Kabra Extrusiontechnik, a leading manufacturer of plastic processing machinery in India, has launched a state-of-the-art HDPE pipe fittings extrusion plant, designed to deliver high-precision, durable fittings for water, gas, and industrial applications. This complete production line integrates advanced technology, energy efficiency, and customizable accessories to meet the growing demand for reliable piping solutions globally.
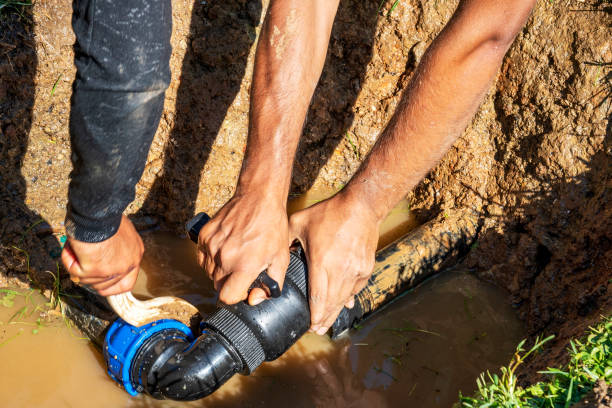
1. Innovative Extrusion Technology
The Kabra HDPE extrusion plant employs a co-rotating twin-screw extruder, renowned for its uniform melting and mixing capabilities. This ensures consistent material distribution, critical for producing fittings with precise dimensions and wall thickness. The extruder’s modular design allows easy adaptation for different HDPE grades, including virgin and recycled resins.
2. Versatile Molding Capabilities
The plant includes a multi-station injection molding machine tailored for HDPE fittings like elbows, tees, couplings, and reducers. Equipped with servo-driven hydraulics, it reduces energy consumption by up to 30% compared to traditional systems. Quick-change tooling enables rapid transitions between fitting sizes, minimizing downtime and boosting productivity.
3. Precision Tooling and Die Design
Kabra’s tooling is engineered for accuracy, with CNC-machined dies that maintain tight tolerances (±0.1mm) across fittings ranging from 20mm to 630mm in diameter. Advanced cooling channels in the dies ensure rapid solidification, reducing warpage and enhancing surface finish. The plant also supports custom die designs for specialized fittings, such as double-wall corrugated or electrofusion types.
4. Energy-Efficient Operations
Sustainability is a core focus, with the plant incorporating energy-recovery systems that reuse heat from the extruder to preheat raw materials. Variable Frequency Drives (VFDs) optimize motor speeds, cutting power use by 20–25%. Additionally, the use of LED lighting and insulated machinery enclosures further reduces operational carbon footprints.
5. Automated Quality Control
Integrated sensors and vision systems monitor fittings in real time, detecting defects such as voids, discoloration, or dimensional deviations. Automated rejection mechanisms ensure only compliant products proceed to packaging. This reduces scrap rates to below 1% and ensures adherence to international standards like ISO 4427 and ASTM D2513.
6. Comprehensive Accessories Package
The complete line includes accessories like:
- Material Handling Systems: Vacuum conveyors and silos for seamless resin feeding.
- Post-Extrusion Equipment: Annealing ovens to relieve stress and improve impact resistance.
- Marking Systems: Laser engravers for permanent part identification.
- Packaging Solutions: Auto-stackers and shrink-wrap machines for efficient bundling.
7. Training and Technical Support
Kabra offers comprehensive operator training, covering machine setup, maintenance, and troubleshooting. A 24/7 technical support team and a global network of service centers ensure minimal downtime. Regular software updates and spare parts availability guarantee long-term reliability.
8. Global Market Adaptability
The plant’s flexibility allows manufacturers to cater to diverse markets—from rural water projects in Africa to high-pressure gas networks in Europe. Kabra’s R&D team collaborates with clients to customize solutions for extreme climates, such as UV-resistant coatings for sunny regions or freeze-resistant designs for cold areas.
FAQ
Q1: What sizes of HDPE fittings can the Kabra plant produce?
A1: The plant can manufacture fittings from 20mm to 630mm in diameter, with custom tooling available for larger sizes upon request.
Q2: Does the plant support recycled HDPE (rHDPE) production?
A2: Yes, the co-rotating twin-screw extruder is optimized for processing rHDPE, ensuring consistent quality even with 50%+ recycled content.
Q3: How energy-efficient is the Kabra HDPE extrusion line?
A3: The plant reduces energy consumption by 20–30% through VFDs, heat recovery systems, and servo-driven hydraulics, lowering operational costs.
Q4: What certifications do Kabra’s HDPE fittings meet?
A4: The fittings comply with ISO 4427, ASTM D2513, and other global standards, ensuring suitability for potable water, gas, and industrial applications.
Q5: Can the plant be upgraded for smart fittings (e.g., IoT sensors)?
A5: Yes, Kabra offers retrofit options to integrate sensors for leak detection, pressure monitoring, or RFID tracking during the molding process.
By offering a complete, customizable HDPE pipe fittings extrusion line, Kabra Extrusiontechnik empowers manufacturers to deliver high-quality, sustainable solutions for infrastructure projects worldwide.