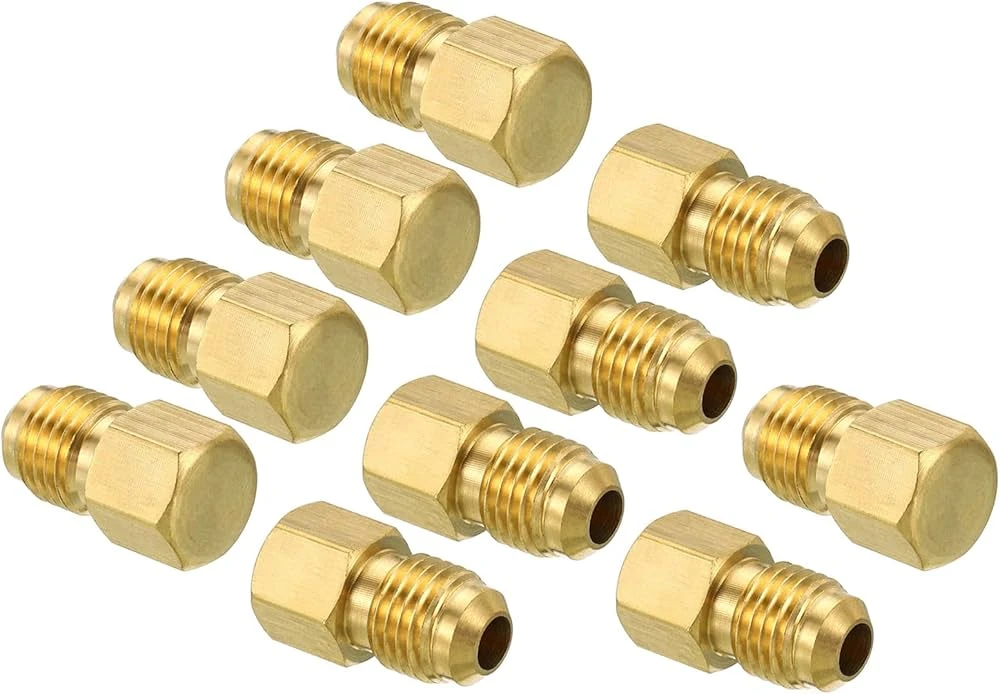
Introduction
Brass fittings play a vital role in compressed air piping systems, providing reliable connections and ensuring optimal performance. Known for their durability and resistance to corrosion, brass fittings are an ideal choice for various applications in industrial and commercial settings. This guide explores the features, benefits, and types of those suitable for compressed air systems.
Key Features of Brass Fittings for Compressed Air
- High-Quality Brass Material
Made from premium brass fittings offer excellent strength and resistance to wear, making them suitable for high-pressure environments. - Corrosion Resistance
Brass is inherently resistant to corrosion, which is crucial in compressed air systems where moisture and other contaminants may be present. - Variety of Connection Types
They come in various configurations, including threaded, barbed, and quick-connect options, allowing for versatile installation.
Benefits of Using Brass Fittings
- Durability: They are designed to withstand the demands of compressed air systems, ensuring long-lasting performance.
- Leak Prevention: The precision manufacturing of it helps to create tight seals, minimizing the risk of leaks and maintaining system efficiency.
- Ease of Installation: Many feature user-friendly designs that facilitate quick and straightforward installation, reducing downtime.
Types of Brass Fittings for Compressed Air Systems
- Elbows: Used to change the direction of piping, making it easier to navigate tight spaces.
- Tees: Allow for branching off to additional piping, enabling multiple air supply lines.
- Couplings: Connect two sections of pipe or tubing, ensuring a secure and reliable joint.
- Adapters: Facilitate connections between different pipe sizes or types, enhancing versatility in system design.
- Quick-Connect Fittings: Enable fast and easy disconnection of hoses, improving workflow efficiency.
Installation Tips
- Select the Right Size: Ensure that the fittings match the size of your piping system to maintain optimal flow and pressure.
- Use Thread Sealant: For threaded connections, apply appropriate thread sealant or tape to prevent leaks.
- Tighten Connections Properly: Avoid over-tightening, which can damage the fittings, but ensure they are securely fastened.
- Regular Inspections: Periodically check fittings for signs of wear or leaks to maintain system integrity.
Conclusion
That are an excellent choice for compressed air piping systems, offering durability, corrosion resistance, and reliable performance. By understanding the various types and features of these fittings, you can make informed decisions for your compressed air applications.
FAQs
1. Why choose these for compressed air systems?
It provide excellent strength, corrosion resistance, and leak prevention, making them ideal for high-pressure applications.
2. What types of brass fittings are best for compressed air?
Common types include elbows, tees, couplings, and quick-connect fittings, depending on your specific needs.
3. How do I install brass fittings properly?
Select the right size, use thread sealant, tighten securely without over-tightening, and regularly inspect for leaks.
5. How often should I inspect my brass fittings?
Regular inspections every few months are recommended to ensure they are functioning correctly and to catch any issues early.