The demand for High-Density Polyethylene HDPE pipe continues to grow across various industries, driven by their durability, flexibility, and resistance to corrosion. As municipalities and industries invest in upgrading their infrastructure, establishing an HDPE pipe manufacturing plant presents a lucrative business opportunity. This article provides a comprehensive project report for setting up an HDPE pipe manufacturing plant in 2024, focusing on cost analysis and raw material requirements.
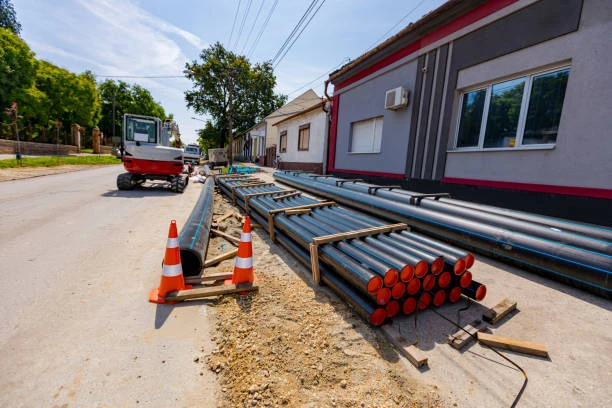
Understanding HDPE Pipe
High-Density Polyethylene (HDPE) pipes are thermoplastic pipes made from high-density polyethylene, known for their strength, lightweight nature, and resistance to chemicals and environmental stress. They are widely used in water supply, sewage systems, and industrial applications due to their long service life and reduced leakage rates.
Key Benefits of HDPE Pipe
- Durability: HDPE pipes are resistant to corrosion and wear, making them suitable for harsh environments.
- Flexibility: Their flexibility allows for easier installation, particularly in challenging terrains.
- Cost-Effectiveness: While initial investments may be higher, the longevity and reduced maintenance costs make HDPE pipes economically viable.
- Environmental Sustainability: HDPE is recyclable, contributing to reduced waste and environmental impact.
Market Overview
The global HDPE pipe market is expected to grow significantly, with projections indicating a market size of USD 39.6 billion by 2032. This growth is driven by increased infrastructure investments and a focus on sustainable solutions.
Key Market Drivers
- Urbanization: Growing urban populations require efficient water supply and drainage systems.
- Infrastructure Development: Governments are investing in new infrastructure, particularly in developing countries.
- Environmental Regulations: Stricter regulations encourage the use of sustainable materials, including HDPE.
Setting Up an HDPE Pipe Manufacturing Plant
HDPE pipe Project Scope and Objectives
The primary objective of this project is to establish a manufacturing plant capable of producing HDPE pipes of various diameters and specifications to meet market demands.
Location Considerations
Choosing the right location is critical for the success of the manufacturing plant. Factors to consider include:
- Proximity to raw material suppliers
- Access to transportation and logistics
- Availability of skilled labor
- Local regulations and incentives
HDPE pipe Cost Analysis
The cost of setting up an HDPE pipe manufacturing plant can be broken down into several key components:
- Capital Investment: This includes the cost of land, building construction, and machinery.
- Operational Costs: Ongoing expenses such as utilities, labor, and maintenance.
- Raw Material Costs: The cost of sourcing HDPE resin and other necessary materials.
HDPE pipe Estimated Capital Investment
- Land Acquisition: $200,000 – $500,000 (depending on location)
- Building Construction: $300,000 – $700,000
- Machinery and Equipment: $500,000 – $1,000,000
- Initial Working Capital: $100,000 – $300,000
Total Estimated Capital Investment: $1.1 million – $2.5 million
Operational Costs Breakdown
- Labor Costs: $50,000 – $150,000 annually (depending on workforce size)
- Utilities: $30,000 – $60,000 annually
- Maintenance: $20,000 – $50,000 annually
- Miscellaneous Expenses: $10,000 – $30,000 annually
Total Estimated Annual Operational Costs: $120,000 – $290,000
Raw Material Requirements
The primary raw material for manufacturing HDPE pipes is high-density polyethylene resin. Other materials required include:
- Additives: These may include UV stabilizers, colorants, and antioxidants to enhance the properties of the HDPE pipes.
- Blending Agents: To ensure uniformity in the manufacturing process.
Sourcing Raw Materials
- HDPE Resin: Sourced from petrochemical suppliers. Prices can vary based on market conditions but typically range from $1,200 to $1,800 per ton.
- Additives: Usually sourced from specialty chemical suppliers. Costs depend on the type and quantity used.
Estimated Raw Material Costs
Assuming a production capacity of 1,000 tons of HDPE pipes per year, raw material costs can be estimate as follows:
- HDPE Resin: $1,200 – $1,800 per ton
- Additives: $100 – $300 per ton
Total Estimated Raw Material Costs: $1.3 million – $2.1 million annually
Production Process
The manufacturing process for HDPE pipes typically involves the following steps:
- Material Preparation: Sourcing and preparing HDPE resin and additives.
- Extrusion: The resin is melte and extruded through a die to form pipes of desired dimensions.
- Cooling and Sizing: The extruded pipe is coole and cut to specified lengths.
- Quality Control: Each batch of pipes is teste for quality, including pressure tests and dimensional checks.
- Packaging: Finished pipes are package for shipment.
HDPE pipe Equipment Required
- Extruder: For melting and shaping the HDPE resin.
- Cooling Tank: To cool the extruded pipes.
- Cutting Machine: For cutting pipes to required lengths.
- Testing Equipment: For quality control checks.
Marketing and HDPE pipe Sales Strategy
To ensure the success of the HDPE pipe manufacturing plant, an effective marketing strategy is essential. Key components of this strategy may include:
- Market Research: Understanding target markets and customer needs.
- Brand Development: Creating a strong brand identity to differentiate from competitors.
- Sales Channels: Establishing relationships with distributors, contractors, and municipalities.
- Online Presence: Developing a website and utilizing social media for outreach and engagement.
Financial Projections
Revenue Projections
Assuming an average selling price of $2,000 per ton for HDPE pipes, with a production capacity of 1,000 tons per year, the potential revenue can be estimate as follows:
- Annual Revenue: $2 million (based on full production capacity)
HDPE pipe Profitability Analysis
Considering the estimate operational costs and raw material costs, the profitability can be projected:
- Total Annual Costs: $1.5 million – $2.3 million
- Net Profit: $700,000 – $500,000 annually (after deducting all costs)
HDPE pipe Conclusion
The establishment of an HDPE pipe manufacturing plant in 2024 presents a promising opportunity, driven by increasing demand for durable and sustainable piping solutions. With careful planning, cost analysis, and effective marketing strategies, the venture can yield significant profits. As infrastructure development continues to rise globally, the need for reliable HDPE pipes will only grow, making this a strategic investment for the future.
HDPE pipe Frequently Asked Questions (FAQs)
- What are HDPE pipes?
- HDPE pipes are high-density polyethylene pipes known for their strength, flexibility, and resistance to corrosion, widely use in various applications.
- What is the estimate cost to set up an HDPE pipe manufacturing plant?
- The estimated cost ranges from $1.1 million to $2.5 million, depending on location and production capacity.
- What are the main raw materials needed for HDPE pipe manufacturing?
- The primary raw material is HDPE resin, along with additives and blending agents.
- What is the production capacity of the proposed plant?
- The proposed plant has a production capacity of 1,000 tons of HDPE pipes per year.
- What are the expected annual revenues from the HDPE pipe manufacturing plant?
- The potential annual revenue is estimate at around $2 million, based on full production capacity.