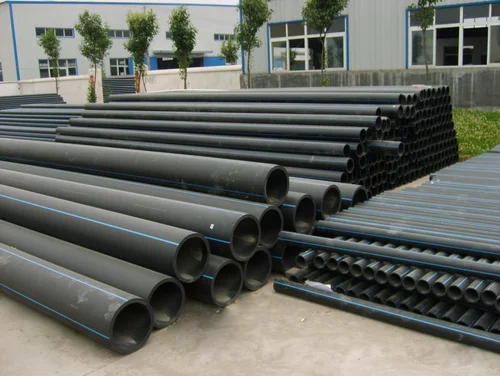
Introduction
PE pipes are renowned for their durability and resistance to environmental factors, making them a popular choice for various piping applications. However, despite their resilience, these pipes are not immune to damage. Identifying wall damage in PE pipes is crucial for maintaining system integrity and preventing failures. The PE Pipe Wall Damage Indicator is a tool designed to help detect and assess damage to the pipe walls. This article explores the importance of this indicator, its functionalities, and how it contributes to effective pipe maintenance.
Understanding PE Pipe Wall Damage
Common Causes of Damage
PE pipes can experience wall damage due to several factors, including:
- External Impacts: Heavy equipment, accidental impacts, or improper handling during installation.
- Environmental Conditions: UV exposure, extreme temperatures, and soil movements.
- Chemical Exposure: Contact with harsh chemicals or pollutants.
- Wear and Tear: Long-term use leading to degradation of the pipe material.
Signs of Wall Damage
Damage to the pipe wall can manifest in various ways:
- Cracks or Splits: Visible fractures on the pipe surface.
- Deformation: Bending or warping of the pipe.
- Discoloration: Changes in color indicating potential chemical or environmental damage.
What is a PE Pipe Wall Damage Indicator?
Definition and Purpose
A PE Pipe Wall Damage Indicator is a specialized device or tool used to detect and evaluate damage to the walls of polyethylene pipes. Its primary purposes include:
- Early Detection: Identifying potential issues before they lead to significant failures.
- Assessment: Evaluating the severity of the damage to determine appropriate remedial actions.
- Maintenance Planning: Assisting in the development of maintenance and repair strategies.
Types of Damage Indicators
1. Visual Inspection Tools
- Inspection Cameras: High-resolution cameras designed to visually inspect the interior and exterior of pipes.
- Endoscopes: Flexible instruments used to examine pipe walls in detail.
2. Sensor-Based Indicators
- Ultrasonic Sensors: Measure wall thickness and detect irregularities using ultrasonic waves.
- Electromagnetic Sensors: Utilize electromagnetic fields to identify changes in material properties and detect damage.
How PE Pipe Wall Damage Indicators Work
1. Detection Methods
- Ultrasonic Testing: Sends sound waves through the pipe material to measure thickness and detect anomalies.
- Visual Inspection: Provides a direct view of the pipe surface for identifying visible signs of damage.
- Electromagnetic Testing: Measures changes in electromagnetic fields to detect structural inconsistencies.
2. Data Interpretation
- Analysis: Interprets data collected by the indicators to assess the condition of the pipe wall.
- Reporting: Generates reports highlighting areas of concern and recommendations for further action.
Benefits of Using PE Pipe Wall Damage Indicators
1. Early Problem Detection
- Prevention: Identifies issues before they escalate into major failures, reducing the risk of system downtime.
- Cost Savings: Prevents costly repairs and replacements by addressing issues early.
2. Accurate Assessment
- Detailed Analysis: Provides a precise evaluation of the damage, allowing for targeted repairs.
- Improved Decision-Making: Enables informed decisions regarding maintenance and repairs.
3. Enhanced Maintenance Efficiency
- Planning: Facilitates the development of effective maintenance schedules and strategies.
- Resource Management: Optimizes the use of resources and labor by focusing on areas that require attention.
Implementing PE Pipe Wall Damage Indicators
1. Choosing the Right Indicator
- Type: Select an indicator based on the specific needs of your piping system and the nature of potential damage.
- Features: Consider features such as measurement accuracy, data storage, and ease of use.
2. Training and Operation
- Training: Ensure personnel are trained in the proper use of the indicator and data interpretation.
- Operation: Follow manufacturer guidelines for operating the device and conducting inspections.
3. Maintenance and Calibration
- Regular Calibration: Calibrate the indicator regularly to maintain accuracy and reliability.
- Maintenance: Perform routine maintenance on the device to ensure optimal performance.
Conclusion
The PE Pipe Wall Damage Indicator is an essential tool for maintaining the integrity of polyethylene piping systems. By facilitating early detection and accurate assessment of pipe wall damage, this device helps prevent costly failures and ensures the long-term reliability of the system. Whether using visual inspection tools or sensor-based indicators, implementing a damage detection strategy is crucial for effective pipe maintenance and management.
FAQs
1. How does an ultrasonic sensor detect pipe wall damage?
An ultrasonic sensor sends sound waves through the pipe material. It measures the time it takes for the waves to return, providing information on wall thickness and identifying any irregularities or damage.
2. Can visual inspection tools detect internal damage?
Visual inspection tools, such as cameras and endoscopes, primarily detect external damage. For internal damage, more advanced tools like ultrasonic or electromagnetic sensors are required.
3. How often should PE pipes be inspected using a damage indicator?
The frequency of inspections depends on factors such as the pipe’s age, environmental conditions, and risk of damage. Regular inspections are recommended to ensure early detection of potential issues.
4. What should be done if the damage indicator detects a problem?
If a problem is detected, assess the severity of the damage and plan appropriate repairs or replacements. Consult with experts if necessary to determine the best course of action.
5. Are PE Pipe Wall Damage Indicators easy to use?
Most modern indicators are designed for ease of use, but proper training is essential. Follow manufacturer guidelines and ensure operators are familiar with the device’s features and functions.