Introduction
In plumbing and industrial systems, fittings are crucial for connecting pipes and ensuring efficient operation. Among the many options available, PPR brass fittings have gained popularity for their durability and adaptability. But what happens when you enhance them with perforated aluminum? This innovation combines the strength of brass, the flexibility of PPR, and the lightweight nature of aluminum, creating a game-changer in the fittings market. Let’s explore what makes perforated aluminum PPR brass fittings unique and their role in modern systems.
Understanding PPR Brass Fittings
What Are PPR Brass Fitting?
PPR brass fittings are components used to connect pipes in plumbing systems. They feature a brass core for strength and PPR (Polypropylene Random Copolymer) for flexibility and thermal resistance.
Common Uses and Benefits
These fittings are widely used in residential plumbing, industrial pipelines, and HVAC systems, offering durability, corrosion resistance, and compatibility with various materials.
The Role of Perforated Aluminum in PPR Brass Fitting
What is Perforated Aluminum?
Perforated aluminum is a sheet or tube of aluminum with holes evenly distributed across its surface. This design reduces weight without compromising strength and adds unique features like heat dissipation and airflow.
Why Integrate It With PPR Brass Fitting?
Incorporating perforated aluminum in PPR brass fittings enhances their functionality, providing a lightweight and thermally efficient solution. It improves the fitting’s ability to handle temperature fluctuations and reduces the overall weight of the system.
Key Benefits of Perforated Aluminum PPR Brass Fitting
Lightweight Design
The perforations in aluminum reduce the overall weight of the fittings, making transportation and installation easier.
Enhanced Durability
Combining brass, PPR, and perforated aluminum results in a fitting that can withstand high pressure and temperatures.
Improved Heat Dissipation
The perforated design allows better airflow, helping to dissipate heat more effectively, especially in systems that handle hot fluids.
Applications of Perforated Aluminum PPR Brass Fitting
Residential Plumbing
These fittings ensure efficient water supply and waste management in homes, offering a reliable solution for hot and cold water systems.
Industrial Pipelines
In industries, these fittings are used for transporting chemicals, gases, and water due to their resistance to corrosion and temperature changes.
Specialized Systems
Perforated aluminum PPR brass fittings are ideal for HVAC systems and specialized setups requiring temperature and pressure stability.
How They Differ From Standard PPR Brass Fitting
The inclusion of perforated aluminum enhances thermal efficiency and reduces weight, setting them apart from standard PPR brass fittings, which may lack these advantages.
Material Composition and Manufacturing
Key Materials Used
The fittings are crafted from high-quality brass, PPR, and perforated aluminum, each contributing to their unique properties.
Manufacturing Process Overview
The manufacturing process involves precision molding of PPR, incorporation of brass components, and integration of perforated aluminum for added benefits.
Environmental Advantages
Sustainability of Aluminum
Aluminum is a sustainable material, often recycled without losing its properties, making these fittings an eco-friendly choice.
Longevity and Recyclability
These fittings offer a long service life and can be recycled at the end of their use, reducing waste and environmental impact.
Challenges and Limitations
Potential Drawbacks
While these fittings are innovative, they may have a higher initial cost and require specialized installation tools.
How to Mitigate Issues
Choosing certified products and following proper installation techniques can address most challenges.
Choosing the Right Perforated Aluminum PPR Brass Fittings
Key Factors to Consider
Evaluate system requirements, such as pressure and temperature ratings, before selecting fittings.
Understanding Certifications and Standards
Look for products certified by relevant industry standards to ensure safety and performance.
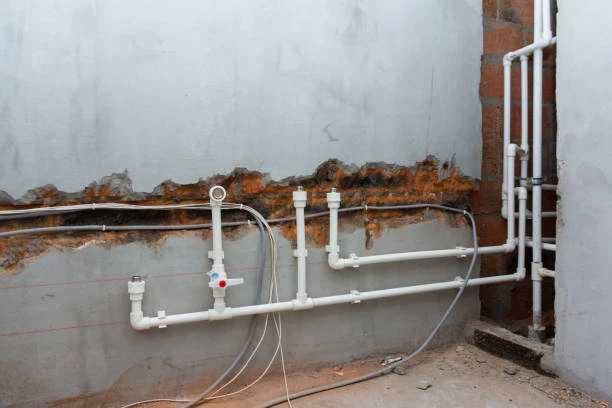
Installation Best Practices
- Cut the pipe to the required length.
- Clean the pipe ends thoroughly.
- Align the fitting and pipe properly.
- Use the appropriate welding or connection tools.
- Test the system for leaks after installation.
Maintenance Tips
- Inspect fittings regularly for wear or damage.
- Clean the system to prevent blockages.
- Replace worn components promptly to maintain efficiency.
Innovations in Perforated Aluminum PPR Brass Fittings
Advancements in manufacturing are introducing more efficient designs and materials, making these fittings even more versatile and durable.
Comparison with Alternative Materials
Perforated Aluminum vs. Solid Aluminum Fittings
Perforated aluminum offers better heat dissipation and a lightweight design compared to solid aluminum.
PPR Brass Fittings vs. Plastic-Only Fittings
The addition of brass and aluminum enhances strength and thermal resistance, outperforming plastic-only fittings.
Conclusion
Perforated aluminum PPR brass fittings represent a significant innovation in plumbing and industrial systems. Their unique combination of materials offers unmatched durability, thermal efficiency, and environmental benefits. By understanding their features and applications, you can make informed decisions for your projects.
FAQs
1. What makes perforated aluminum PPR brass fittings unique?
They combine the strength of brass, the flexibility of PPR, and the lightweight, thermally efficient properties of perforated aluminum.
2. Are these fittings suitable for industrial applications?
Yes, they are ideal for transporting chemicals, gases, and water in industrial systems.
3. How do perforated aluminum PPR brass fittings improve thermal efficiency?
The perforations in aluminum enhance airflow and heat dissipation, maintaining system stability.
4. Can these fittings be recycled?
Yes, both the aluminum and brass components are recyclable, making them environmentally friendly.
5. Are they cost-effective despite their advanced features?
While the initial cost may be higher, their durability and low maintenance needs make them cost-effective in the long run.