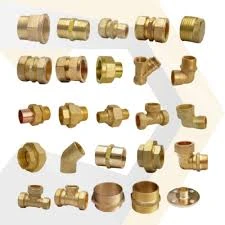
Brass fittings are an essential component in a wide range of industrial, plumbing, and manufacturing applications due to their unique combination of properties such as durability, corrosion resistance, and ease of installation. In this comprehensive guide, we’ll explore the key factors to consider when choosing the best brass fittings for your specific applications.
1. Understanding Brass Composition
Brass is an alloy primarily composed of copper and zinc, with other metals like lead, tin, or aluminum sometimes added to enhance specific properties. The percentage of zinc in the alloy determines the type of brass and its properties. For example, red brass (also known as cartridge brass) contains a higher percentage of copper and is known for its strength and corrosion resistance, making it ideal for high-pressure applications. On the other hand, yellow brass has a higher zinc content, offering good machinability but slightly less corrosion resistance.
2. Assessing Your Application Requirements
Before selecting brass fittings, thoroughly assess your application’s requirements. Consider factors such as:
- Pressure and Temperature: High-pressure or high-temperature applications require stronger and more heat-resistant brass fittings.
- Media Compatibility: Ensure the brass fittings are compatible with the fluid or gas they will be carrying. For instance, some brass alloys may not be suitable for use with certain chemicals or acids.
- Size and Connection Type: Determine the required size and connection type (e.g., threaded, solder, or compression fittings) based on your system’s specifications.
- Regulatory Compliance: Ensure the brass fittings meet any relevant industry standards or regulatory requirements.
3. Types of Brass Fittings
Brass fittings come in various shapes and sizes, each designed for specific purposes. Common types include:
- Elbows: Used to change the direction of flow in a pipe system.
- Couplings: Connect two pipes of the same diameter.
- Tees: Allow fluid to flow in two directions while branching off into a third.
- Unions: Provide a convenient way to disconnect and reconnect sections of pipe without the need to cut or solder.
- Caps and Plugs: Seal the end of a pipe, preventing fluid flow.
- Ball Valves: Control the flow of fluid or gas through a pipe by rotating a ball with a hole in it.
4. Choosing High-Quality Brass Fittings
When selecting brass fittings, look for manufacturers that offer high-quality products. Key indicators of quality include:
- Material Certification: Ensure the fittings are made from certified brass alloy that meets your application’s requirements.
- Manufacturing Standards: Look for fittings that comply with industry standards such as ASME, ANSI, or DIN.
- Finishing: A well-finished fitting indicates attention to detail and can help resist corrosion.
- Warranty: A manufacturer’s warranty provides peace of mind and can indicate confidence in the product’s quality.
5. Cost-Effectiveness
While cost is an important consideration, it should not be the sole deciding factor when selecting it. Cheaper options may compromise quality and durability, leading to higher maintenance costs or even system failures in the long run. Instead, focus on finding the best value for your money by balancing cost with quality and performance.
6. Conclusion
Choosing the best these for your applications requires careful consideration of your specific requirements, the properties of the brass alloy, and the quality of the fittings. By assessing your needs, understanding the types of fittings available, and selecting high-quality products from reputable manufacturers, you can ensure the integrity and efficiency of your systems. Remember, investing in quality it is a wise decision that will pay off in the long run through reduced maintenance costs and improved system performance.