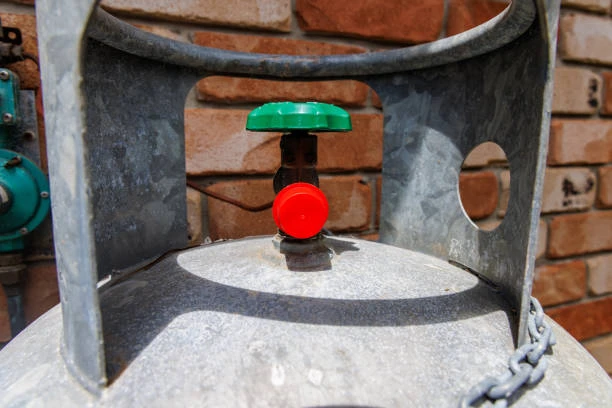
How Was the Valve Issue Resolved?
The response to the valve issue highlighted the plant’s commitment to safety and efficiency. Below is a summary of the steps taken:
1. Rapid Diagnostics
Engineers conducted a thorough diagnostic process to identify the specific valve causing the problem. Advanced monitoring systems played a critical role in pinpointing the fault.
2. Component Inspection
The affected valve was isolated, disassembled, and inspect for signs of wear, damage, or debris. This process revealed a minor defect in the valve’s actuator.
3. Repairs and Replacements
Technicians replaced the faulty actuator with a new, high-performance component. The valve was also recalibrate to ensure optimal performance.
4. Testing and Validation
After repairs, the team tested the valve under simulated operating conditions to verify its reliability. Once validated, the reactor system was carefully restart.
5. Post-Incident Review
A comprehensive review was conduct to identify lessons learn and implement measures to prevent similar issues in the future.
Implications for Nuclear Energy
The quick resolution of the valve issue at Vogtle Unit 3 underscores the robustness of modern nuclear safety protocols. It also highlights the importance of regular maintenance and monitoring in high-stakes energy environments.
Key Takeaways:
- Operational Resilience: Advanced diagnostic tools and skilled technicians minimize downtime.
- Commitment to Safety: Safety remains the top priority, with stringent protocols ensuring no compromises.
- Ongoing Innovation: Incidents like this drive further technological advancements in valve design and system monitoring.
Preventing Future Valve Issues in Nuclear Plants
To mitigate the risk of valve-related problems, nuclear plants must implement proactive measures, including:
- Routine Maintenance: Regular inspections and servicing of valves to identify wear and potential issues early.
- Upgraded Materials: Use advanced materials that withstand high pressure and temperature conditions.
- Real-Time Monitoring: Install sensors to detect anomalies in valve performance.
- Staff Training: Ensure operators and technicians are well-train in handling and maintaining critical components.
- Vendor Partnerships: Collaborate with trusted manufacturers for high-quality valve components.
Conclusion
The successful return of Vogtle Unit 3 to operational status after addressing the valve issue demonstrates the effectiveness of modern nuclear plant protocols. The incident, while brief, serves as a reminder of the intricate systems at work in power generation and the importance of maintaining their reliability.
As the plant resumes its role in providing clean energy to thousands of homes, it reaffirms the resilience and potential of nuclear energy in achieving a sustainable future. With continuous improvements in technology and safety practices, the industry is well-position to address challenges and power the world efficiently and safely.
FAQs About Valve Issues in Power Plants
1. What causes valve issues in nuclear power plants?
Valve issues often result from wear and tear, material fatigue, debris, or miscalibrations within the system.
2. How are valve issues detected?
Advanced monitoring systems and routine inspections help detect irregularities in valve performance.
3. Can valve issues compromise reactor safety?
Modern reactors have multiple safeguards to ensure that valve issues do not compromise overall safety. Quick diagnostics and repairs mitigate risks.
4. How long does it take to resolve a valve issue?
Resolution times vary depending on the complexity of the problem but typically involve diagnostics, repairs, and thorough testing.
5. What steps are taken to prevent valve issues?
Preventive measures include routine maintenance, material upgrades, real-time monitoring, and continuous staff training.