In recent developments within the oil and gas sector, Bharat Petroleum Corporation Limited (BPCL) has made a significant decision to adopt Univation’s polyethylene (PE) pipe process for its Bina refinery. This choice emphasizes the growing importance of HDPE pipe in modern industrial applications. In this article, we will explore the significance of BPCL’s selection, the advantages of HDPE pipes, and their applications within the refinery context.
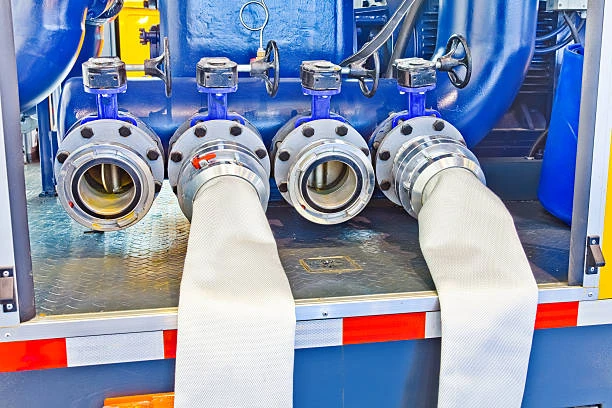
Understanding HDPE Pipe
High-Density Polyethylene (HDPE) pipes are widely recognized for their durability, flexibility, and resistance to various chemicals. These pipes are manufactured from high-density polyethylene, which provides them with exceptional strength and longevity. In contrast to traditional materials like metal or PVC, HDPE pipes offer numerous advantages, making them ideal for applications in the oil and gas industry.
Key Characteristics of HDPE Pipe
- Durability: HDPE pipes are resistant to corrosion, impact, and environmental stress. This makes them suitable for harsh industrial environments, ensuring a longer lifespan with minimal maintenance.
- Flexibility: The flexibility of HDPE pipes allows for easy installation and transportation, particularly in complex systems. They can be coiled, which reduces the need for additional fittings and joints.
- Chemical Resistance: HDPE is highly resistant to a wide range of chemicals, making it suitable for carrying various substances without degrading or contaminating the contents.
- Cost-Effectiveness: While the initial investment in HDPE pipes may be higher than other materials, their durability and low maintenance costs often result in significant savings over time.
- Environmental Impact: HDPE pipes are recyclable, aligning with sustainable practices and reducing the environmental footprint of industrial projects.
HDPE pipe BPCL’s Decision and Its Implications
The decision by BPCL to select Univation’s PE pipe process signals a strategic move towards modernizing its infrastructure at the Bina refinery. This choice is influenced by several factors:
HDPE pipe Enhanced Operational Efficiency
By integrating HDPE pipes into the refinery’s operations, BPCL aims to enhance efficiency and reliability. The durability and chemical resistance of HDPE will minimize downtime caused by leaks or pipe failures, allowing the refinery to operate smoothly and continuously.
HDPE pipe Sustainability Goals
BPCL has been actively pursuing sustainability initiatives, and the use of HDPE pipes aligns with these goals. The recyclability of HDPE material reduces waste and supports BPCL’s commitment to environmental stewardship.
Safety Considerations
The oil and gas industry is inherently risky, with potential hazards associated with transporting flammable and toxic materials. HDPE pipes offer superior safety features, including resistance to corrosion and reduced likelihood of leaks, thereby enhancing overall workplace safety.
Applications of HDPE Pipe in Refineries
HDPE pipes find a myriad of applications within the refinery context. Here are some key areas where they are particularly beneficial:
1. Transporting Crude Oil and HDPE pipe Refined Products
HDPE pipes are ideal for the transportation of crude oil and various refined products due to their resistance to chemicals and ability to handle high pressures. Their flexibility allows for complex routing, accommodating the layout of refinery infrastructure.
2. HDPE pipe Wastewater Management
Refineries generate significant amounts of wastewater that require effective management. HDPE pipes can be used for collecting and transporting wastewater to treatment facilities, ensuring compliance with environmental regulations.
3. HDPE pipe Cooling Water Systems
HDPE pipes are use in cooling systems to manage temperatures in various refinery processes. Their thermal resistance and durability ensure efficient operation under varying conditions.
4. HDPE pipe Fire Protection Systems
In refineries, fire protection is paramount. HDPE pipes can be integrate into fire suppression systems due to their ability to withstand heat and chemicals, ensuring the safety of personnel and equipment.
5. Fuel Gas Distribution
For distributing fuel gases within the refinery, HDPE pipes provide a lightweight and flexible solution. Their resistance to corrosion and high pressures makes them a preferred choice for safe and efficient gas transport.
Challenges and Considerations
While the advantages of HDPE pipes are compelling, there are also challenges to consider. Proper installation and adherence to industry standards are crucial to maximizing the benefits of HDPE. Additionally, the selection of compatible fittings and accessories is essential to prevent potential issues.
Installation Practices
To ensure the longevity and efficiency of HDPE pipes, proper installation practices must be followe. This includes:
- Correct Jointing Techniques: Utilizing heat fusion or electrofusion methods to create strong, leak-proof joints.
- Trenchless Technology: Implementing trenchless installation methods can minimize surface disruption and reduce installation time.
- Regular Inspections: Conducting routine inspections can help identify potential issues before they escalate.
Regulatory Compliance
Compliance with local and international regulations is critical in the oil and gas sector. BPCL’s commitment to using HDPE pipes will involve ensuring that all materials and installation practices meet regulatory standards.
The Future of HDPE in the Oil and Gas Industry
The selection of Univation’s PE pipe process by BPCL marks a significant step towards modernization and sustainability in the oil and gas industry. As the demand for efficient, safe, and environmentally friendly solutions continues to rise, the adoption of HDPE pipes is expecte to grow.
Innovations in HDPE Technology
Research and development in HDPE technology are ongoing. Innovations such as enhanced barrier properties, improved stress resistance, and advancements in installation techniques will further solidify HDPE’s role in the industry.
Broader Applications
As industries increasingly recognize the benefits of HDPE, its applications are likely to expand beyond traditional uses. Future developments may include the integration of smart technology for monitoring and maintenance, enhancing the performance and reliability of HDPE systems.
Conclusion
BPCL’s selection of Univation’s PE pipe process for the Bina refinery underscores the vital role that HDPE pipes play in modern industrial applications. Their durability, flexibility, and resistance to harsh chemicals make them an ideal choice for the oil and gas sector. As the industry continues to evolve, HDPE pipes will undoubtedly remain at the forefront, contributing to safer, more efficient, and sustainable operations.
Frequently Asked Questions (FAQs)
- What are HDPE pipes? HDPE pipes are pipes make from high-density polyethylene, known for their strength, flexibility, and chemical resistance.
- What are the main advantages of using HDPE pipes in refineries? The main advantages include durability, chemical resistance, flexibility, cost-effectiveness, and reduced environmental impact.
- How are HDPE pipes installed? HDPE pipes can be installe using various methods, including heat fusion, electrofusion, and trenchless technology.
- Are HDPE pipes recyclable? Yes, HDPE pipes are recyclable, making them an environmentally friendly choice for industrial applications.
- What applications do HDPE pipes have in the oil and gas industry? HDPE pipes are use for transporting crude oil, managing wastewater, cooling systems, fire protection, and fuel gas distribution.