Introduction: New ASTM F3722 Standard for Polypropylene Pipes
Polypropylene pipes have gained significant traction in industries requiring durable and efficient piping solutions. The recent release of the ASTM F3722 standard marks a milestone in the development of heat fusing technologies for polypropylene pipes. This new standard outlines the methods for heat fusing polypropylene (PP) pipes, offering improved reliability and performance for a range of applications, from water systems to industrial pipelines. In this article, we explore the key aspects of the ASTM F3722 standard, how it impacts polypropylene pipes, and why heat fusion is the preferred joining method.
What Are Polypropylene Pipes?
Polypropylene (PP) pipes are a type of plastic piping commonly used in plumbing, heating, and industrial applications. Known for their high resistance to chemicals, temperature variations, and corrosion, polypropylene pipes offer an excellent alternative to traditional materials like metal or PVC. Polypropylene pipes come in a range of sizes and grades, making them suitable for various sectors, including water supply systems, chemical transportation, and industrial fluid handling.
Key Features of Polypropylene Pipes
- Corrosion Resistance: Polypropylene pipes are immune to corrosion, making them ideal for both potable water and industrial applications.
- Chemical Resistance: These pipes can withstand exposure to a variety of chemicals without degradation.
- High Temperature Resistance: PP pipes are capable of handling high temperatures, often required in hot water and industrial systems.
- Long Lifespan: Polypropylene pipes can last for decades when installed and maintained properly.
With these properties, polypropylene pipes have become the material of choice for many industries, offering significant benefits over alternatives like steel or copper.
Heat Fusion: The Preferred Method for Polypropylene Pipes Joining
Heat fusion is a critical process in the installation and maintenance of polypropylene pipes. This method involves using heat to join pipe segments, creating a strong, leak-proof bond between them. The ASTM F3722 standard focuses specifically on this process, providing guidelines to ensure a consistent and reliable bond that can handle the demands of various systems.
Benefits of Heat Fusing Polypropylene Pipes
Heat fusion is the preferred joining method for polypropylene pipes due to several advantages:
- Strong, Permanent Bond: Heat fusing creates a seamless connection between pipe segments, resulting in a joint that is as strong as the pipe itself.
- Leak-Free: The fusion process eliminates the risk of leaks, a critical factor in water and gas transport systems.
- No Need for External Fittings: Heat fusion eliminates the need for mechanical connectors, reducing the risk of failure and simplifying the installation process.
People widely use the process in a variety of applications, from residential plumbing to large-scale industrial projects, due to its efficiency and reliability.
The ASTM F3722 Standard Explained
The ASTM F3722 standard outlines the proper procedures for heat fusing polypropylene pipes. It provides clear guidelines for the equipment, techniques, and safety protocols needed to create reliable, long-lasting joints. The release of this standard marks a significant advancement in how the industry installs and maintains polypropylene pipes, ensuring a higher level of quality and consistency.
Key Components of ASTM F3722 Standard
- Fusion Parameters: The standard specifies the exact temperature, pressure, and duration required to achieve a proper fusion between pipe segments.
- Joint Quality Control: ASTM F3722 provides a framework for testing the strength and integrity of fused joints, ensuring they meet or exceed industry standards.
- Fusion Equipment Guidelines: The standard recommends the use of specific equipment, such as fusion machines and heating elements, to achieve optimal results.
- Safety Protocols: The standard includes detailed safety instructions to prevent accidents during the fusion process, ensuring that workers follow proper procedures.
By standardizing the heat fusion process, ASTM F3722 improves the overall reliability and safety of polypropylene pipe systems.
How Heat Fusion Improves Polypropylene Pipes Performance
The process of heat fusing polypropylene pipes offers a number of advantages over traditional pipe joining methods, such as threading or welding. Heat fusion creates a continuous, smooth inner surface, which reduces the likelihood of buildup or clogs within the pipe. Additionally, the strength and leak-proof nature of heat fusion joints ensure the long-term reliability of the system.
Enhanced Durability
The fused joints created by the heat fusion process are highly resistant to stresses such as pressure fluctuations, vibration, and thermal expansion. This ensures the system will remain intact and functional for many years, even under harsh conditions.
Reduced Maintenance Costs
Because heat fusion creates a permanent bond, there is no need for ongoing maintenance to prevent leaks or joint failure. This significantly reduces maintenance costs over the lifetime of the system.
Improved Flow Efficiency
The smooth, uninterrupted surface created by heat fusion also improves the flow of liquids or gases through the system. With fewer obstacles to flow, the system operates more efficiently, saving energy and reducing operational costs.
Applications of Heat-Fused Polypropylene Pipes
People use heat-fused polypropylene pipes in a wide range of applications across various industries. These pipes commonly appear in both residential and commercial plumbing systems, as well as in industrial processes that require durable and chemically resistant piping solutions.
Residential and Commercial Plumbing
In plumbing systems, heat-fused polypropylene pipes are used for both hot and cold water distribution. The pipes’ high-temperature resistance makes them ideal for hot water systems, while their chemical resistance ensures they are safe for potable water applications.
Industrial Fluid Handling
In industrial environments, people use polypropylene pipes to transport chemicals, acids, and other harsh substances. The ability to heat-fuse these pipes ensures a tight seal that withstands the corrosive effects of the chemicals being transported.
Wastewater and Drainage Systems
People also use polypropylene pipes in wastewater and drainage systems due to their excellent resistance to corrosion and chemicals. Heat fusion helps create secure joints, preventing leaks and improving the overall reliability of the system.
Gas and Oil Transport
People are increasingly using polypropylene pipes to transport natural gas and oil, especially in systems that require high resistance to both temperature and chemicals. Heat fusion is critical in ensuring the integrity of these pipelines.
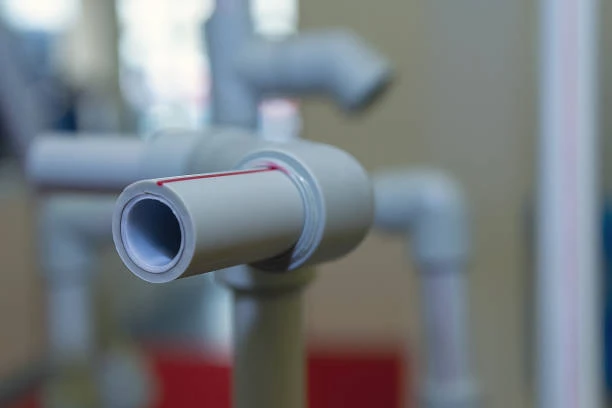
Training and Certification for Heat Fusion Process
To ensure proper implementation of the ASTM F3722 standard, employers must train workers in the heat fusion process. Proper training ensures that workers perform the fusion correctly, resulting in high-quality joints that meet or exceed performance standards.
Certification Programs for Fusion Technicians
Various organizations offer certification programs for polypropylene pipe fusion technicians, ensuring that they are well-versed in the latest techniques and standards. These programs typically cover:
- Fusion Equipment Operation: Training on how to operate heat fusion machines and associated equipment.
- Fusion Process Protocols: Instruction on the correct parameters for heat, pressure, and time to achieve a reliable bond.
- Joint Inspection and Testing: Training on how to inspect fused joints for quality and integrity.
Certified technicians help ensure the successful application of the ASTM F3722 standard, contributing to the longevity and safety of the pipe systems they install.
Conclusion: The Future of Polypropylene Pipes Technology
The release of the ASTM F3722 standard represents a significant advancement in the technology surrounding polypropylene pipes and heat fusion.
As demand for high-quality, durable piping systems continues to grow, polypropylene pipes and heat fusion technology will play an increasingly important role in meeting the needs of industries worldwide. With the ASTM F3722 standard setting the bar for best practices, the future of polypropylene pipe systems looks bright.
Frequently Asked Questions (FAQs)
- What is heat fusion for polypropylene pipe?
Heat fusion is a process where heat is applied to melt the ends of polypropylene pipe and join them together, creating a strong, leak-proof bond. - Why is the ASTM F3722 standard important?
The ASTM F3722 standard provides clear guidelines for the heat fusion process, ensuring that polypropylene pipe systems are installed reliably and safely. - What are the main benefits of heat fusion?
Heat fusion offers a strong, durable joint that is resistant to leaks, corrosion, and environmental stress, improving the overall performance of polypropylene pipe systems. - Can polypropylene pipe be used for gas transportation?
Yes, polypropylene pipe are increasingly used in natural gas transportation systems due to their resistance to high temperatures and chemicals. - How can I become certified to perform heat fusion on polypropylene pipe?
Certification programs for heat fusion technicians are available through various organizations and provide training in fusion techniques, equipment, and safety protocols.