The Alexander First Nation, a thriving Indigenous community in Alberta, Canada, has officially opened a state-of-the-art HDPE (High-Density Polyethylene) pipe fittings manufacturing facility. This initiative marks a significant step toward economic self-sufficiency, sustainable infrastructure development, and job creation within the community. The plant aims to supply durable, eco-friendly piping solutions for water management, agriculture, and municipal projects across Canada.
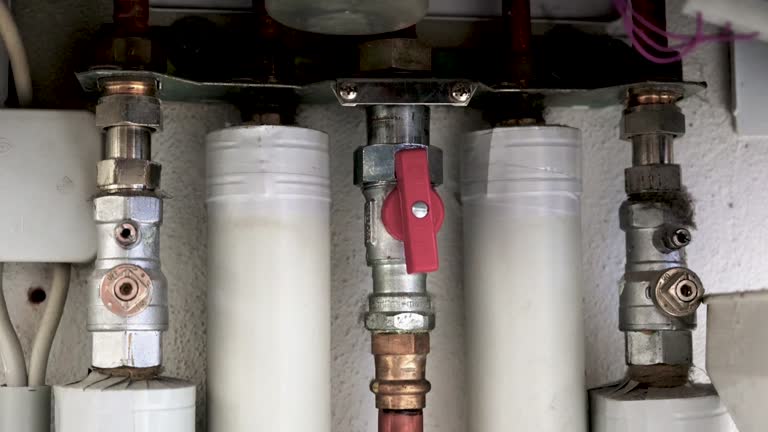
1. Driving Economic Sovereignty
The Alexander First Nation’s decision to invest in HDPE pipe fittings stems from a vision to reduce reliance on external suppliers and generate local revenue. By owning and operating the facility, the community retains profits, reinvests in community programs, and fosters long-term financial stability. The project is part of a broader strategy to diversify the economy beyond traditional sectors like agriculture and forestry.
2. Meeting Regional Infrastructure Demands
Canada’s aging water and sewage systems require urgent upgrades, particularly in rural and Indigenous communities. The new facility will produce HDPE fittings for pressure pipes, irrigation systems, and stormwater management, addressing critical gaps in infrastructure resilience. HDPE’s corrosion resistance and flexibility make it ideal for withstanding Canada’s harsh winters and varying soil conditions.
3. Sustainability and Environmental Stewardship
The plant prioritizes eco-friendly practices, using 100% recyclable HDPE and minimizing waste through efficient production processes. Fittings are designed for leak-proof joints, reducing water loss—a vital consideration in drought-prone regions. Additionally, the facility operates on renewable energy where possible, aligning with Canada’s net-zero emissions goals and the Alexander First Nation’s commitment to environmental stewardship.
4. Job Creation and Skills Development
The facility has created over 50 full-time jobs, with a focus on hiring community members and providing on-the-job training. Employees gain expertise in injection molding, quality control, and supply chain management, equipping them with transferable skills for future career opportunities. The project also includes apprenticeship programs to nurture the next generation of Indigenous tradespeople.
5. Collaborating with Industry and Government
The Alexander First Nation has partnered with leading HDPE manufacturers and engineering firms to ensure the facility meets Canadian Standards Association (CSA) and ASTM International guidelines. Federal and provincial grants, including funding from the Indigenous Community Infrastructure Fund, have supported the project’s startup costs. These collaborations strengthen the community’s role in Canada’s infrastructure supply chain.
6. Innovative Product Offerings
The plant produces a range of HDPE fittings, including electrofusion, butt fusion. And compression couplings, in sizes from 20mm to 1,200mm. Specialty products, such as UV-resistant fittings for outdoor use and freeze-resistant designs for cold climates, cater to Canada’s diverse geography. The community also plans to develop smart fittings with IoT sensors for real-time leak detection in the future.
7. Empowering Indigenous Entrepreneurship
Beyond manufacturing, the Alexander First Nation is exploring distribution partnerships to expand its market reach. The facility serves as a model for other Indigenous communities seeking to enter the infrastructure sector. Demonstrating how resourcefulness and strategic partnerships can drive economic empowerment.
8. Future Expansion and Global Ambitions
With initial success, the community aims to double production capacity within three years and explore export opportunities to the United States and international markets. Long-term goals include becoming a hub for sustainable HDPE innovation, contributing to global efforts to combat water scarcity through efficient piping systems.
FAQ
Q1: What types of HDPE pipe fittings does the Alexander First Nation facility produce?
A1: The facility manufactures electrofusion, butt fusion, and compression fittings for water, gas, and wastewater systems, available in sizes from 20mm to 1,200mm.
Q2: Are the fittings suitable for Canada’s cold climate?
A2: Yes, the fittings are designed to withstand temperatures as low as -40°C, with freeze-resistant properties to prevent cracking in icy conditions.
Q3: How does the project benefit the Alexander First Nation community?
A3: The facility creates jobs, generates revenue, and provides skills training. Profits are reinvested in community services like healthcare, education, and housing.
Q4: Can the fittings be used for agricultural irrigation?
A4: Absolutely. The fittings are ideal for drip irrigation systems, offering durability and leak-proof performance to conserve water in farming operations.
Q5: Does the community offer financing for projects using its HDPE fittings?
A5: While the facility focuses on manufacturing, it collaborates with financial institutions to offer flexible payment terms for municipalities and Indigenous-led projects.
By pioneering HDPE pipe fittings production, the Alexander First Nation is not only strengthening its own future but also setting a precedent for sustainable, Indigenous-led economic development in Canada.