Introduction
A PPR (Polypropylene Random Copolymer) pipe GB/T 18742 making machine a specialized piece of equipment designed for the continuous production of PPR pipes through the extrusion process. These machines play a crucial role in the manufacturing of high-quality pipes used in plumbing, construction, and industrial applications. This article provides an overview of the components, working principles, and advantages of PPR pipe making machines.
Key Components of a PPR Pipe Making Machine
- Extruder
- The extruder is the core component of the machine, responsible for melting and homogenizing PPR granules. It consists of a screw mechanism that conveys the raw material through a heated barrel. where melted before being pushed through the die.
- Die Head
- The die head shapes the molten PPR material into the desired pipe dimensions. The design of the die is critical for achieving uniform wall thickness and smooth finishes on the pipes.
Calibration System
- After the pipe exits the die, it passes through a calibration system that shapes and cools the pipe to ensure it meets specified dimensions. This system may include water baths or vacuum calibration units.
- Cooling System
- A cooling system, typically consisting of a water tank or air-cooling devices, is used to rapidly cool the extruded pipe, solidifying the material and maintaining its shape.
- Pulling Unit
- The pulling unit consists of caterpillar belts or rollers that transport the cooled pipe along the production line at a controlled speed, ensuring consistent tension and preventing deformation.
Cutting Machine
- Once the pipe has been pulled to the desired length, the cutting machine slices it into predetermined lengths. This unit can be equipped with automatic features to enhance production efficiency.
- Control Panel
- An integrated control panel allows operators to monitor and adjust various parameters of the production process, such as temperature, speed, and pressure. Advanced systems may include automation for improved efficiency.
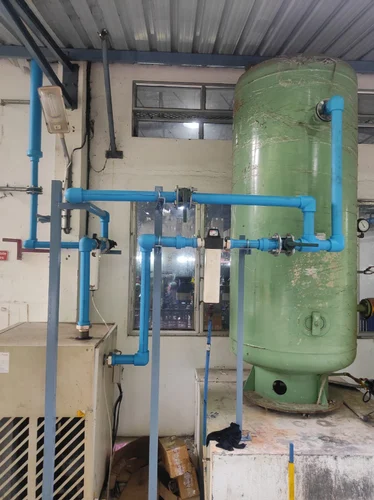
Working Principles of a PPR Pipe Making Machine
- Material Feeding
- PPR granules loaded into the hopper of the extruder. The material often pre-dried to eliminate moisture that could affect the extrusion process.
- Melting and Mixing
- The screw within the extruder rotates, conveying the PPR granules through the heated barrel. As the material is heated, it melts and mixed thoroughly to achieve a uniform consistency.
Extrusion Process
- The molten PPR forced through the die head, where it takes on the shape of the desired pipe. The diameter and wall thickness are determined by the design of the die.
- Calibration and Cooling
- The extruded pipe then calibrated and cooled using the calibration system and cooling devices. This step ensures that the pipe maintains its dimensions and structural integrity as it solidifies.
Pulling and Cutting
- The cooled pipe pulled along the line by the pulling unit. Once it reaches the required length, the cutting machine slices it into individual sections.
- Quality Control
- Finished pipes undergo quality control checks to ensure they meet industry standards regarding dimensions, weight, and overall quality.
Advantages of PPR Pipe Making Machines
- High Production Efficiency
- PPR pipe making machines can operate continuously, allowing for high output rates and efficient production processes.
Consistent Quality
- The controlled environment of the extrusion process ensures uniformity in pipe dimensions and properties, resulting in high-quality products.
- Versatility
- These machines easily adjusted to produce pipes of various sizes and specifications, catering to diverse market needs.
Cost-Effectiveness
- The efficiency of the production process reduces material waste and labor costs, making it an economically viable option for manufacturers.
- Automation Potential
- Modern machines equipped with automation features, reducing labor requirements and minimizing the risk of human error during production.
Applications
- Residential Plumbing: PPR pipes produced by these machines are ideal for hot and cold water supply in homes.
- Commercial Buildings: Suitable for plumbing systems in offices, hotels, and other commercial properties.
- Industrial Use: Can produce pipes for applications in chemical processing, food and beverage industries, and irrigation systems.
- Infrastructure Projects: Essential for large-scale municipal water supply and sewage systems.
Conclusion
A PPR pipe making machine is an essential investment for manufacturers looking to produce high-quality PPR pipes efficiently. With advanced technology and precise control, these machines enable the mass production of durable and reliable piping solutions suitable for a variety of applications. As the demand for PPR pipes continues to grow, investing in a PPR pipe making machine can significantly enhance a manufacturer’s competitiveness in the market.