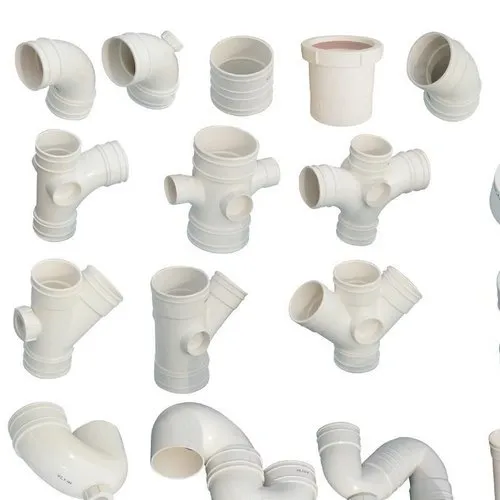
PVC pipe fittings are essential components in various plumbing and construction applications. They play a crucial role in ensuring efficient fluid transport, and the quality of these fittings largely depends on the moulds used in their production. In this article, we will explore the intricacies of PVC pipe fittings moulds, their manufacturing process, and the innovations shaping their future.
Types of PVC Pipe Fittings
PVC pipe fittings come in various shapes and sizes, each designed for specific functions. Common fittings include:
- Elbows: Used to change the direction of the pipe.
- Tees: Allow for branching off in a plumbing system.
- Couplings: Connect two pipes together.
Specialty fittings may include reducers, caps, and adapters, all designed to meet specific application requirements.
The Role of Moulds in PVC Fitting Production
Moulds are the backbone of PVC fitting manufacturing. They shape the raw material into the desired forms and ensure that each fitting meets stringent quality standards.
- Mould Design and Function: The design of a mould directly influences the quality and precision of the final product. Well-designed moulds facilitate efficient production and reduce waste.
Manufacturing Process of PVC Fittings
The production of PVC fittings involves several key steps:
- Material Preparation: High-quality PVC resin is mixed with additives.
- Heating and Moulding: The mixture is heated until it becomes pliable, then injected into the mould.
- Cooling and Solidification: After cooling, the PVC hardens into the shape of the mould.
- Finishing Touches: The fittings undergo trimming and inspection to ensure they meet specifications.
Precision in moulding is critical; any deviation can lead to defects in the fittings.
Quality Control in Mould Production
Ensuring high-quality moulds is vital for producing reliable PVC fittings:
- Testing and Inspection Standards: Regular inspections during the mould production process help identify any flaws early on.
- Ensuring Consistency and Durability: Manufacturers employ rigorous testing methods to ensure that moulds produce consistent results and can withstand repeated use.
Innovations in Mould Design and Technology
The moulding industry is constantly evolving, with innovations driving improvements in efficiency and quality:
- Use of CAD Software in Design: Computer-Aided Design (CAD) software enables manufacturers to create precise mould designs, reducing errors and lead times.
Challenges in Mould Production
While the mould production process is well-established, manufacturers face challenges:
- Strategies to Overcome Challenges: Regular maintenance of moulds and investing in high-quality materials can mitigate many of these issues.
Cost Considerations
Investing in moulds can be substantial, but it’s essential for long-term success:
- Long-term Savings and Efficiency: Well-designed moulds improve production efficiency, reduce waste, and ultimately save money.
Environmental Impact of Mould Production
As environmental concerns grow, manufacturers are increasingly adopting sustainable practices:
- Recycling and Waste Management: Implementing recycling initiatives for scrap material helps minimize waste and environmental impact.
Future Trends in PVC Fitting Moulds
The future of PVC fitting moulds is promising, with several trends emerging:
- Market Demands Shaping Future Designs: The increasing demand for eco-friendly and specialized fittings will influence mould design and production techniques.
Conclusion
Moulds are integral to the PVC pipe fittings manufacturing process, ensuring that the final products meet the highest quality standards. As the industry evolves, ongoing innovations and sustainable practices will play a crucial role in shaping the future of PVC fittings. Manufacturers and consumers alike must prioritize quality in mould design and production to ensure a reliable and efficient plumbing infrastructure.
FAQs
- What materials are used to make PVC pipe fitting moulds? Common materials include steel and aluminum, chosen for their durability.
- How are PVC fittings manufactured? The process involves preparing PVC resin, heating and moulding it, cooling, and finishing.
- What challenges do manufacturers face in mould production? Common challenges include wear and tear of moulds, misalignment, and material defects.
- What innovations are influencing mould design? Technologies like CAD software and advanced moulding techniques are driving improvements.
- How can manufacturers reduce environmental impact? By adopting eco-friendly practices and implementing recycling initiatives.