Introduction: The Growing Importance of Electrofusing in HDPE Pipe Systems
The polyethylene pipe industry continues to innovate, with electrofusing becoming one of the most critical methods for joining High-Density Polyethylene (HDPE) pipes. As a leading process in the installation of HDPE piping systems, electrofusion welding offers several advantages, such as ease of use, reliability, and efficiency. In an effort to further support industry professionals, the Plastics Pipe Institute (PPI) recently released two essential guides for electrofusing HDPE pipe. These guides aim to enhance safety, improve installation practices, and streamline the electrofusion process for a variety of applications, from water distribution to gas transportation.
What is Electrofusion Welding for HDPE Pipes?
In electrofusion, an electric current is applied to specialized fusion couplers to join HDPE pipes and fittings. This process melts the material at the joining interface, creating a solid, permanent bond. The method is particularly valuable in situations where pipe alignment and space constraints make other welding methods challenging.
Key Benefits of Electrofusing HDPE Pipe
- Reliable and Strong Joints: Electrofusion provides a high-quality, uniform weld that can withstand high-pressure conditions.
- Ease of Installation: The process requires minimal tools, making it easy to use on-site and reducing the time and labor involved.
- Flexibility: Electrofusion works well in tight or confined spaces where other methods, such as butt fusion, might be difficult to implement.
- No Need for Special Training: Compared to some other welding methods, general contractors or installers with basic training can more easily learn and perform electrofusion.
As the popularity of HDPE pipes continues to rise, particularly in water and gas distribution systems, the adoption of electrofusion as a reliable joining method is becoming standard practice. PPI’s release of new guides aims to ensure that industry professionals can apply these benefits with greater precision and efficiency.
Overview of the Two New Guides for Electrofusing HDPE Pipe
The two newly released guides by PPI provide comprehensive information on electrofusing HDPE pipes, targeting both new users and experienced professionals. These resources focus on installation best practices, safety protocols, and material compatibility, helping users achieve optimal performance and longevity for their systems.
Guide 1: Best Practices for Electrofusion Installation
The first guide focuses on best practices for electrofusion installation. It guides you through everything from preparation to testing and inspection, ensuring you complete every step of the process correctly. Proper installation is crucial to the performance and durability of the joint. The guide emphasizes the following key points:
- Pipe Preparation: Properly cleaning the pipe ends before fusion is critical. Dirt, oil, or moisture can prevent a solid bond from forming. The guide includes recommended cleaning methods and tools.
- Correct Fitting Selection: Choosing the right electrofusion coupler and fitting is essential to ensure compatibility with the pipe and its intended use. The guide provides detailed specifications for selecting the appropriate fittings based on pipe size and material type.
- Temperature Control: Temperature plays a crucial role in the electrofusion process. The guide discusses the importance of maintaining consistent heating, ensuring that the heating element reaches the optimal temperature for fusion without overheating.
- Fusion Time: Electrofusion requires precise control of fusion time. The guide outlines the recommended fusion times based on the pipe size, material, and coupling specifications.
By following the best practices outlined in this guide, installers can ensure that each electrofusion joint will be strong, leak-free, and durable.
Guide 2: Safety Protocols and Troubleshooting for Electrofusing HDPE Pipe Systems
The second guide is dedicated to safety protocols and troubleshooting. As with any type of welding or fusion process, safety is paramount. This guide addresses potential hazards, provides safety tips, and offers solutions to common problems that can arise during electrofusion installation.
- Safety Precautions: The guide highlights the importance of using proper personal protective equipment (PPE), such as gloves and eye protection, to safeguard against heat exposure. It also discusses the safe handling of electrical equipment used during electrofusion.
- Electrical Safety: Given that electrofusion involves high electrical current, the guide explains the precautions to take to avoid electrical hazards.
- Troubleshooting Common Issues: The guide covers common issues that can occur during the electrofusion process, such as poor fusion results, misalignment of pipes, or faulty connections. It offers practical troubleshooting steps to rectify these issues and improve the quality of the joint.
- Maintenance Tips: Regular maintenance of electrofusion machines and equipment is essential for consistent results. The guide includes tips for cleaning and maintaining fusion machines, as well as how to store them when not in use.
This second guide is an invaluable resource for ensuring the electrofusion process is performed safely and that any challenges are addressed swiftly.
How Electrofusion Improves HDPE Pipe Systems
Electrofusion welding has a range of benefits that enhance the performance of HDPE piping systems. This method ensures stronger, longer-lasting connections that can better withstand the stress of water, gas, and other utilities. Additionally, the ability to join pipes without the need for large, complex machinery makes electrofusion an attractive solution for challenging installations.
Improved Joint Strength and Durability
One of the most significant advantages of electrofusing HDPE pipes is the strength of the joint. The fusion process creates a bond that is just as strong as the surrounding pipe material, eliminating the weak points that can occur with threaded, bolted, or glued joints. This contributes to fewer leaks and less maintenance over the lifetime of the system.
Faster and More Efficient Installations
Electrofusion allows for quicker installation of pipe joints compared to other methods. This efficiency makes electrofusion ideal for large-scale infrastructure projects, where time is a critical factor.
Versatility in Pipe Sizes and Applications
This versatility enables the use of electrofusion in various settings, from urban water distribution systems to remote gas pipelines. The process also accommodates other plastic piping materials, such as polypropylene, which further expands its range of applications.
Minimizing Environmental Impact
HDPE pipes are known for their environmental benefits, including being lightweight, recyclable, and resistant to environmental degradation. Electrofusion helps maximize these benefits by ensuring a reliable, leak-free connection without the need for additional sealing materials, which can degrade over time.
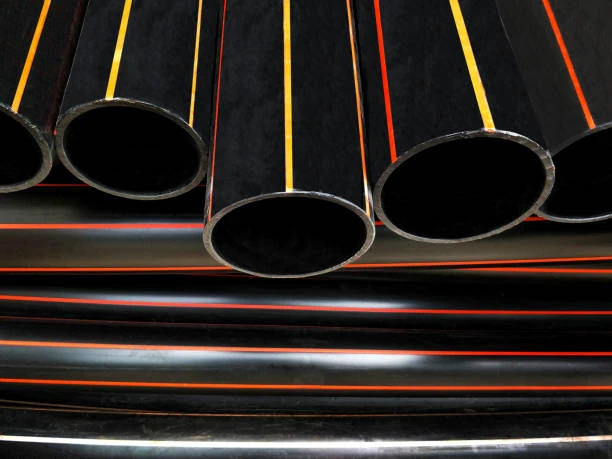
Key Applications for Electrofusing HDPE Pipe
Electrofusion is used in many industries where HDPE piping is required. Some of the most common applications include:
1. Water Distribution Systems
Electrofusion is widely used in municipal water systems due to its ability to create reliable and long-lasting connections in underground pipes. The process ensures that joints can withstand water pressure and environmental conditions.
2. Gas Pipelines
For gas distribution systems, electrofusion provides a secure method for connecting pipes that will transport natural gas. Given the high pressures and potential hazards of gas systems, strong and durable joints are essential.
3. Industrial Applications
Industries such as petrochemicals, food processing, and pharmaceuticals benefit from the reliability of electrofused HDPE pipes.
4. Mining Operations
Mining companies use electrofused HDPE pipes to transport water, chemicals, and slurry through harsh environments. The ability to fuse pipes in difficult-to-reach locations makes electrofusion an ideal solution for remote or rugged areas.
Conclusion: The Role of Electrofusing HDPE Pipe Technology
The release of the two PPI guides on electrofusing HDPE pipe reflects the growing importance of this joining method in modern infrastructure projects. Electrofusion offers numerous benefits, including faster installations, stronger joints, and improved efficiency. As more industries turn to HDPE pipes for water, gas, and industrial applications, the need for proper training and safety measures becomes more critical.
By embracing new technologies like electrofusion, the pipe market can address the challenges of aging infrastructure and pave the way for more reliable, durable, and sustainable piping systems.
Frequently Asked Questions (FAQs)
- What is electrofusion welding for HDPE pipes?
In electrofusion, you join HDPE pipes by applying electrical current to a fitting with built-in heating elements, which fuse the pipes together. - What are the advantages of electrofusing HDPE pipes?
Electrofusion provides strong, durable, leak-free joints, and is easier to install, requiring fewer tools and less specialized training than other welding methods. - What types of applications use electrofusion for HDPE pipes?
Electrofusion is used in water distribution, gas pipelines, industrial systems, and mining operations, where strong, reliable joints are critical. - How do the new PPI guides help installers of HDPE pipes?
The guides provide best practices, safety protocols, troubleshooting tips, and installation guidelines to help installers achieve high-quality, durable electrofusion joints. - Is electrofusion a safer method compared to other welding techniques?
Yes, electrofusion is considered safer because it controls heating and reduces manual handling of heated surfaces, unlike other fusion methods like butt welding.