Ground source geothermal systems, also known as ground-coupled heat pumps (GCHPs), are gaining traction as a sustainable energy solution for heating and cooling buildings. High-Density Polyethylene (HDPE) pipe fittings have emerged as a critical component in these systems, offering durability, corrosion resistance, and efficiency. Recent technological advancements in HDPE fittings are further enhancing their performance in geothermal applications, ensuring reliable heat exchange and long-term system longevity.
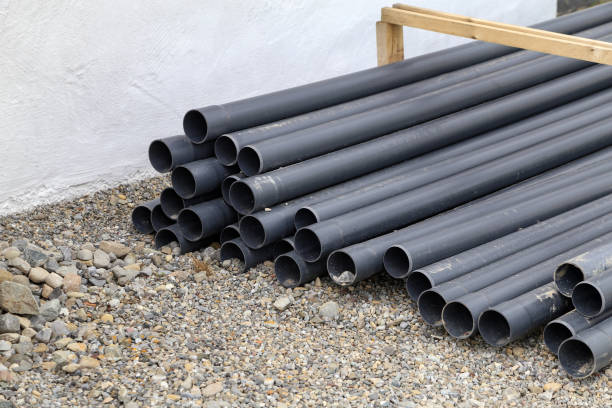
1. Introduction to HDPE in Geothermal Systems
HDPE pipes and fittings are ideal for geothermal loops due to their flexibility, chemical inertness, and ability to withstand ground movement and temperature fluctuations. Unlike metal alternatives, HDPE does not corrode or degrade when exposed to soil moisture or geothermal fluids, making it a cost-effective and low-maintenance choice.
2. Innovations in Material Science
Manufacturers are now developing HDPE resins specifically tailored for geothermal applications. These advanced materials, such as PE100-RC (Resistance to Crack) and PE4710, offer enhanced stress crack resistance and improved toughness. Such innovations ensure that fittings endure the mechanical stresses of installation and the thermal cycling inherent in geothermal systems.
3. Optimized Fitting Designs for Efficiency
New HDPE fitting feature streamlined designs that minimize pressure drops and improve heat transfer efficiency. For instance, electrofusion and butt fusion fittings now incorporate smoother internal surfaces and reduced turbulence-inducing geometries. These optimizations enhance the overall performance of geothermal loops, reducing energy consumption and operational costs.
4. Seismic and Ground Movement Resistance
Geothermal systems installed in earthquake-prone regions require fittings that can accommodate ground movement without failure. Latest HDPE fitting include flexible joints and articulated designs that absorb seismic stresses, preventing leaks or pipe disconnections. This feature is critical for maintaining system integrity in areas prone to tectonic activity.
5. Enhanced Leak Detection and Monitoring
Advanced HDPE fitting now integrate smart sensors for real-time leak detection and pressure monitoring. These fittings can alert operators to potential issues before they escalate, enabling proactive maintenance and reducing downtime. Such innovations align with the growing trend toward smart infrastructure in sustainable energy systems.
6. Sustainability and Recyclability
The geothermal industry is increasingly prioritizing eco-friendly solutions. HDPE fittings are fully recyclable, and manufacturers are adopting production processes that minimize energy consumption and waste. Additionally, the long lifespan of HDPE (50+ years) reduces the need for replacements, further lowering the environmental impact of geothermal installations.
7. Compatibility with Advanced Fluids
Some geothermal systems now use environmentally friendly heat transfer fluids, such as propylene glycol-based solutions, to reduce ecological risks. New HDPE fittings are tested for compatibility with these fluids, ensuring they resist chemical degradation and maintain structural integrity over time.
8. Installation and Maintenance Advancements
Modern HDPE fittings are designed for easier installation, with features like quick-connect couplings and pre-insulated options that reduce labor costs and installation time. Additionally, self-sealing gaskets and push-fit joints simplify maintenance, allowing technicians to repair or replace fittings without disrupting the entire system.
FAQ
Q1: What is the primary advantage of using HDPE fittings in geothermal systems over metal alternatives?
A1: HDPE fittings are corrosion-resistant, flexible, and durable, eliminating the risk of rust or degradation common in metal pipes. They also offer lower installation and maintenance costs.
Q2: How do new HDPE fitting improve energy efficiency in geothermal systems?
A2: Innovations like optimized internal geometries and reduced pressure drops minimize energy losses, improving the coefficient of performance (COP) of heat pumps and reducing overall energy consumption.
Q3: Can HDPE fittings withstand extreme temperatures in geothermal applications?
A3: Yes, HDPE fittings are rated for temperatures ranging from -40°C to 60°C (-40°F to 140°F), making them suitable for most geothermal loop installations.
Q4: Are there any certifications to look for when selecting HDPE fittings for geothermal systems?
A4: Look for fittings certified by organizations like NSF International, ASTM, or ISO to ensure they meet industry standards for pressure ratings, material quality, and longevity.
Q5: How long do HDPE fittings typically last in a geothermal system?
A5: When installed correctly, HDPE fitting can last 50+ years, outlasting many traditional materials and reducing lifecycle costs.
By leveraging these technical advancements, HDPE pipe fittings are playing a pivotal role in advancing the efficiency and reliability of ground source geothermal systems, paving the way for a more sustainable energy future.