Electrofusion welding is a widely adopted method for joining HDPE pipe fittings due to its reliability, efficiency, and ability to create leak-proof connections. However, improper installation can compromise system integrity, leading to leaks, reduced lifespan, or even catastrophic failures. This guide outlines best practices for safely and correctly installing HDPE pipe fittings using electrofusion techniques.
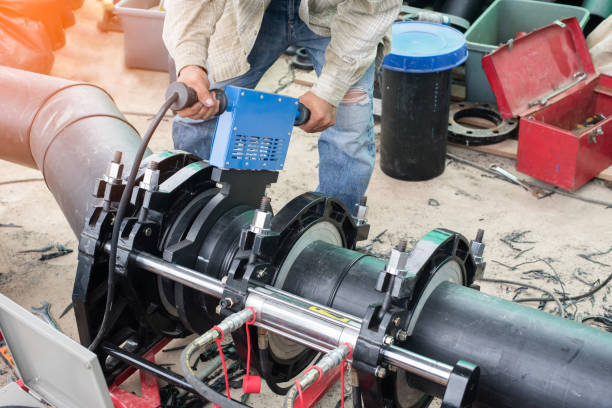
1. Pre-Installation Preparations
Before initiating electrofusion welding, ensure all materials and tools are in optimal condition. Inspect HDPE pipe and fittings for defects such as cracks, scratches, or contamination. Clean the ends of pipes and fittings thoroughly using a lint-free cloth to remove dirt, moisture, or oxidation layers. Use only electrofusion fittings designed for the specific HDPE material grade (e.g., PE100) and SDR rating to ensure compatibility.
2. Equipment Selection and Calibration
Use electrofusion welding machines certified for HDPE applications, adhering to standards like ISO 12176-3. Regularly calibrate welding machines to maintain accurate temperature and time settings. Verify the machine’s compatibility with the fittings’ resistance coils and ensure proper electrode connections. Mismatched equipment can lead to incomplete welds or material degradation.
3. Marking and Alignment
Mark the insertion depth on the pipe using a permanent marker, referencing the fitting’s specified engagement length. Misalignment during insertion can cause uneven heating or incomplete fusion. Use reusable alignment clamps to hold pipes and fittings in place, preventing movement during welding. Ensure the fitting’s internal coil is centered and free from obstructions.
4. Welding Process Execution
Secure the fitting onto the pipe, ensuring full insertion to the marked depth. Activate the welding machine, which will automatically heat the coil embedded in the fitting. Avoid interruptions during the welding cycle, as premature termination can result in weak joints. Monitor the machine’s display for error codes or irregularities. For larger fittings (e.g., DN315 and above), some manufacturers recommend preheating the pipe end to improve fusion quality.
5. Cooling and Post-Weld Inspection
After welding, allow the joint to cool naturally without applying external force or water. Rapid cooling can cause thermal stress and weaken the bond. Once cooled, visually inspect the weld bead for uniformity, absence of voids, and proper fusion. Use a go/no-go gauge to verify the bead’s width meets the fitting manufacturer’s specifications. Non-destructive testing (e.g., ultrasonic or radiographic methods) may be required for critical applications.
6. Handling and Storage of Electrofusion Fittings
Store electrofusion fittings in a dry, cool environment away from direct sunlight and UV exposure. UV degradation can compromise the fitting’s integrity. Avoid bending or dropping fittings, as this may damage internal coils. Keep fittings in their original packaging until use to prevent contamination.
7. Training and Certification
Only trained and certified personnel should perform electrofusion welding. Operators must understand the principles of heat transfer, material behavior, and welding parameters. Regular refresher training and competency assessments ensure adherence to industry standards (e.g., DVGW GW 335-A, ASTM F2620).
8. Documentation and Traceability
Maintain detailed records of welding parameters, operator details, and inspection results for each joint. Use barcode scanning or RFID tags to track fittings from production to installation. This traceability is crucial for quality assurance and future maintenance.
FAQ
Q1: Can electrofusion be used for all HDPE pipe sizes?
A1: Electrofusion is suitable for pipes ranging from DN20 to DN710mm. For larger diameters, butt fusion is typically preferred due to equipment limitations.
Q2: What is the minimum ambient temperature for electrofusion welding?
A2: Most manufacturers recommend a minimum ambient temperature of 5°C (41°F). Colder temperatures may require preheating the pipe or using insulated welding machines.
Q3: How long does an electrofusion weld take?
A3: Welding times vary by fitting size and material grade but typically range from 10 seconds (for DN20) to 1200 seconds (for DN710). Always follow the fitting manufacturer’s guidelines.
Q4: Can electrofusion fittings be reused?
A4: No. Electrofusion fittings are single-use components. Reusing them can lead to catastrophic failures.
Q5: What is the service life of an electrofusion joint?
A5: When installed correctly, electrofusion joints have a lifespan comparable to the pipe itself—typically 50+ years under normal operating conditions.
By following these guidelines, installers can ensure the safety, reliability, and longevity of HDPE piping systems joined via electrofusion.