Introduction
The construction industry constantly evolves with advancements that enhance efficiency, reduce costs, and improve reliability. PVC water fittings have long been a cornerstone of plumbing and piping systems, known for their durability and adaptability. The introduction of 3D-printed corner connectors is a game-changer, offering customized solutions to complex piping systems. This article explores the intersection of 3D printing technology and PVC water fittings, focusing on how it redefines construction practices.
What Are PVC Water Fittings?
Definition and Applications
PVC water fittings connect and manage the flow of water through piping systems. Their applications range from residential plumbing to large-scale industrial projects.
Key Features of PVC Water Fittings
- Durability: Resistant to corrosion and wear, PVC fittings withstand harsh conditions.
- Cost-Effectiveness: Affordable compared to metal counterparts while delivering excellent performance.
- Versatility: Available in various designs to meet diverse construction needs.
The Role of Corner Connectors in PVC Water Fittings
Structural Integrity
Corner connectors provide crucial support in turning points of piping systems, maintaining stability and flow.
Enhancing Pipe Network Flexibility
These connectors enable intricate layouts, adapting to the unique demands of each project.
Supporting Complex Systems
In large-scale installations, corner connectors are vital for ensuring the efficient and seamless operation of water systems.
Introduction to 3D Printing Technology
Basics of 3D Printing
3D printing, or additive manufacturing, builds objects layer by layer using digital designs. This method offers high precision and flexibility.
Benefits of 3D Printing in Construction
- Customization: Tailored solutions for unique project requirements.
- Efficiency: Faster production times reduce delays.
- Cost Savings: Minimal waste and optimized material usage.
3D Printed Corner Connectors in PVC Water Fittings
Advantages Over Traditional Connectors
- Customizability: Easily modified to fit specific designs, improving project accuracy.
- Faster Production: Reduced lead times accelerate project completion.
- Reduced Costs: Lower material waste translates to cost savings.
Enhancing Performance and Reliability
3D-printed connectors integrate better with piping systems, enhancing flow efficiency and structural robustness.
Case Studies of Successful Implementation
Several projects worldwide have adopted 3D-printed PVC components, achieving improved system performance and reduced costs.
Impacts on Construction Industry
Streamlining PVC Fitting Assemblies
3D printing simplifies the production of corner connectors, speeding up the assembly process in construction projects.
Promoting Sustainability
The additive manufacturing process minimizes material waste, contributing to eco-friendly construction practices.
Driving Innovation in Plumbing Systems
By integrating 3D-printed components, construction professionals can design more innovative and efficient plumbing systems.
Challenges and Limitations
Material Constraints
The materials suitable for 3D printing must match the durability and chemical resistance of traditional PVC fittings.
Cost of 3D Printers
High upfront costs for 3D printing equipment can limit accessibility for smaller businesses.
Standardization Issues
Ensuring consistency and adherence to industry standards remains a challenge for widespread adoption.
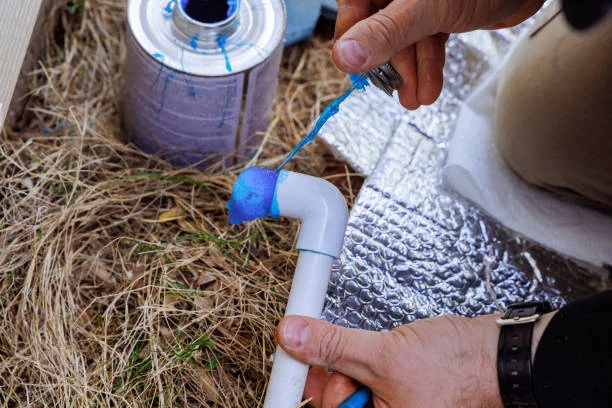
Future of 3D Printing in PVC Water Fittings
Innovations in Materials for 3D Printing
Researchers focus on developing materials that combine the properties of PVC with the flexibility of 3D printing.
Automating Manufacturing Processes
Automation will further reduce production times and costs, making the technology more accessible.
Global Adoption Trends
As awareness and technology spread, more construction projects will integrate 3D-printed PVC components.
Conclusion
The advent of 3D-printed corner connectors marks a significant leap in the construction industry. These innovations in PVC water fittings streamline processes, promote sustainability, and enhance system performance. As the technology matures, it will pave the way for more efficient and environmentally friendly construction practices.
FAQs
1. How do 3D-printed connectors improve PVC water fittings?
They offer tailored solutions, faster production, and enhanced integration with piping systems.
2. Are 3D-printed PVC fittings more durable than traditional ones?
Yes, they can be engineered for higher precision and better material performance.
3. What are the environmental benefits of 3D-printed PVC components?
The process reduces waste, conserving resources and lowering environmental impact.
4. Is 3D printing technology accessible to small construction businesses?
While initial costs are high, growing competition and innovations are making it more affordable.
5. What are the common materials used in 3D-printed PVC fittings?
Materials include PVC-based composites and other polymers engineered for durability and flexibility.