Introduction PPR Pipe
The demand for high-quality piping solutions is growing rapidly due to the expansion of modern infrastructure and construction. PPR Pipe (Polypropylene Random Copolymer pipes) have emerged as a preferred choice for water supply systems because of their durability, non-corrosive properties, and ability to handle both hot and cold water. Dekuma, a leading provider of advanced extrusion technology, offers state-of-the-art PPR pipe extrusion lines that ensure efficient, reliable, and high-quality PPR pipe production.
This article explores the features, benefits, and process of Dekuma’s PPR pipe extrusion line, shedding light on why it stands out in the pipe manufacturing industry.
What is PPR Pipe
PPR pipes are made from polypropylene random copolymer, a thermoplastic material known for its superior chemical resistance, high strength, and excellent thermal properties. These pipes are used widely in residential, commercial, and industrial settings for water transportation and heating systems.
Key advantages of PPR pipes include:
- Resistance to high temperatures up to 95°C
- Anti-corrosion and non-scaling properties
- Long service life of over 50 years under optimal conditions
- Non-toxic and safe for potable water systems
- Energy-efficient production and recyclability
Overview of Dekuma’s PPR Pipe Extrusion Line
Dekuma is a globally recognized manufacturer of extrusion systems, known for its precision, innovation, and energy-efficient solutions. Their PPR pipe extrusion line is specifically designed to produce high-quality PPR pipes with consistent dimensions, smooth finishes, and superior durability.
Core Components of the Dekuma PPR Pipe Extrusion Line
- High-Performance Extruder
- The extruder is the heart of the PPR pipe production process. Dekuma’s extruder ensures consistent melting and mixing of raw materials with minimal energy consumption.
- Die Head and Moulds
- Precision-engineered die heads and moulds guarantee accurate pipe diameters and uniform wall thickness. This component plays a crucial role in ensuring the pipes meet strict international standards.
- Vacuum Calibration Tank
- The vacuum calibration tank stabilizes the shape and size of the extruded PPR pipe while maintaining its roundness and smooth surface finish.
- Cooling System
- A water-cooling system rapidly solidifies the extruded pipes, preventing warping and ensuring structural integrity.
- Haul-Off Machine
- The haul-off unit pulls the pipes consistently through the production line without deforming or stretching, ensuring uniform dimensions.
- Cutting Unit
- Automatic cutting units cut the pipes to specified lengths, typically 4 meters or customized sizes, with precision.
- Printing and Marking System
- Pipes are marked with essential details, including size, pressure rating, production date, and brand information for traceability and compliance.
- Control System
- Dekuma integrates advanced PLC (Programmable Logic Controller) systems that allow real-time monitoring and control of the extrusion process. Operators can easily adjust parameters for optimal production.
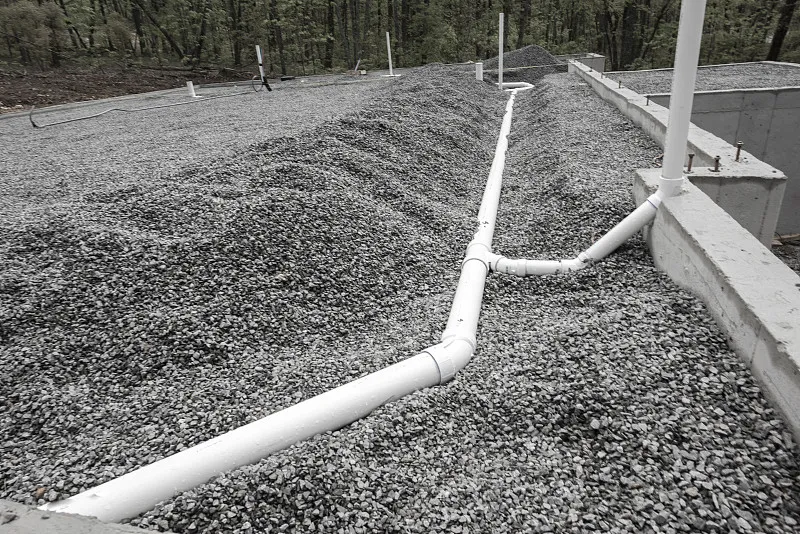
PPR Pipe Production Process Using Dekuma’s Extrusion Line
The PPR pipe production process on Dekuma’s extrusion line is efficient, streamlined, and ensures high-quality output.
1. Raw Material Feeding
- Polypropylene random copolymer granules, mixed with color pigments and stabilizers, are fed into the hopper of the extruder.
2. Extrusion Process
- Inside the extruder, the granules are melte and homogenized at temperatures between 200-250°C.
- The molten material is push through the die head, forming the desired pipe diameter and wall thickness.
3. Vacuum Calibration
- The extruded pipe passes through the vacuum calibration tank, which stabilizes the shape and dimensions of the pipe.
4. Cooling
- Pipes are cool in water tanks to solidify their structure and prevent surface imperfections.
5. Haul-Off Operation
- The haul-off unit maintains steady tension and speed, pulling the pipe smoothly through the line without deforming it.
6. Cutting and Printing
- Pipes are cut to precise lengths using an automated cutting system.
- Markings, including size, pressure class, and manufacturer details, are printe on the pipe surface for identification.
7. Final Quality Inspection
- Each pipe undergoes quality checks, including pressure testing, dimensional inspection, and surface analysis, ensuring compliance with industry standards.
8. Packaging and Storage
- Finished pipes are bundle, packed, and stored safely for transportation to end users.
Advantages of Dekuma’s PPR Pipe Extrusion Line
Dekuma’s advanced extrusion lines offer numerous benefits that set them apart in the market:
- High Precision and Quality
- Dekuma’s extrusion technology ensures pipes have uniform wall thickness, smooth surfaces, and consistent dimensions.
- Energy Efficiency
- The extrusion line is design to reduce energy consumption, making the production process more sustainable and cost-effective.
- Automation and Control
- The PLC control system allows for precise monitoring and adjustment of production parameters, minimizing human errors and optimizing output.
- Durability and Reliability
- The machinery is built with high-quality components, ensuring long-term reliability and reduced maintenance costs.
- Customizable Production
- Dekuma’s extrusion lines can produce PPR pipes in various diameters, wall thicknesses, and lengths, meeting diverse customer needs.
- Compliance with International Standards
- The pipes produced using Dekuma’s extrusion line comply with global quality standards, ensuring reliability for residential, commercial, and industrial applications.
Applications of PPR Pipe Produced by Dekuma’s Extrusion Line
PPR pipes manufactured using Dekuma’s extrusion technology are suitable for a variety of applications:
- Residential Plumbing: Hot and cold water systems in homes and apartments.
- Commercial Buildings: Centralized heating and water supply systems.
- Industrial Use: Transportation of chemicals and fluids due to the pipes’ anti-corrosion properties.
- HVAC Systems: Used in heating, ventilation, and air conditioning systems.
- Agricultural Irrigation: Reliable water delivery for agricultural systems.
Conclusion
Dekuma’s PPR pipe extrusion line represents cutting-edge technology in pipe manufacturing, offering unmatched efficiency, precision, and reliability. By utilizing advanced machinery, Dekuma ensures the production of high-quality PPR pipes that meet global standards and cater to a wide range of applications. With features like energy efficiency, automation, and rigorous quality control, Dekuma’s extrusion line is an excellent investment for manufacturers looking to produce durable and versatile PPR pipes.
Frequently Asked Questions (FAQs)
1. What is the advantage of Dekuma’s PPR pipe extrusion line?
Dekuma’s extrusion line offers high precision, energy efficiency, and automated control, ensuring the production of high-quality PPR pipes.
2. What materials are used in PPR pipe production?
PPR pipes are made from polypropylene random copolymer (PPR-C), which is non-toxic, durable, and resistant to corrosion.
3. Can Dekuma’s extrusion line produce pipes of different sizes?
Yes, Dekuma’s extrusion lines can produce PPR pipes in various diameters, wall thicknesses, and lengths to meet specific customer requirements.
4. How long do PPR pipes produced using Dekuma’s extrusion line last?
PPR pipes have a lifespan of over 50 years under proper installation and operating conditions.
5. Are PPR pipes produced by Dekuma’s machines environmentally friendly?
Yes, PPR pipes are 100% recyclable, and Dekuma’s extrusion technology is design for energy-efficient production, making it an eco-friendly choice.