Introduction
HDPE compression fittings have revolutionized the piping industry with their exceptional durability, ease of installation, and adaptability across various applications. These fittings provide a reliable and efficient solution for connecting HDPE pipes without the need for welding or adhesives. From agricultural irrigation to large municipal water systems, HDPE compression fitting have become the go-to option for modern piping solutions.
What Are HDPE Compression Fitting?
HDPE compression fitting are a type of pipe fitting used to connect HDPE pipes. They are composed of several components that include a body, O-rings, and tightening nuts. These fittings function by compressing the pipe against the fitting to create a secure and leak-proof connection. The key reason for their popularity is their ease of use, eliminating the need for complex tools and techniques.
Why Are They Used?
HDPE compression fitting are used for their reliability, quick installation process, and ability to handle high-pressure systems. This makes them an excellent choice for various applications, such as water supply lines, sewage systems, and gas pipelines.
The Structure of HDPE Compression Fitting
The core components of HDPE compression fitting include:
- Body: The main part that houses the pipe.
- O-rings: These ensure a watertight seal between the pipe and the fitting.
- Nuts: Tighten the components, compressing the pipe into the fitting to create a solid joint.
These components work in synergy to ensure a strong, leak-free connection between pipes.
Advantages of Using HDPE Compression Fitting
HDPE compression fitting offer several key advantages:
1. Durability and Strength
HDPE is known for its high strength-to-density ratio, making it durable enough to withstand various environmental conditions without cracking or breaking.
2. Ease of Installation
Unlike traditional metal fitting, HDPE compression fitting don’t require welding or adhesives, making the installation process faster and easier. This reduces labor costs and installation time significantly.
3. Corrosion Resistance
One of the biggest benefits of HDPE compression fitting is their resistance to corrosion. This makes them ideal for underground and water-based applications where metal fittings would degrade over time.
4. Leak-Proof Properties
The compression mechanism ensures a tight seal, preventing leaks and minimizing water loss, which is critical for efficient system operation.
Types of HDPE Compression Fittings
HDPE compression fitting come in various forms to suit different piping configurations:
- Couplings: Used to connect two pipes in a straight line.
- Elbows: Allow for changes in direction.
- Tees: Facilitate branching of pipes.
- Valves: Control the flow of liquids or gases through the system.
Applications of HDPE Compression Fittings
HDPE compression fitting are versatile and used in a wide range of industries, including:
1. Agricultural Irrigation
Farmers rely on HDPE compression fitting for efficient water delivery systems in crop irrigation.
2. Municipal Water Distribution
These fittings are a key component in the reliable delivery of clean water to homes and businesses.
3. Industrial Piping Systems
Factories and industrial plants use HDPE compression fitting for transporting liquids and gases in high-pressure systems.
Installation Process of HDPE Compression Fitting
Tools Required
- Pipe cutters
- Wrench
- Lubricant (optional)
Step-by-Step Installation Guide
- Cut the HDPE pipe to the desired length.
- Clean the pipe ends to remove any dirt.
- Insert the pipe into the fitting body.
- Tighten the nuts to secure the connection.
By following these steps, you can ensure a strong and leak-free installation.
Maintenance of HDPE Compression Fittings
Regular inspection and maintenance will extend the lifespan of your HDPE compression fitting. This includes:
- Checking for leaks.
- Tightening the nuts as needed.
- Replacing worn-out O-rings.
Comparison of HDPE Compression Fittings with Other Fittings
Metal Fittings
- Pros: High strength, suitable for high-temperature applications.
- Cons: Susceptible to corrosion.
PVC Fittings
- Pros: Affordable, easy to install.
- Cons: Lower strength compared to HDPE, can become brittle.
HDPE compression fittings strike a balance between strength and flexibility, making them a preferred choice for many applications.
Environmental Impact of HDPE Compression Fittings
HDPE compression fitting are eco-friendly, as they are recyclable and require less energy to manufacture compared to metal fitting. Their durability also reduces the need for frequent replacements, minimizing waste.
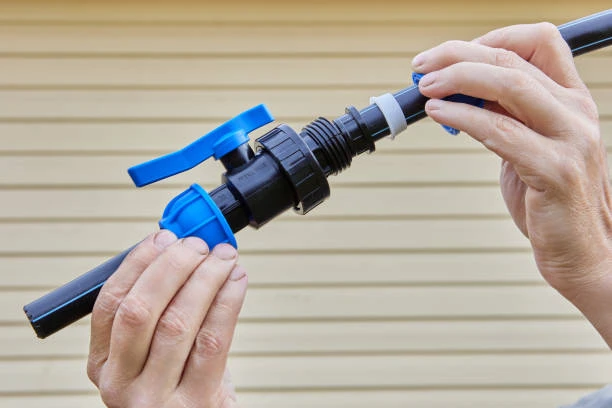
Common Issues and Troubleshooting with HDPE Compression Fitting
- Leaks: Often due to improper tightening or damaged O-rings.
- Improper Installation: Ensuring proper alignment and tightness is crucial.
- Wear and Tear: Regular maintenance can help mitigate wear-related issues.
Market Trends and Innovations in HDPE Compression Fitting
The HDPE compression fitting market continues to evolve with innovations in materials and design, improving durability and installation efficiency. The global demand is growing as industries seek cost-effective and sustainable piping solutions.
Cost Effectiveness of HDPE Compression Fittings
While HDPE compression fitting may have a higher initial cost than some alternatives, their durability, ease of installation, and low maintenance requirements make them more cost-effective in the long run.
Industry Standards and Certifications for HDPE Compression Fitting
HDPE compression fitting must meet industry standards such as ISO certification to ensure their quality and safety for use in critical applications like water supply systems.
Conclusion
HDPE compression fittings provide a versatile, durable, and cost-effective solution for modern piping needs. Their ease of installation, resistance to corrosion, and environmentally friendly characteristics make them a preferred choice for various industries. With ongoing innovations, the future looks promising for HDPE compression fitting as they continue to play a pivotal role in piping systems worldwide.
FAQs
- What are HDPE compression fitting used for?
They are used to connect HDPE pipes in water, gas, and industrial piping systems. - Are HDPE compression fitting durable?
Yes, HDPE fittings are highly durable and resistant to corrosion, making them ideal for long-term use. - Can I install HDPE compression fitting myself?
Yes, they are designed for easy installation without the need for specialized tools or welding. - Are HDPE compression fitting eco-friendly?
Yes, HDPE fittings are recyclable and have a lower environmental impact compared to metal fittings. - What industries use HDPE compression fitting?
These fittings are commonly used in agriculture, municipal water systems, and industrial piping networks.