Introduce PPR Pipe
In the plumbing and construction industry, PPR (Polypropylene Random Copolymer) pipes have become a favored choice due to their excellent durability, corrosion resistance, and versatility. The production of PPR pipes in the 20-63mm diameter range is particularly relevant for various applications, including water supply systems, irrigation, and HVAC. This article will explore the intricacies of the 20-63mm PPR Pipe production line, detailing the manufacturing process, machinery involved, quality control, and market trends.
Understanding PPR Pipe
What Are PPR Pipes?
PPR pipes are made from a thermoplastic polymer, which provides a range of benefits:
- Durability: PPR pipes can last over 50 years under proper conditions.
- Chemical Resistance: They resist a wide variety of chemicals, making them suitable for many applications.
- Temperature Tolerance: PPR pipes can handle temperatures from -20°C to 95°C.
- Eco-Friendly: Made from non-toxic materials, PPR pipes are recyclable.
Applications of 20-63mm PPR Pipes
PPR pipes in the 20-63mm range are widely use in various sectors:
- Residential Plumbing: Ideal for hot and cold water supply.
- Irrigation Systems: Commonly used in agricultural applications.
- HVAC Systems: Suitable for heating and cooling installations.
- Industrial Uses: Effective for transporting chemicals and gases.
The PPR Pipe Production Line
Overview of the Production Process
The production of PPR pipes involves several key stages, from raw material preparation to final quality control. A standard production line for 20-63mm PPR pipes includes the following steps:
- Raw Material Preparation
- Extrusion
- Cooling and Calibration
- Cutting
- Quality Control
- Packaging
Step 1: Raw Material Preparation
The primary raw material for PPR pipes is polypropylene, which is often combined with additives to enhance performance. The following steps are involve in raw material preparation:
- Material Selection: High-quality polypropylene should be sourced, often in the form of pellets.
- Mixing Additives: Depending on the desired properties, additives such as stabilizers, colorants, and antioxidants are mixe with the polypropylene.
- Drying: The materials are drie to eliminate moisture that could affect the extrusion process.
Step 2: Extrusion
Extrusion is the heart of the PPR pipe production line. The process involves the following:
- Feeding: The prepared material is fed into the extruder, where it is heated and melted.
- Screw Mechanism: A rotating screw within the extruder pushes the molten material through a die, shaping it into the desired pipe diameter (20-63mm).
- Die Head: The die head determines the final shape and diameter of the pipe.
Step 3: Cooling and Calibration
After extrusion, the newly formed PPR pipe must be cooled and calibrated:
- Cooling: The pipes are cooled using a water bath or air cooling system to solidify the material.
- Calibration: A calibration unit ensures that the pipe maintains the correct diameter and wall thickness as it cools.
Step 4: Cutting
Once cooled and calibrated, the PPR pipes are cut to the desired lengths. The cutting process includes:
- Automatic Cutting Machine: This machine is programme to cut the pipes at predetermined lengths for efficiency.
- Quality Check: Each cut pipe is checke for uniformity and accuracy.
Step 5: Quality Control
Quality control is essential to ensure the PPR pipes meet industry standards. Key aspects of quality control include:
- Visual Inspection: Checking for surface defects, color consistency, and dimensions.
- Pressure Testing: Pipes are teste under pressure to ensure they can withstand typical operating conditions.
- Sampling: Random samples are take for laboratory testing to check material properties and compliance with standards.
Step 6: Packaging
Finally, the PPR pipes are package for shipment. Packaging is crucial for protecting the pipes during transport. The packaging process includes:
- Bundling: Pipes are bundle together based on length and diameter.
- Labeling: Each bundle is labele with information regarding dimensions, material specifications, and batch numbers.
- Storage: The packaged pipes are store in a controlled environment to prevent damage.
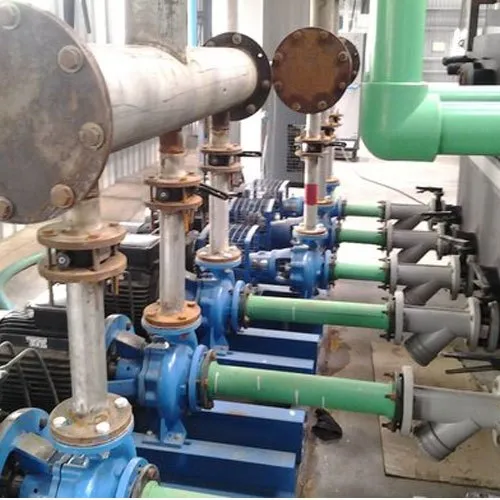
Machinery Used in PPR Pipe Production
The efficiency and quality of the production line heavily depend on the machinery used. Here are some essential machines involve in the production of 20-63mm PPR pipes:
1. Extruder
The extruder is the main machine in the production line. It consists of a hopper, barrel, screw, and die. A high-quality extruder can ensure a consistent flow of material and precise temperature control.
2. Cooling Tank
Cooling tanks are crucial for solidifying the extruded pipes. They can be water-based or air-cooled, depending on the production line’s design.
3. Cutting Machine
Automatic cutting machines enhance efficiency by providing precise and uniform lengths for the pipes.
4. Calibration Equipment
Calibration equipment ensures the pipe maintains its diameter and wall thickness during cooling.
5. Quality Control Instruments
Quality control instruments include pressure testing machines, gauges, and other devices for assessing physical properties.
PPR Pipe Market Trends and Challenges
Current Market Trends
The PPR pipe market is witnessing significant growth due to:
- Increased Construction Activities: Growing urbanization and infrastructure projects globally are driving demand.
- Sustainable Practices: The push for eco-friendly materials in construction supports the adoption of PPR pipes.
- Technological Advancements: Innovations in production techniques are improving efficiency and reducing costs.
Challenges in PPR Pipe Production
While the market is growing, several challenges exist:
- Raw Material Costs: Fluctuations in polypropylene prices can affect production costs.
- Competition: The market is competitive, with various materials available for plumbing solutions.
- Regulatory Compliance: Ensuring compliance with industry standards and regulations can be complex and requires continual monitoring.
Conclusion PPR Pipe
The 20-63mm PPR pipe production line is a vital aspect of the plumbing industry, offering significant advantages in durability, chemical resistance, and environmental sustainability. Understanding the production process, machinery involved, and market dynamics can help manufacturers optimize their operations and meet growing demand. By focusing on quality control and technological advancements, the PPR pipe industry can continue to thrive and innovate.
FAQs
1. What is the lifespan of PPR pipes?
PPR pipes typically last over 50 years when properly installed and maintained.
2. Are PPR pipes suitable for hot water applications?
Yes, PPR pipes can handle temperatures up to 95°C, making them suitable for hot water supply.
3. How are PPR pipes produced?
PPR pipes are produce through an extrusion process that involves heating polypropylene and shaping it through a die.
4. What are the advantages of using PPR pipes?
PPR pipes offer durability, corrosion resistance, lightweight handling, and eco-friendliness.
5. Can PPR pipes be recycled?
Yes, PPR pipes are made from recyclable materials, contributing to sustainable building practices.