The global demand for HDPE pipes continues to surge as infrastructure projects, environmental regulations, and population growth drive a need for sustainable, durable pipeline solutions. Industry analysts now forecast that the global HDPE pipes market will reach unprecedented levels by 2029, surpassing earlier predictions and setting new benchmarks for both volume and value.
Stakeholders across construction, agriculture, municipal utilities, and industrial sectors increasingly choose HDPE (High-Density Polyethylene) as their preferred material. These pipes deliver unmatched performance in flexibility, corrosion resistance, and lifespan. As more governments and private entities invest in smart infrastructure, the global HDPE pipes market strengthens its position as a future-ready industry.
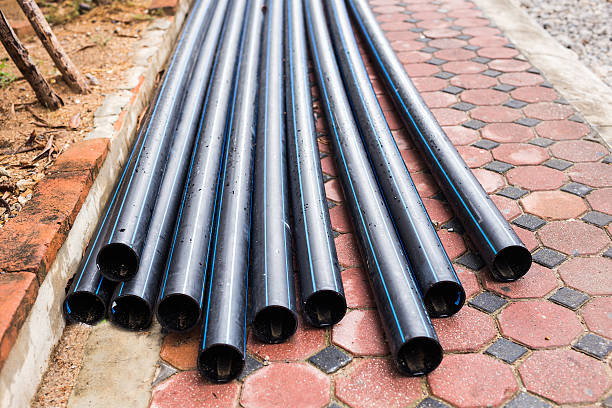
Strong Growth Drivers Across Key Regions
Asia-Pacific leads the global market for HDPE pipes, with China, India, and Southeast Asian countries ramping up investments in water supply networks, sewerage systems, and gas distribution. These nations face growing urban populations and deteriorating infrastructure. Their governments prioritize long-lasting, low-maintenance piping, and HDPE offers the most practical solution.
North America and Europe also witness rising adoption of HDPE pipes due to stricter environmental standards and increasing replacement of outdated metal and concrete pipes. In these regions, municipalities focus on leak-free systems, water conservation, and sustainability. HDPE’s performance under extreme temperatures and aggressive soil conditions makes it the top choice for modern infrastructure development.
Applications Fueling Market Expansion
Construction firms rely on HDPE pipes for water supply lines, fire protection systems, and underground cable conduits. Agriculture projects benefit from HDPE’s flexibility and easy installation in irrigation networks. Municipalities install HDPE pipelines for stormwater drainage and sewage treatment due to their resistance to chemical corrosion and root intrusion.
In the energy sector, natural gas and industrial chemical transportation also rely on HDPE’s non-reactive properties. The versatility of HDPE across so many sectors directly supports the forecasted market value increase by 2029.
Technological Innovations Enhance Market Momentum
Manufacturers now produce large-diameter and high-pressure HDPE pipe systems for use in major infrastructure projects. These advancements allow engineers to design longer runs with fewer joints, reducing potential leak points and installation time. Smart fusion welding techniques improve joint integrity and speed up the installation process, even in remote or challenging environments.
In addition, many producers now integrate recycled HDPE into non-pressure applications, which reduces production emissions and enhances circular economy goals. These innovations keep HDPE pipes ahead of other materials in terms of both performance and environmental benefits.
Competitive Landscape and Strategic Partnerships
Leading manufacturers such as JM Eagle, Uponor, Aliaxis, Pipelife, and WL Plastics continue to expand capacity and geographic reach. These companies form partnerships with government bodies and engineering firms to secure long-term infrastructure contracts. They also invest in R&D to develop specialized HDPE formulations for mining, oil and gas, and coastal engineering.
Smaller regional players focus on niche markets such as agricultural piping or telecommunications. These firms help the HDPE pipes sector maintain diversity and responsiveness to local needs, while still aligning with global market trends.
Sustainability Remains a Core Advantage
Environmental benefits represent a key pillar of the projected growth. HDPE’s long lifespan—often exceeding 50 years—reduces the need for replacement, repair, or chemical maintenance. The material’s recyclability, leak resistance, and minimal energy consumption during production make it an eco-conscious alternative to metal or cement-based systems.
Governments and corporate buyers now use lifecycle assessment (LCA) tools when selecting pipeline materials. These tools regularly favor HDPE pipes in categories such as carbon emissions, installation impact, and long-term reliability. As ESG (Environmental, Social, Governance) standards grow in importance, HDPE continues to score high on sustainability metrics.
Forecast and Market Value by 2029
Market research firms project the global HDPE pipes market to reach a value of over USD 34 billion by 2029, with a compound annual growth rate (CAGR) of approximately 6%–8%. Asia-Pacific will retain the largest market share, while the Middle East and Africa will experience rapid growth due to increasing investments in oil and gas infrastructure.
Meanwhile, digital monitoring systems and IoT integration into pipeline management will add further value to HDPE pipes. These technologies enable operators to detect pressure loss, leaks, or system failure early, which improves efficiency and reduces long-term costs.
Challenges and Opportunities
The HDPE industry still faces a few challenges. Fluctuating raw material prices—especially resin—can affect profitability. Additionally, a lack of skilled installers in some developing markets may hinder adoption. However, companies continue to provide technical training, installation guidelines, and equipment to address these issues.
Opportunities continue to outweigh challenges. New government regulations, aging water systems, and environmental pressures all create favorable conditions for expanded use of HDPE pipes. With innovation, strategic investment, and international collaboration, the market remains on track for major growth by 2029.
FAQ: Installation of HDPE Pipes
Q1: What method should I use to join HDPE pipes?
You should use butt fusion or electrofusion welding for permanent, leak-proof joints. Both methods create seamless connections that resist separation and leakage.
Q2: Can I install HDPE pipes in trenchless applications?
Yes. HDPE suits trenchless methods such as horizontal directional drilling (HDD) and slip lining. Its flexibility and strength allow it to handle underground stress without failure.
Q3: How do I handle HDPE pipes during installation?
Use soft slings or padded supports to avoid scratching the surface. Avoid dragging pipes over rough terrain, and store them in shaded areas when possible.
Q4: Do HDPE pipes require thrust blocks?
No. Fusion-welded joints eliminate the need for external thrust blocks, as the joints themselves handle internal pressure and directional changes.
Q5: Can I install HDPE pipes in cold weather?
Yes, but you should follow cold-weather fusion protocols. Preheat the joint area properly, and allow extra time for cooling and alignment to ensure a proper bond.