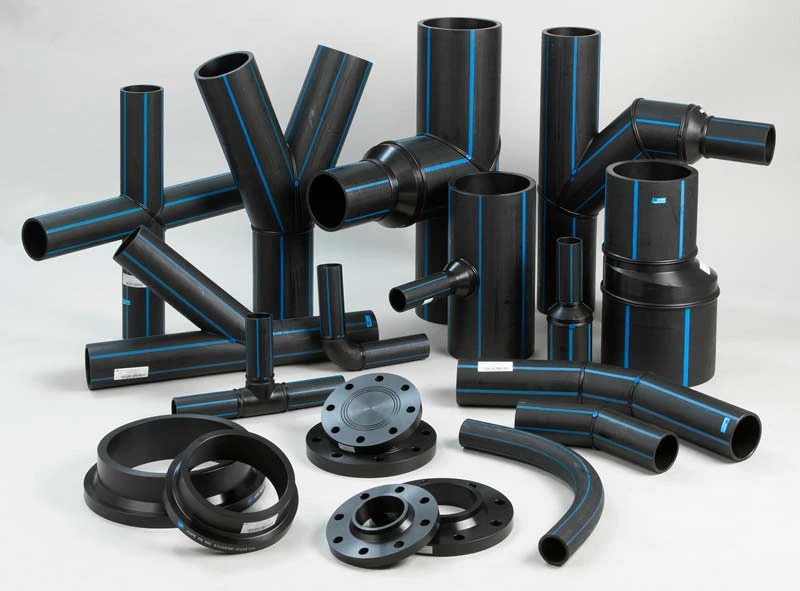
Key Features of HDPE Pipes
- Corrosion Resistance: HDPE Pipe and Fittings are resistant to rust, corrosion, and chemical damage, which prolongs their lifespan.
- Flexibility: The material can bend without breaking, allowing for easier installation in challenging terrains.
- Low Friction Coefficient: This results in reduced flow resistance, which can enhance the efficiency of fluid transport.
- Lightweight: HDPE pipes are much lighter than traditional materials, making them easier to handle and install.
Advantages of Using HDPE Pipes and Fittings
- Durability: With a lifespan of 50 years or more, HDPE Pipe and Fittings require minimal maintenance and replacements.
- Cost-Effective: While the initial investment may be higher, the long-term savings on maintenance and replacement costs make HDPE a cost-effective choice.
- Environmental Impact: HDPE is recyclable, contributing to sustainability efforts in construction and plumbing.
- Resistance to Infiltration and Exfiltration: The sealed joints prevent leaks and maintain system integrity.
Applications of HDPE Pipes and Fittings
- Water Supply Systems: Ideal for drinking water and irrigation applications.
- Sewage and Drainage Systems: Used in waste management and stormwater drainage.
- Gas Distribution: Suitable for transporting natural gas and propane.
- Mining and Industrial Uses: Employed for transferring slurries, chemicals, and other industrial fluids.
Installation Process for HDPE Pipes and Fittings
1. Planning and Preparation
- Design the Layout: Before installation, plan the piping layout, considering the purpose and environmental factors.
- Gather Tools and Materials: Ensure you have all necessary tools, including fusion machines, pipe cutters, and safety gear.
2. Cutting the Pipes
- Measure and Cut: Use a measuring tape to determine the lengths needed. Cut the HDPE pipes with a pipe cutter for clean edges.
3. Preparing the Fittings
- Inspect Fittings: Check that all fabricated fittings are free from damage and compatible with the pipes.
- Clean Surfaces: Ensure the joining surfaces are clean for effective fusion.
4. Joining Methods
- Butt Fusion: This method involves heating the ends of the pipes and fittings to a specific temperature, then pressing them together to form a strong joint.
- Electrofusion: When electrical current passes through, it melts the fitting and pipe ends to create a secure connection.
5. Testing the System
- Conduct Pressure Tests: After installation, conduct pressure tests to ensure there are no leaks and that the system can handle the required pressure.
6. Finalizing the Installation
- Secure Pipes: Use supports and brackets to secure the pipes, preventing movement that could cause stress on joints.
Conclusion
HDPE pipes and fabricated fittings are reliable solutions for various piping needs. With their durability, flexibility, and cost-effectiveness, they provide significant advantages in many applications, from water distribution to industrial processes. Understanding their features and installation methods can help ensure a successful and efficient piping system.
FAQs
What is the lifespan of HDPE pipes?
HDPE pipes can last over 50 years with proper installation and maintenance.
How do I know if my HDPE pipes are leaking?
Regular inspections and pressure testing can help identify leaks in the system.
Is HDPE recyclable?
Yes, HDPE is fully recyclable, making it an environmentally friendly option for piping solutions.