Introduce PPR Pipe
When it comes to plumbing systems, the strength, reliability, and long-term performance of the pipes and fittings are critical to the overall success of any installation. One of the most common materials used for plumbing systems is Polypropylene Random Copolymer (PPR) due to its exceptional resistance to high temperatures, pressure, and corrosion. To ensure that PPR Pipe and fittings are securely connected, professionals rely on specialized welding equipment. One such tool is the Spider™ 125 Series 2, a high-performance welding machine designed specifically for PPR pipes and fittings. In this article, we will delve into the importance of heating and fusing PPR pipe and fittings, how the Spider™ 125 Series 2 works, and tips for achieving the best welding results.
Introduction: Why Proper Heating and Fusing of PPR Pipe is Essential
Properly welding PPR pipes and fittings is a crucial step in ensuring that plumbing systems are leak-proof, durable, and efficient. The fusion process involves heating the PPR material until it becomes soft enough to bond with another piece of PPR, creating a seamless connection that will last for decades. Achieving this process requires the right equipment, temperature control, and technique.
The Spider™ 125 Series 2 is an advanced welding machine designed to heat and fuse PPR pipes and fittings with precision. By utilizing the proper heating and fusion technique, you can ensure strong, leak-resistant joints that will stand the test of time.
What is the Spider™ 125 Series 2?
The Spider™ 125 Series 2 is a high-quality welding machine that has been specifically designed for fusing PPR pipes and fittings. It is well-known in the industry for its accuracy, reliability, and ease of use, making it a top choice for professionals working with PPR pipe installations. The machine’s robust design and features enable it to handle a wide range of pipe sizes, from smaller residential applications to larger commercial and industrial projects.
Key Features of the Spider™ 125 Series 2:
- Digital Temperature Control: Ensures that the welding machine maintains a consistent temperature within the optimal range (typically 260°C to 280°C), which is critical for achieving high-quality fusion.
- Quick Heat-Up Time: The Spider™ 125 Series 2 heats up rapidly, allowing professionals to start welding quickly and efficiently, improving overall productivity.
- Wide Range of Pipe Sizes: Capable of welding PPR pipes and fittings ranging from 20mm to 125mm, making it a versatile tool for various projects.
- Ergonomic Design: The machine is designed for comfort and ease of use, reducing operator fatigue during long hours of work.
- Precision Welding Plates: The Spider™ 125 Series 2 comes with high-quality welding plates that ensure even heat distribution for optimal fusion results.
The Welding Process: Heating and Fusing PPR Pipe & Fittings
The process of heating and fusing PPR pipes and fittings involves several crucial steps that ensure a successful and durable joint. The Spider™ 125 Series 2 simplifies this process with its advanced features. Below, we’ll break down the essential steps for heating and fusing PPR pipes and fittings using this machine.
Step 1: Preparing the Pipe and Fitting
Before starting the welding process, ensure that both the PPR pipe and fitting are clean and free from any dirt, grease, or moisture. Contaminants on the surface can prevent proper fusion and weaken the joint.
Trick for Success:
- Use a clean cloth to wipe the ends of the pipe and fitting.
- Check that both the pipe and fitting are dry and free from any debris.
Step 2: Set the Temperature on the Spider™ 125 Series 2
To begin the welding process, set the Spider™ 125 Series 2 to the desired temperature. The optimal temperature for welding PPR pipes is usually around 260°C to 280°C.
Tip for Accuracy:
- Ensure that the welding machine is calibrated and set to the correct temperature before starting. Too low a temperature will result in weak fusion, while too high a temperature can burn the material and cause damage.
Step 3: Insert the Pipe and Fitting into the Welding Machine
Place the pipe and fitting into the heating plates of the Spider™ 125 Series 2. The machine’s plates are designed to heat both the pipe and fitting evenly, ensuring that the fusion process occurs at the molecular level.
Important Note:
- Make sure that the pipe and fitting are inserted properly, with the pipe flush against the heating plate and the fitting aligned with the other plate. Misalignment can cause uneven fusion, leading to weak joints.
Step 4: Heat the Pipe and Fitting
Allow the pipe and fitting to heat for the specified amount of time. The heating time varies depending on the size of the pipe and fitting. For example, smaller pipes (20mm to 40mm) may require around 4 to 6 seconds of heating, while larger pipes (up to 125mm) may need up to 12-15 seconds.
Tip for Timing:
- Check the manufacturer’s guidelines for the correct heating time based on pipe size and thickness. Timing is crucial to achieving a strong, reliable bond.
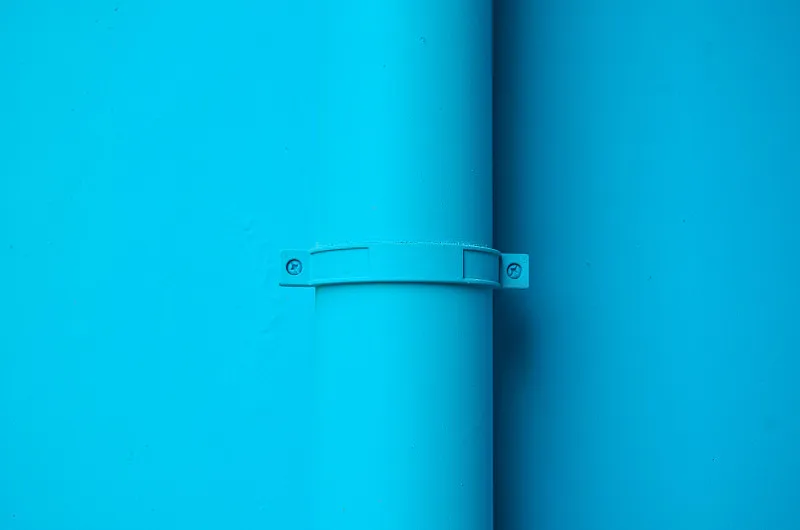
Step 5: Remove and Fuse the Pipe and Fitting
Once the pipe and fitting have been heated to the optimal temperature, remove them from the heating plates and immediately push the pipe and fitting together. Hold them in place for a few seconds to allow the materials to fuse properly.
Trick for Success:
- Apply consistent pressure to ensure that the pipe and fitting are aligned and remain firmly in place during the fusion process. This pressure helps create a strong bond between the two components.
Step 6: Cooling and Final Adjustment
After the fusion, it’s crucial to allow the joint to cool naturally. Cooling too quickly can result in weak points or cracks in the joint. During the cooling process, do not disturb the joint, as it may compromise the integrity of the fusion.
Tip:
- Allow at least 5-10 minutes for the joint to cool before testing or moving the pipe.
Why the Spider™ 125 Series 2 is Ideal for PPR Welding
The Spider™ 125 Series 2 offers several advantages over other welding machines on the market, particularly when it comes to PPR pipe welding.
1. Precision and Accuracy
The digital temperature control feature ensures that the machine maintains the correct temperature, reducing the risk of overheating or underheating the pipes. The precise temperature control is especially important for larger pipe sizes, which require more time and heat for optimal fusion.
2. Versatility
The Spider™ 125 Series 2 is versatile, capable of welding a wide range of pipe sizes. From small residential systems to larger commercial projects, this machine handles it all, making it a great investment for professionals.
3. Durability
This welding machine is built to last. Its robust construction and high-quality components ensure long-term use, even in demanding environments.
4. Enhanced Efficiency
The quick heat-up time and consistent performance ensure that the welding process is efficient, reducing downtime and allowing professionals to complete projects faster.
Common Mistakes to Avoid When Using the Spider™ 125 Series 2
While the Spider™ 125 Series 2 is an advanced machine designed for ease of use, there are still some common mistakes that can affect the quality of the fusion. Here are a few to avoid:
- Incorrect Pipe and Fitting Alignment: Misalignment can cause uneven fusion, leading to weak joints. Always ensure the pipe and fitting are perfectly aligned before beginning the welding process.
- Not Following Heating Time Guidelines: Overheating or underheating the pipe and fitting can result in poor fusion. Always follow the manufacturer’s recommended heating times based on pipe size.
- Skipping the Cleaning Process: Failing to clean the pipe and fitting before welding can lead to contamination and a weak joint. Make sure to clean both components thoroughly before starting the fusion.
- Not Allowing Proper Cooling Time: Cooling too quickly can cause the joint to crack. Allow enough time for the joint to cool naturally before testing it.
Conclusion: Mastering the Spider™ 125 Series 2 for Perfect PPR Pipe Welding
Using the Spider™ 125 Series 2 to heat and fuse PPR pipes and fittings is an efficient and reliable way to create long-lasting, leak-proof plumbing systems. By following the correct procedures and using the machine’s features effectively, you can ensure strong, durable joints every time. Whether you’re working on a small residential project or a large-scale commercial installation, the Spider™ 125 Series 2 will help you achieve the best results with minimal hassle.
Frequently Asked Questions (FAQs)
1. How long should I heat a PPR pipe and fitting using the Spider™ 125 Series 2?
Heating time varies by pipe size, typically ranging from 4 to 6 seconds for smaller pipes and 12-15 seconds for larger pipes. Always refer to the manufacturer’s guidelines for precise timing.
2. What is the ideal temperature for welding PPR pipes with the Spider™ 125 Series 2?
The ideal welding temperature for PPR pipes is between 260°C and 280°C. Make sure to adjust the temperature based on the pipe size and thickness.
3. Can the Spider™ 125 Series 2 weld pipes larger than 125mm?
No, the Spider™ 125 Series 2 is designe to weld PPR pipes up to 125mm. For larger pipes, a different model may be neede.
4. How do I know if the pipe and fitting are properly aligne?
Ensure the pipe is flush against the heating plate and the fitting is aligne correctly. Use alignment tools or clamps to help hold them in place during the welding process.
5. How long should I wait for the joint to cool after welding?
Allow the joint to cool for at least 5-10 minutes before testing or moving the pipe to ensure the fusion is strong and stable.