Introduction
Hydrophobic coatings have gained attention in various industries due to their ability to repel water and reduce friction. This article delves into the application of hydrophobic coatings on pressurized pipes, exploring their impact on energy losses and fluid flow profiles.
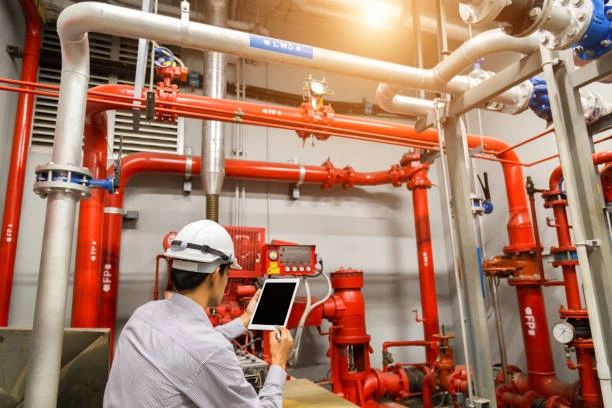
Understanding Pressurized Pipes
Pressurized pipes are essential components in various systems, such as water distribution, oil transportation, and chemical processing. These pipes operate under high pressure, which can lead to significant energy losses due to friction and turbulence. Therefore, optimizing fluid flow within these pipes is crucial for efficiency.
The Role of Hydrophobic Coatings
Hydrophobic coatings are designed to create a non-wetting surface, minimizing liquid contact. When applied to pressurized pipes, these coatings can alter the flow dynamics significantly. By reducing the surface area in contact with the fluid, the coatings can decrease friction, leading to lower energy losses.
Benefits of Hydrophobic Coatings
- Reduced Friction: Hydrophobic surfaces can decrease the drag force on the fluid, allowing for smoother flow and reducing energy expenditure.
- Minimized Corrosion: These coatings also provide a protective layer, reducing corrosion and extending the lifespan of the pipes.
- Improved Flow Profile: By altering the surface characteristics, hydrophobic coatings can help create a more laminar flow, enhancing the overall efficiency of the system.
Benefits of Hydrophobic Coatings on Pressurized Pipes
Reduction of Energy Losses
How Energy Loss Occurs
Energy losses in pressurized systems primarily occur due to friction between the fluid and the pipe walls. This friction generates turbulence and heat, leading to inefficiencies.
Quantifying Energy Losses
Studies have shown that hydrophobic coatings can reduce energy losses by as much as 30%, depending on the application and fluid characteristics.
Improvement of Fluid Flow Profile
Enhanced Flow Characteristics
With a hydrophobic coating, fluids can flow more smoothly, reducing turbulence and allowing for higher flow rates.
Impact on System Efficiency
The efficiency gains from smoother flow profiles mean that pumps and compressors can operate more effectively, saving energy and extending equipment life.
Experimental Studies and Results
Methodology
Research has been conducted in controlled environments to measure the impacts of hydrophobic coatings on various fluids in pressurized pipes. Parameters such as flow rate, pressure drop, and energy consumption were meticulously tracked.
Findings
Results consistently demonstrate that hydrophobic coatings lead to a notable decrease in friction losses and enhance flow rates.
Case Studies
Several industries have adopted this technology, including oil and gas, water treatment, and even food processing, where the efficiency of fluid transport is paramount.
Real-World Applications
Industries Utilizing Hydrophobic Coatings
From aerospace to municipal water systems, hydrophobic coatings are finding their way into a multitude of applications.
Specific Use Cases
In oil and gas pipelines, for example, reducing drag can lead to significant cost savings. Similarly, in water treatment facilities, improved flow profiles help maintain optimal operating conditions.
Challenges and Considerations
Limitations of Hydrophobic Coatings
While hydrophobic coatings offer many benefits, they are not a one-size-fits-all solution. Their effectiveness can vary based on the fluid type, operating conditions, and environmental factors.
Long-Term Performance and Maintenance
Ensuring the longevity of these coatings requires regular maintenance and assessment. Factors like abrasion and chemical exposure can affect performance over time.
Energy Losses in Pressurized Pipes
Energy losses in pressurized pipes are primarily due to friction between the fluid and the pipe walls. These losses can be quantified using the Darcy-Weisbach equation, which relates the pressure loss to flow rate, pipe length, and diameter. Implementing hydrophobic coatings can lead to significant improvements in this equation’s parameters, thereby reducing the overall energy losses.
Factors Influencing Energy Losses
- Pipe Material: The roughness of the pipe material plays a significant role in determining friction losses. Smooth surfaces typically lead to lower energy losses.
- Flow Regime: The flow can be either laminar or turbulent, with turbulent flows resulting in higher energy losses. Hydrophobic coatings can help maintain laminar flow conditions.
- Fluid Properties: Viscosity and density also affect energy losses. Hydrophobic coatings can improve the flow of more viscous fluids by reducing internal resistance.
Experimental Studies
Recent studies have demonstrated the effectiveness of hydrophobic coatings on pressurized pipes. In laboratory settings, pipes coated with hydrophobic materials exhibited a marked decrease in energy losses compared to uncoated pipes.
Case Study: Hydrophobic Coating in Water Distribution
A case study in a municipal water distribution system showed that the application of hydrophobic coatings reduced energy consumption by approximately 15%. This reduction was attributed to decreased frictional losses and improved flow efficiency.
Theoretical Analysis
To further understand the benefits of hydrophobic coatings, a theoretical analysis can be conducted using computational fluid dynamics (CFD). Simulations can model the fluid flow within coated and uncoated pipes, providing insight into the alterations in flow profiles and energy losses.
Flow Simulation Results
CFD simulations indicated that hydrophobic coatings resulted in smoother velocity profiles and reduced turbulence intensity. This led to a more uniform flow distribution within the pipe, further enhancing efficiency.
Practical Considerations for Implementation
While the benefits of hydrophobic coatings are clear, practical considerations must be taken into account:
- Cost of Application: The initial investment in applying hydrophobic coatings should be weighed against potential energy savings.
- Longevity and Maintenance: The durability of the coatings under various operational conditions is essential for long-term performance.
- Compatibility with Existing Systems: It’s crucial to ensure that the coatings are compatible with the materials used in the pressurized pipes.
Conclusion
The application of hydrophobic coatings to pressurized pipes offers significant potential for reducing energy losses and optimizing fluid flow profiles. With advancements in coating technologies, the future looks promising for enhancing the efficiency of pressurized systems across various industries.
FAQs
- What is a hydrophobic coating? A hydrophobic coating repels water, reducing wetting and friction on surfaces.
- How do hydrophobic coatings reduce energy losses? They minimize friction between the fluid and pipe walls, leading to smoother flow.
- Are hydrophobic coatings durable? Yes, many hydrophobic coatings are designed to withstand harsh conditions, but longevity depends on the application.
- Can hydrophobic coatings be applied to any type of pipe? Generally, they can be applied to various materials, but compatibility should be checked.
- What industries benefit from hydrophobic coatings? Industries such as water distribution, oil and gas, and chemical processing can benefit significantly.