When choosing piping materials for plumbing and industrial applications, PPR (Polypropylene Random Copolymer) EN 15874 and HDPE (High-Density Polyethylene) are two popular options. Both have unique properties, advantages, and limitations. Here’s a detailed comparison of PPR and HDPE pipes.
1. Material Composition
- PPR Pipes: Made from polypropylene random copolymer, PPR pipes are known for their robustness and resistance to chemicals and high temperatures.
- HDPE Pipes: Constructed from high-density polyethylene, HDPE pipes are lightweight, flexible, and resistant to corrosion and various chemicals.
2. Temperature Resistance
- PPR Pipes: Can withstand high temperatures, typically up to 95°C (203°F), making them suitable for hot water applications.
- HDPE Pipes: Generally suitable for temperatures up to around 60°C (140°F). They are not recommended for high-temperature applications.
3. Durability and Lifespan
- PPR Pipes: Have a long lifespan, often exceeding 50 years when installed correctly. They are resistant to corrosion, scaling, and fouling.
- HDPE Pipes: Also have a long lifespan, often exceeding 50 years. They are highly resistant to impact and abrasion, making them suitable for various environments.
4. Flexibility and Installation
- PPR Pipes: Rigid and less flexible, requiring specific fittings and joints, often using heat fusion methods for installation.
- HDPE Pipes: Highly flexible, which allows for easier installation, especially in tight spaces or when bending is required. They can be joined using fusion welding or mechanical fittings.
5. Pressure Rating
- PPR Pipes: Generally have high pressure ratings, making them suitable for high-pressure applications in plumbing systems.
- HDPE Pipes: Available in various pressure ratings, suitable for both low and high-pressure applications, including water supply and irrigation.
6. Chemical Resistance
- PPR Pipes: Excellent resistance to a wide range of chemicals, making them ideal for industrial applications where chemical exposure is a concern.
- HDPE Pipes: Also resistant to many chemicals, particularly corrosive substances, making them suitable for sewage and waste management applications.
7. Cost
- PPR Pipes: Typically more expensive than HDPE pipes due to the material and installation requirements.
- HDPE Pipes: Generally more cost-effective, especially for large-scale projects, due to their ease of installation and lower material costs.
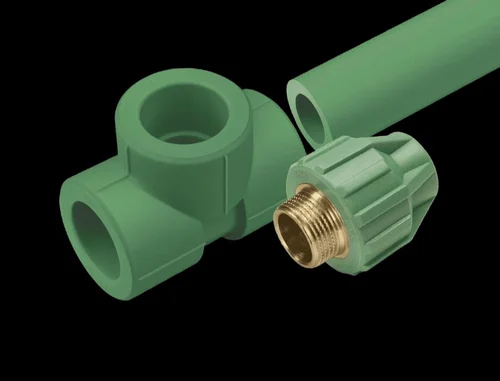
8. Applications
- PPR Pipes: Commonly used for hot and cold water supply, heating systems, and industrial applications where high temperature and pressure resistance are required.
- HDPE Pipes: Widely used in water distribution, sewage systems, irrigation, and gas distribution due to their flexibility and durability.
Comparison Table
Feature | PPR Pipes | HDPE Pipes |
---|---|---|
Material | Polypropylene | High-Density Polyethylene |
Temperature Resistance | Up to 95°C (203°F) | Up to 60°C (140°F) |
Durability | High | High |
Flexibility | Rigid | Flexible |
Pressure Rating | High | Varies (low to high) |
Chemical Resistance | Excellent | Good |
Cost | Higher | Lower |
Common Uses | Water supply, heating | Water distribution, sewage, irrigation |
Conclusion
Both PPR and HDPE pipes have their unique advantages and suitable applications. PPR pipes are ideal for high-temperature and pressure applications, while HDPE pipes offer flexibility and cost-effectiveness for various water and sewage systems. The choice between them depends on project requirements, environmental conditions, and budget considerations.