Introduction
When selecting piping materials for plumbing, irrigation, or industrial applications, the debate often comes down to HDPE pipes (High-Density Polyethylene) versus traditional options like metal, concrete, or PVC. HDPE pipe offer superior durability, flexibility, and cost-efficiency, making them a preferred choice in modern construction and infrastructure projects.
In this article, we explore the key differences between HDPE pipe and traditional piping systems, highlighting why HDPE stands out as the better option for many applications.
What Are HDPE Pipe?
HDPE pipes are plastic pipes made from high-density polyethylene, a strong and flexible thermoplastic. Manufacturers widely use them for water supply, gas distribution, sewage systems, and industrial applications due to their:
- Corrosion resistance
- Leak-proof joints (fused, not glued)
- Long lifespan (50+ years)
- Lightweight yet durable structure
Unlike traditional pipes, HDPE pipes resist chemical reactions, abrasion, and environmental stress, making them ideal for harsh conditions.
HDPE Pipe vs. Traditional Pipe: Key Differences
1. Material Durability
- HDPE Pipes: Resistant to rust, corrosion, and chemical damage. They withstand extreme temperatures (-40°C to 60°C).
- Traditional Pipes (Metal/Concrete): Prone to rust (iron), scaling (steel), and cracking (concrete). Require frequent maintenance.
2. Installation & Flexibility
- HDPE Pipes: Lightweight and flexible, allowing trenchless installation (minimal digging). Heat-fused joints eliminate leaks.
- Traditional Pipes: Heavy and rigid, requiring more labor and support structures. Threaded or welded joints may fail over time.
3. Cost Efficiency
- HDPE Pipes: Lower installation costs due to lightweight handling and fewer fittings. Long-term savings with minimal repairs.
- Traditional Pipes: Higher initial costs (material + labor). Frequent repairs increase expenses.
4. Environmental Impact
- HDPE Pipes: Recyclable, non-toxic, and energy-efficient to produce. Reduce water contamination risks.
- Traditional Pipes: Mining and manufacturing metal/concrete pipes consume more energy and generate waste.
5. Lifespan & Maintenance
- HDPE Pipes: Last 50+ years with minimal upkeep. No internal scaling reduces flow restrictions.
- Traditional Pipes: Degrade faster (20-30 years for metal, 30-50 for concrete). Scaling and corrosion reduce efficiency.
Why Choose HDPE Pipe?
- Leak-Free System – Heat-fused joints prevent leaks, unlike glued or threaded connections.
- Chemical & UV Resistant – Ideal for industrial and outdoor use.
- Earthquake-Resistant – Flexible material bends without breaking under pressure.
- Lower Total Cost – Saves money on installation, maintenance, and replacements.
- Eco-Friendly – Made from recyclable materials, reducing environmental impact.
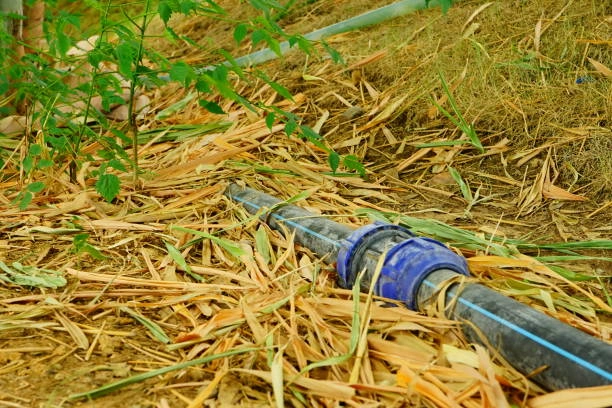
Applications of HDPE Pipe
- Water Supply & Distribution (municipal & agricultural)
- Sewage & Drainage Systems (corrosion-resistant)
- Gas & Oil Pipelines (safe, leak-proof transport)
- Mining & Industrial Use (handles abrasive materials)
- Trenchless Technology (minimal ground disruption)
Conclusion
When comparing HDPE pipes to traditional piping systems, HDPE clearly offers better durability, cost savings, and environmental benefits. Its resistance to corrosion, flexibility, and long lifespan make it the top choice for modern infrastructure projects.
Whether for residential plumbing, large-scale irrigation, or industrial applications, HDPE pipes provide a reliable and sustainable solution.
FAQs About HDPE Pipe
1. Are HDPE pipe safe for drinking water?
Yes, HDPE pipes meet international safety standards (NSF, ISO) and do not leach harmful chemicals.
2. Can HDPE pipe handle high pressure?
Yes, especially PE 100 HDPE pipes, which withstand high-pressure applications like gas and water mains.
3. How long do HDPE pipe last?
Properly installed HDPE pipes last 50+ years, even in harsh environments.
4. Are HDPE pipe recyclable?
Yes, manufacturers can recycle HDPE material to produce new pipes or other plastic products.
5. Can I install HDPE pipe myself?
While possible, professional installation ensures proper fusion welding for leak-free joints.