PVC pipe fittings play a vital role in plumbing, irrigation, and industrial applications. Injection moulding, a process that shapes plastic by injecting molten material into a mould, is essential for manufacturing these fittings with precision and efficiency. This article explores the injection moulding of PVC pipe fittings, focusing on why it’s the preferred method and how it contributes to producing high-quality components.
What are PVC Pipe Fittings?
PVC (polyvinyl chloride) pipe fittings are essential connectors used to join PVC pipes in various plumbing systems. These fittings enable secure connections, changes in direction, and branching within pipe networks. Common applications include potable water systems, waste management, and chemical processing.
Understanding the Injection Moulding Process
Injection moulding is a method where molten plastic material, such as PVC, is injected into a mould. This process forms the material into the desired shape, which solidifies upon cooling. The mould is then opened, and the product is ejected, ready for further processing or assembly. Injection moulding allows for mass production of complex shapes, making it ideal for manufacturing various PVC pipe fittings.
Why Use Injection Moulding for PVC Pipe Fittings?
Injection moulding offers multiple benefits for producing PVC pipe fittings, including:
- High Precision: Injection moulding allows for exact dimensions, critical for fittings that must form tight seals.
- Efficiency: This process enables rapid production, which is ideal for high-demand industries.
- Cost-Effectiveness: Producing large quantities reduces the per-unit cost, making it economical for manufacturers and customers alike.
Materials Used in PVC Pipe Fitting Injection Moulding
The primary material in these fittings is PVC, chosen for its durability, corrosion resistance, and low cost. Manufacturers may add stabilizers, plasticizers, and other additives to enhance the PVC’s strength, flexibility, and heat resistance. These materials ensure that the fittings withstand pressure and temperature changes over time.
Types of PVC Fittings Made by Injection Moulding
Injection moulding can create a range of PVC fittings for various applications. Some common types include:
- Elbows: Allow directional changes in piping.
- Couplings: Connect two pipe segments.
- Tees: Enable three-way junctions for branching.
- Reducers: Connect pipes of different diameters.
Each fitting type serves a unique function within plumbing systems, catering to both residential and industrial needs.
Precision and Quality Control in Injection Moulding
In injection moulding, precision is paramount. Manufacturers implement stringent quality control measures, such as automated inspections and measurements, to ensure each fitting meets exact standards. Consistency is crucial in plumbing systems, as even slight variations can lead to leaks or system failures.
The Role of Mould Design in PVC Fittings Manufacturing
Mould design significantly impacts the quality of the final product. Each fitting type requires a unique mould, precisely crafted to avoid imperfections. Efficient mould design also affects production speed, ensuring that each cycle is quick and reliable. This efficiency translates to lower production costs and fewer defects.
Production Speed and Efficiency Benefits
One of the major benefits of injection moulding is its high-speed production capability. By minimizing production time per unit, manufacturers can meet large orders with ease, making the process both efficient and scalable.
Environmental and Economic Benefits of Injection Moulding
Injection moulding also supports environmental goals by reducing material waste. By optimizing each cycle, manufacturers reduce the need for excess material, lowering both costs and environmental impact. Furthermore, injection moulding is energy-efficient, which helps in minimizing the carbon footprint associated with manufacturing.
Challenges in Injection Moulding of PVC Fittings
Injection moulding of PVC does come with challenges:
- Material Sensitivity: PVC requires careful temperature control, as overheating can degrade the material.
- Complex Design Needs: Certain fitting shapes can be challenging to mould, requiring precise mould design and advanced equipment.
To address these issues, manufacturers rely on modern machinery, refined mould designs, and controlled environments to maintain quality.
Technological Innovations in PVC Fitting Injection Moulding
Recent technological advancements have enhanced the injection moulding process. Improved automation, real-time monitoring, and enhanced mould design capabilities allow manufacturers to produce high-quality PVC fittings with greater speed and consistency.
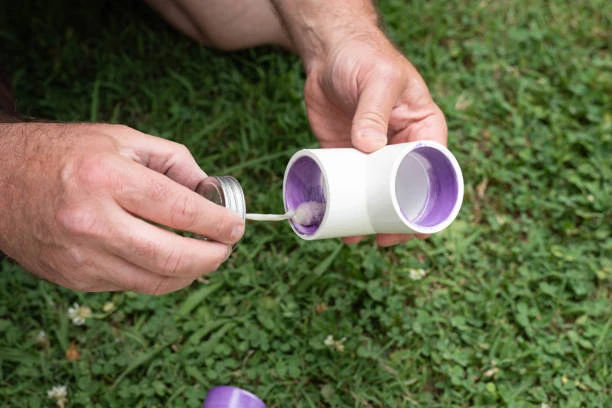
Safety Considerations in Injection Moulding of PVC
PVC emits hazardous fumes at high temperatures, so safety measures are critical. Ventilation systems, protective gear for workers, and strict handling protocols help maintain a safe environment. Safety not only protects workers but also ensures a high-quality product.
Injection Moulding vs. Other Manufacturing Techniques for PVC
Compared to other techniques like extrusion or casting, injection moulding offers superior control over shape and precision. Extrusion is better suited for creating pipes, while injection moulding excels in producing intricate fittings that require detailed mould designs.
Conclusion
Injection moulding has become the leading method for manufacturing PVC pipe fittings, combining efficiency, cost-effectiveness, and precision. While challenges exist, technological advancements continue to improve the process, making it an excellent choice for producing high-quality PVC fittings used in various applications.
FAQs
- Why is injection moulding used for PVC fittings?
Injection moulding ensures precision, high-speed production, and cost-effectiveness. - What materials are needed in PVC fitting moulding?
PVC is the primary material, with added stabilizers for durability and heat resistance. - Are injection-moulded PVC fittings safe for plumbing?
Yes, they are durable, resistant to corrosion, and ideal for various plumbing needs. - What are the main types of PVC fittings produced?
Common types include elbows, tees, reducers, and couplings. - Can injection moulding reduce PVC waste?
Yes, the process optimizes material use, reducing waste and production costs.