Introduction: The Importance of Proper Preparation in Socket Fusion
Socket fusion, a technique widely used in joining Polypropylene Random PPR pipes and fittings, demands meticulous preparation to ensure leak-free connections and long-term system integrity. This guide serves as a comprehensive roadmap for anyone involved in the installation or maintenance of PPR piping systems, emphasizing the critical steps and best practices for preparing PPR pipe and fittings prior to socket fusion.
Material Selection and Inspection
Before beginning the preparation process, it is essential to select high-quality PPR pipes and fittings that meet or exceed industry standards. Inspect each piece for cracks, scratches, or contamination that could compromise the fusion bond. Ensure that the pipes and fittings are compatible in terms of material composition, size, and pressure rating. Additionally, check the manufacturer’s recommendations for the specific type of socket fusion equipment required, as different brands and models may have varying operational parameters.
Surface Preparation: Cleaning and Chamfering
Surface preparation is critical for achieving a strong, uniform fusion bond. Begin by cleaning the ends of the pipes and the socket ends of the fittings thoroughly using a suitable solvent cleaner. This removes any dirt, grease, or debris that could interfere with the fusion process. Once clean, chamfer the outer edge of the pipe end at a 15-degree angle using a chamfering tool. This preparation ensures that the melted material flows smoothly into the fitting, creating a robust joint.
Heating the Pipe and Fitting: Temperature and Timing
The next step involves heating the prepared ends of the pipe and the socket of the fitting to their respective fusion temperatures. Use a socket fusion machine that allows for precise temperature control and consistent heating. Follow the manufacturer’s guidelines for the specific materials being fused, as the optimal temperature can vary. Typically, PPR materials require temperatures ranging from 260°C to 290°C. Once the desired temperature is reached, maintain it for the recommended dwell time, ensuring that the entire surfaces are uniformly heated.
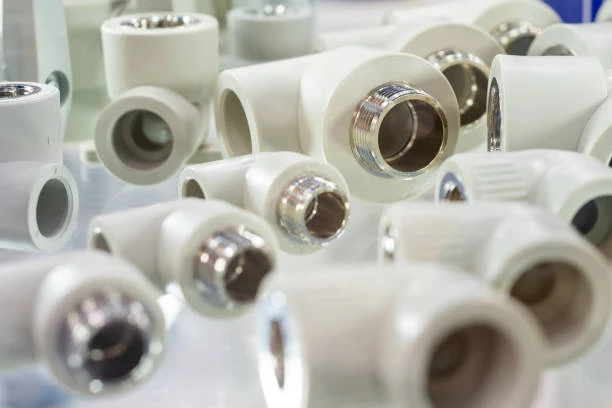
Preparing the PPR Pipes and Fittings
1 Cutting the Pipes
Accurate cutting is crucial for a successful socket fusion joint. Use a sharp, high-quality pipe cutter or saw to cut the pipes to the desired length. Ensure that the cut is straight and perpendicular to the pipe’s axis to avoid any irregularities that could compromise the fusion.
2 Deburring the Cut Ends
After cutting, use a deburring tool to remove any sharp edges or burrs from the pipe ends. A smooth, debris-free surface is essential for achieving a strong, leak-free joint.
3 Cleaning the Surfaces
Clean the pipe and fitting surfaces thoroughly using a clean cloth or a suitable solvent. Remove any dirt, grease, or debris that could interfere with the fusion process. Ensure that the surfaces are dry before proceeding to the next step.
Socket Fusion Process: Insertion and Cooling
With the pipe and fitting ends properly heated, quickly but carefully insert the pipe into the fitting socket. Apply firm, steady pressure to ensure that the surfaces are in full contact. The melted materials will begin to flow and fuse together. Maintain this pressure for the recommended fusion time, which can vary based on pipe size and material thickness.
After fusion, allow the joint to cool naturally for several minutes without disturbing it. This cooling period is crucial for the material to solidify and achieve full strength.
Post-Fusion Inspection and Testing
Once cooled, inspect the fused joint visually for any signs of imperfections such as bubbles, discoloration, or incomplete fusion. Use a suitable gauge to check the joint for alignment and tightness. Additionally, perform pressure testing on the completed piping system to verify its integrity. This final step ensures that the PPR piping system is ready for safe, reliable operation.
Conclusion: Ensuring Success with Proper Preparation
Socket fusion of PPR pipes and fittings is a precise and critical process that requires meticulous preparation, execution, and inspection. By following these comprehensive guidelines, installers can achieve strong, durable connections that meet the highest standards of performance and reliability.
Proper preparation is the cornerstone of successful socket fusion, ensuring that PPR piping systems operate efficiently and safely for years to come.
FAQ
Q: Can I use PPR pipes and fittings for outdoor applications?
A: UV-stabilized versions of PPR are available for outdoor use, which offer better resistance to sunlight degradation.
Q: What is the maximum operating temperature for PPR pipes?
A: The maximum operating temperature for PPR pipes depends on the specific grade and manufacturer. Typically, PPR pipes can withstand temperatures up to 95°C (203°F) for hot water systems and lower temperatures for cold water applications.
Q: Can I use PPR pipes and fittings with other types of piping materials?
Yes, PPR pipes and fittings can be used in conjunction with other piping materials, such as copper or PEX, through the use of suitable transition fittings. However, it’s important to follow the manufacturer’s guidelines and local building codes when making such connections.
Q: How can I prevent bubbles or imperfections in my socket fusion joints?
Additionally, maintaining the correct temperature and heating time during the fusion process is crucial. Always follow the manufacturer’s instructions carefully and use high-quality tools and equipment.