As the global demand for High-Density Polyethylene HDPE pipe continues to rise, the establishment of new HDPE pipe manufacturing plants is on the horizon for 2024. This article will explore the essential aspects of setting up a manufacturing unit for HDPE pipes, industry trends, and the critical role of pipe press fittings in enhancing the overall performance and efficiency of HDPE piping systems.
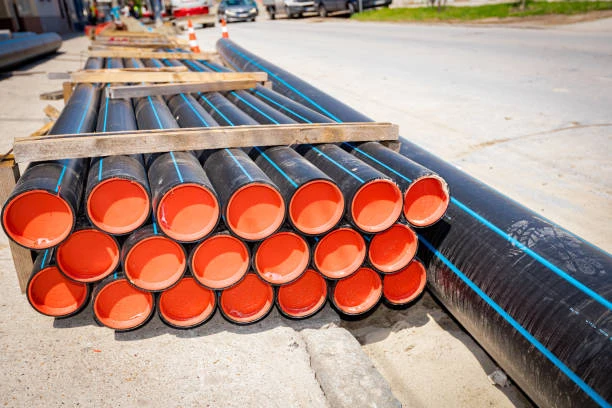
Understanding HDPE Pipes
High-Density Polyethylene pipes are widely utilized in various sectors, including water distribution, sewage systems, industrial applications, and agricultural irrigation. Known for their durability, flexibility, and resistance to corrosion, HDPE pipes are a preferred choice for modern infrastructure.
Key Features of HDPE Pipes
- Corrosion Resistance: HDPE pipes do not rust or corrode, making them ideal for transporting water and chemicals.
- Durability: With a lifespan that can exceed 50 years, HDPE pipes require minimal maintenance and replacement.
- Lightweight: Their lightweight nature simplifies transportation and installation compared to traditional materials like steel and concrete.
- Flexibility: HDPE pipes can bend without breaking, allowing for easier installation around obstacles.
- Environmental Sustainability: HDPE is recyclable, contributing to a reduced environmental footprint in construction and infrastructure projects.
Setting Up an HDPE Pipe Manufacturing Plant
Establishing an HDPE pipe manufacturing plant requires careful planning and consideration of various factors. Below are the key steps involved in setting up a successful unit.
1. Market Research and Feasibility Study
Before setting up a manufacturing plant, it’s crucial to conduct thorough market research to understand the demand for HDPE pipes in your target region. A feasibility study will help assess the project’s financial viability, identifying potential risks and opportunities.
2. Location Selection
Choosing the right location is vital for the success of the manufacturing unit. Factors to consider include proximity to raw material suppliers, transportation infrastructure, and access to skilled labor. An optimal location can reduce logistics costs and enhance operational efficiency.
3. Facility Design and Layout
The layout of the manufacturing facility should optimize workflow and efficiency. Key areas to consider include:
- Production Area: Space for extrusion machines, pipe winding units, and quality control stations.
- Storage: Adequate storage for raw materials and finished products to facilitate smooth operations.
- Office Space: Administrative areas for management and support staff.
4. Equipment and Machinery
Investing in high-quality machinery is essential for producing HDPE pipes that meet industry standards. Key equipment includes:
- Extrusion Machines: For shaping HDPE into pipes.
- Winding Machines: Specifically for manufacturing HDPE winding pipes.
- Quality Control Equipment: For testing pipe strength, diameter, and other specifications.
5. Compliance and Certification
Adhering to local and international standards is crucial for any manufacturing plant. Obtain necessary permits and certifications, such as ISO standards and compliance with environmental regulations, to ensure quality and safety.
6. Skilled Workforce
Recruiting and training a skilled workforce is vital for the successful operation of the manufacturing plant. Invest in training programs to ensure that employees are proficient in operating machinery and adhering to quality control processes.
7. Supply Chain Management
Developing a robust supply chain is essential for sourcing raw materials and distributing finished products. Establish relationships with reliable suppliers and logistics partners to ensure a smooth operation.
Industry Trends Influencing HDPE Pipe Manufacturing
As the HDPE pipe market evolves, several trends are shaping the industry landscape and influencing manufacturing processes.
1. Increased Demand for Sustainable Solutions
Environmental sustainability is a growing priority across industries. The shift toward sustainable practices is driving demand for recyclable materials like HDPE, which aligns with eco-friendly construction methods.
2. Technological Advancements
Innovations in manufacturing technologies are enhancing the efficiency and quality of HDPE pipe production. Automation and smart manufacturing processes are becoming more prevalent, leading to improved output and reduced labor costs.
3. Expansion in Infrastructure Projects
Global investments in infrastructure development are expected to rise significantly, particularly in emerging markets. This growth presents substantial opportunities for HDPE pipe manufacturers to meet the demand for reliable piping solutions in water and sewage systems.
4. Shift Towards Modular Construction
Modular construction practices are gaining popularity, and HDPE pipes play a crucial role in these systems. The lightweight and flexible nature of HDPE allows for easier integration into modular designs, enhancing overall project efficiency.
5. Rising Adoption of Smart Piping Systems
The integration of technology into piping systems, such as sensors and monitoring devices, is emerging as a significant trend. Smart HDPE piping systems can provide real-time data on pressure, flow rates, and potential leaks, contributing to proactive maintenance and enhanced system reliability.
The Critical Role of HDPE pipe Press Fittings
As HDPE pipe production expands, the importance of pipe press fittings cannot be overstated. These fittings ensure the integrity and efficiency of HDPE piping systems.
Benefits of HDPE pipe Press Fittings
- Quick Installation: Pipe press fittings allow for rapid installation, reducing project timelines and labor costs.
- Leak-Free Connections: The pressing technology creates strong, permanent seals that prevent leaks, enhancing the reliability of HDPE systems.
- Cost Efficiency: By minimizing installation time and requiring fewer specialized tools, pipe press fittings lower overall project costs.
- Compatibility: Many press fittings are designed to work with various materials, including HDPE, offering flexibility in project design.
- Minimal Maintenance: Once installed, pipe press fittings require little maintenance, ensuring long-term reliability and performance.
Conclusion
The establishment of new HDPE pipe manufacturing plants in 2024 presents an exciting opportunity for growth in the industry. By understanding the key aspects of setting up a manufacturing unit and recognizing the trends shaping the market, businesses can position themselves for success. The critical role of pipe press fittings in ensuring efficient and reliable connections further underscores the importance of quality manufacturing processes. As the demand for HDPE pipes continues to rise, manufacturers who prioritize innovation and sustainability will thrive in the evolving landscape.
FAQs
1. What are HDPE pipe used for?
HDPE pipes are used in various applications, including water distribution, sewage management, industrial fluid transport, and agricultural irrigation.
2. How do pipe press fittings benefit HDPE pipe systems?
Pipe press fittings provide quick installation, leak-free connections, cost efficiency, and require minimal maintenance.
3. What are the key steps in setting up an HDPE pipe manufacturing plant?
Key steps include conducting market research, selecting a location, designing the facility, investing in machinery, ensuring compliance, recruiting a skilled workforce, and managing the supply chain.
4. What trends are currently influencing the HDPE pipe industry?
Trends include increased demand for sustainable solutions, technological advancements, expansion in infrastructure projects, a shift towards modular construction, and the rising adoption of smart piping systems.
5. Why is environmental sustainability important for HDPE pipe?
Environmental sustainability is important because HDPE pipes are recyclable and contribute to reducing waste and carbon footprints in construction and infrastructure projects.